Understanding Aluminum Alloys: Types, Properties, and Applications
- VIA INDIGOS
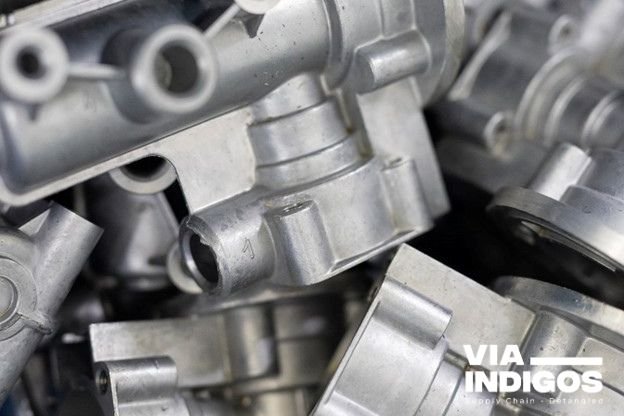
When creating something extraordinary, whether it’s a cutting-edge aerospace part, a sleek automotive component, or durable building materials, the choice of material is key. Enter aluminum alloys, the superheroes of modern aluminium manufacturing. They’re lightweight, durable, and versatile, making them a favorite in industries that demand high performance and reliability.
But what makes these materials so special? And how do you choose the right one for your needs? Let’s dive into the world of aluminum alloys to understand their types, properties, and applications.
Why Aluminum Alloys Dominate Manufacturing
It’s no accident that aluminum is one of the most widely used metals. Pure aluminum is lightweight, corrosion-resistant, and easy to work with, but when combined with other elements, it transforms into an alloy with tailored properties for specific applications.
Think of it like customizing a recipe: by adding the right “ingredients” like magnesium, silicon, or copper, you get a material that’s stronger, more flexible, or better suited to extreme conditions. The result? A metal that’s as adaptable as your imagination.
Types of Aluminum Alloys: What You Need to Know
Here’s a breakdown of the most popular aluminum alloy series and where they shine:
1XXX Series: Pure Aluminum
This series is as pure as it gets, 99% or more aluminum. It’s known for its high corrosion resistance and excellent conductivity, but it’s not the strongest option. Think of it as the go-to for applications where reliability and resistance to rust are key.
The primary and most impactful versions available in this alloy series are;
- 1100: Excellent corrosion resistance, high thermal and electrical conductivity, easily formable.
- 1350: Superior electrical conductivity, often used for electrical conductors.
When one thinks about industries that rely on aluminum alloys, a few stand out for their incredible demand for strength, durability, and performance:
- Electrical and Power: Ideal for electrical cables and conductors due to high conductivity.
- Food and Beverage: Valued for food processing and packaging equipment for its corrosion resistance.
- Chemical Processing: Essential for tanks and equipment requiring chemical inertness.
- Aerospace: Perfect for fuel tanks, thanks to its lightweight and non-reactive properties.
2XXX Series: Aluminum-Copper
This series offers high strength but trades off some corrosion resistance. It’s the choice for industries like aerospace and automotive, where durability under pressure is non-negotiable.
The most relevant divisions within the alloy series are;
- 2024: High strength-to-weight ratio, excellent fatigue resistance; commonly used in aerospace.
- 2219: High strength and excellent corrosion resistance in high-temperature environments.
Aluminum alloys play a pivotal role across industries where strength, durability, and performance are non-negotiable:
- Aerospace: For aircraft structures, fuselage, and wing components.
- Automotive: Ideal for high-strength structural parts and performance vehicles.
- Defense: Used in high-performance military equipment.
- Sports and Recreation: Found in competitive sports equipment like bicycles and racing gear.
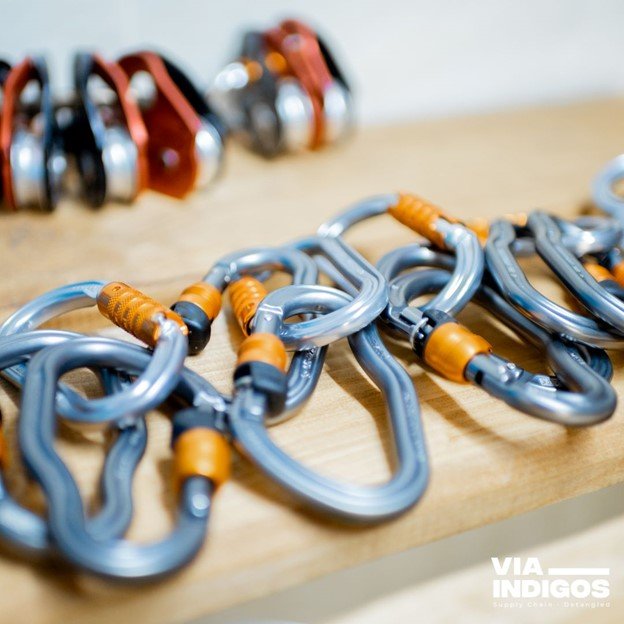
Carabiners designed for mountain climbing safety
3XXX Series: Aluminum-Manganese
For applications that need a balance of strength and corrosion resistance, 3XXX alloys deliver. They’re easy to form and are commonly found in everyday products.
The primary and most impactful options available in the alloy series are:
- 3003: Good corrosion resistance, widely used in roofing and siding.
- 3105: Slightly higher strength than 3003, suitable for residential sidings and mobile homes.
Aluminum alloys seamlessly integrate into diverse industries, offering unmatched functionality and reliability:
- Construction: Perfect for roofing, siding, and architectural panels.
- Packaging: Widely used in beverage cans and food containers.
- Household Goods: Found in cookware, appliances, and utensils.
- Automotive: Essential for radiators and other cooling system components.
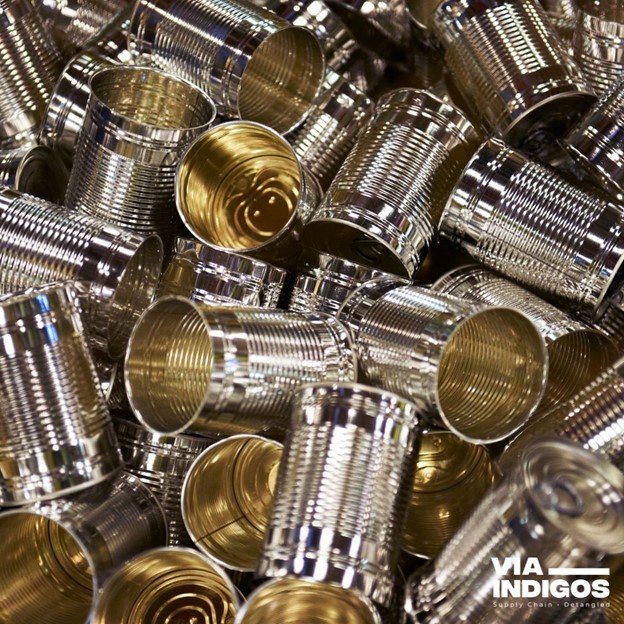
Sleek and recyclable aluminum cans in focus
4XXX Series: Aluminum-Silicon
If your project involves high temperatures or wear-and-tear, 4XXX alloys are your solution. These alloys can handle tough conditions while maintaining their integrity.
Highlighting the most significant versions of the material under this alloy series:
- 4032: High strength, wear resistance, and low thermal expansion; used in engine components.
- 4045: Excellent heat resistance, used in brazing applications like heat exchangers.
Aluminum alloys excel in industries demanding exceptional heat resistance and durability under challenging conditions:
- Automotive: Used in engine components, pistons, and cylinder heads.
- Aerospace: Ideal for heat-resistant structural parts.
- Manufacturing: Perfect for tools and equipment with high wear resistance.
- Industrial Applications: Essential for brazing materials in heat exchangers and HVAC systems
5XXX Series: Aluminum-Magnesium
When you think of marine-grade aluminum, think 5XXX. These alloys are incredibly resistant to corrosion, especially in saltwater environments.
The primary and most impactful versions available in this alloy series are;
- 5052: Excellent corrosion resistance, suitable for marine environments and fuel tanks.
- 5083: Exceptional performance in extreme environments; used in marine and aerospace applications.
- 5754: Good corrosion resistance, often used in pressure vessels.
Aluminum alloys demonstrate remarkable versatility, excelling in applications where strength and corrosion resistance are crucial:
- Marine: Essential for ships, boats, and offshore structures due to saltwater corrosion resistance.
- Transportation: Ideal for fuel tanks and truck trailers.
- Industrial Equipment: Used in storage tanks and pressure vessels.
- Aerospace: Perfect for lightweight structural components exposed to moisture.
Consumer Electronics: Widely used in enclosures for computers and portable devices.
6XXX Series: Aluminum-Magnesium-Silicon
The jack-of-all-trades. This series combines strength, corrosion resistance, and machinability, making it one of the most popular choices across industries.
The most relevant divisions within the alloy series.
6061-T6 Aluminum:
- High strength and excellent corrosion resistance.
- Common for aerospace fittings, bicycle frames, and pressure vessels.
6063 Aluminum:
- Moderate strength with superior formability.
- Used in piping, railings, and decorative products.
Aluminum alloys offer unparalleled adaptability, making them a cornerstone material in numerous industries:
- Construction: Used for window frames, doors, and structural supports.
- Automotive: Ideal for frames, body panels, and engine components.
- Aerospace: Essential for fittings and lightweight structural parts.
- Consumer Products: Found in furniture and bicycle frames.
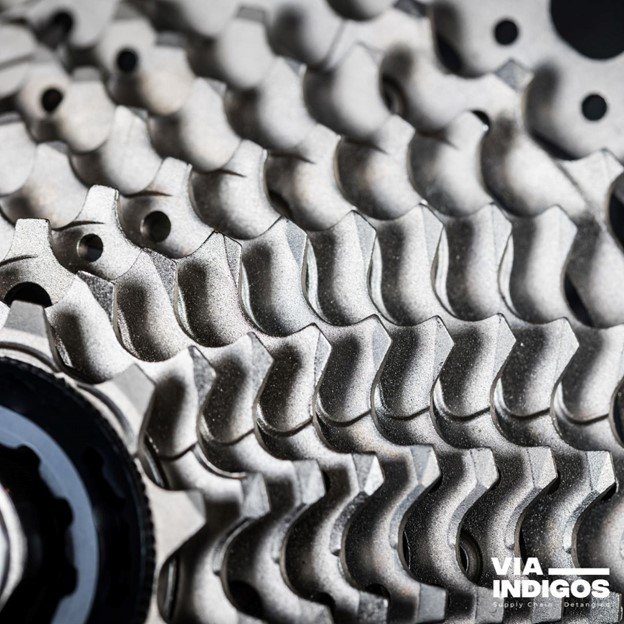
Aluminum bicycle rear cassette components built for strength and smooth functionality.
7XXX Series: Aluminum-Zinc
When performance and strength are non-negotiable, 7XXX alloys step in. These are high-strength alloys used in aerospace and competitive sports.
The primary and most impactful options available in the alloy series are:
7075-T6 Aluminum:
- Comparable in strength to steel, with good fatigue resistance but lower corrosion resistance.
- Used in aerospace frames, tooling, and structural parts.
7050 Aluminum:
- Excellent corrosion resistance and fracture toughness.
- Common in aerospace structural parts and rock climbing equipment.
Aluminum alloys are indispensable in industries where strength, precision, and performance are paramount:
- Aerospace: High-strength structural parts, wings, and fuselage components.
- Sports and Recreation: Premium bicycles and climbing equipment.
- Automotive: Racing car frames and high-performance gears.
- Tooling: Molds and precision tools.
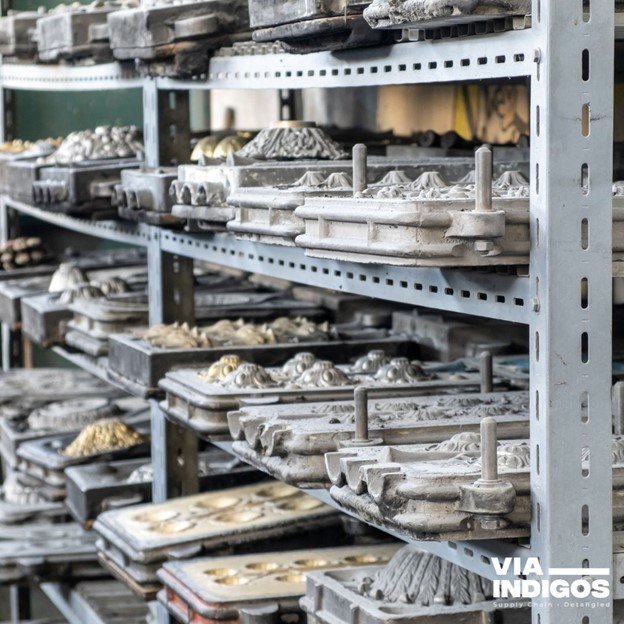
High-quality aluminum molds engineered for durability, precision, and versatility in producing a wide range of components.
Specialty Aluminum: MIC-6
A precision-cast aluminum alloy, MIC-6 is celebrated for its dimensional stability and machinability, making it ideal for applications requiring tight tolerances.
Aluminum alloys excel in industries demanding exceptional heat resistance and durability under challenging conditions:
- Precision Manufacturing: Jigs, fixtures, and tools for high-tolerance machining.
- Robotics: Components requiring stability and precision.
- Medical Devices: Equipment needing tight tolerances and deformation resistance.
- Aerospace and Automotive: Tooling and prototypes for production processes.
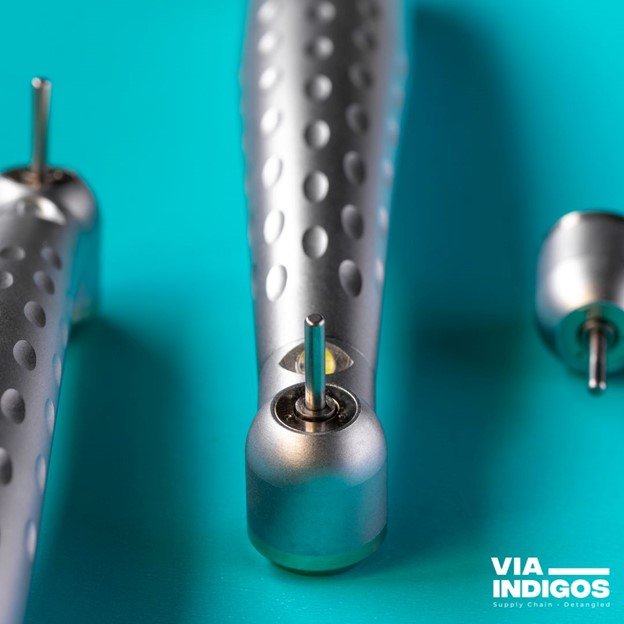
Durable and lightweight aluminum dental handpieces
Conclusion
Choosing the Right Aluminum Alloy
Selecting the right alloy depends on your application’s requirements:
- For corrosion resistance: Consider 1XXX or 5XXX
- For high strength: Look to 2XXX, 6XXX, or 7XXX
- For machinability: 6061, 6063, and MIC-6
- For high temperature or wear resistance: Opt for 4XXX
By thoroughly understanding the unique strengths and limitations of each aluminum alloy, you can make well-informed decisions that optimize performance, enhance durability, and ensure the success and longevity of your projects across various applications.
The Benefits of Aluminum Alloys
Why do so many industries rely on aluminum alloys?
It’s not just one standout feature, it’s the unique combination of characteristics that make them one of the most versatile materials available. From aerospace to everyday consumer goods, aluminum alloys deliver performance, durability, and sustainability in ways few other materials can match. Here’s a closer look at the key benefits:
1. Lightweight and Strong
Aluminum alloys strike the ideal balance between being lightweight and incredibly strong, which is why they’re favored in industries where weight reduction is critical.
- Applications: Aerospace engineers rely on aluminum to reduce the weight of aircraft, enabling better fuel efficiency and performance. Similarly, automakers use it to create lighter vehicles that meet stringent fuel economy standards without compromising on safety.
- Why It Matters: This unique strength-to-weight ratio makes aluminum alloys indispensable for industries focused on efficiency and mobility, ensuring products are both functional and cost-effective.
2. Corrosion Resistance
Aluminum naturally forms a protective oxide layer that makes it highly resistant to corrosion. When alloyed with other elements, this resistance is further enhanced, making aluminum alloys ideal for use in harsh environments.
- Applications: Marine industries benefit from aluminum alloys that can withstand saltwater corrosion, while construction projects utilize these materials for roofing, siding, and structural components exposed to the elements.
- Why It Matters: Corrosion resistance means longer-lasting products, reduced maintenance costs, and improved performance in demanding environments, from coastal regions to industrial settings.
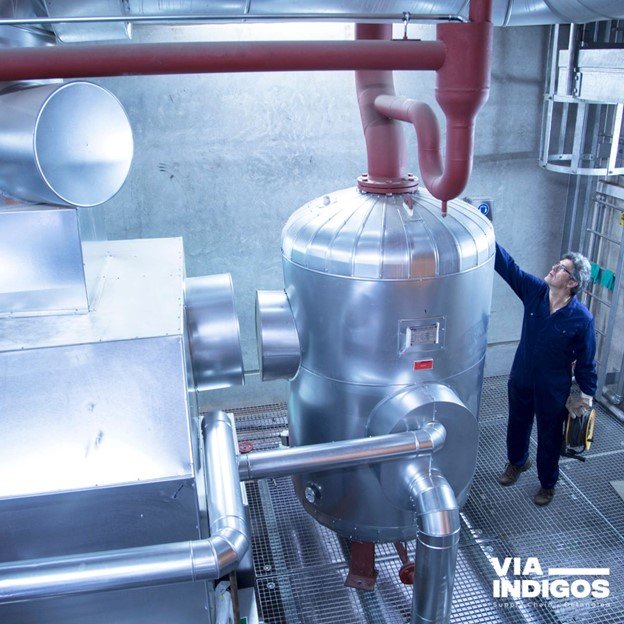
High-performance aluminum tanks, designed for durability, corrosion resistance, and optimal functionality
3. Customizable Properties
One of the standout features of aluminum alloys is their ability to be tailored for specific applications. By carefully selecting alloying elements like magnesium, silicon, or copper, manufacturers can create materials with precise characteristics.
- Applications: Need heat-resistant components? Look to Series 4XXX. Want lightweight strength for structural applications? Series 6XXX delivers. Whatever the need, there’s an aluminum alloy designed to meet it.
- Why It Matters: Customization allows manufacturers to meet strict design and performance standards without over-engineering, ensuring efficiency in both production and application.
4. Recyclable and Sustainable
Aluminum is one of the most environmentally friendly metals, as it can be recycled indefinitely without losing its properties. Recycling aluminum also requires only 5% of the energy needed to produce it from raw materials, making it a cost-effective and sustainable choice.
- Applications: From beverage cans to automotive parts, aluminum alloys are integral to circular economies that prioritize sustainability.
- Why It Matters: As industries strive to reduce their carbon footprint, aluminum alloys offer a way to create high-performance products while contributing to sustainability goals.
5. High Thermal and Electrical Conductivity
Aluminum alloys excel at conducting heat and electricity, especially in their pure form. This makes them essential in applications where efficient energy transfer is critical.
- Applications: Power transmission lines, heat exchangers, and electronic components like heat sinks and casings.
- Why It Matters: This combination of thermal and electrical efficiency ensures optimal performance in energy systems and electronics, supporting innovation across industries.
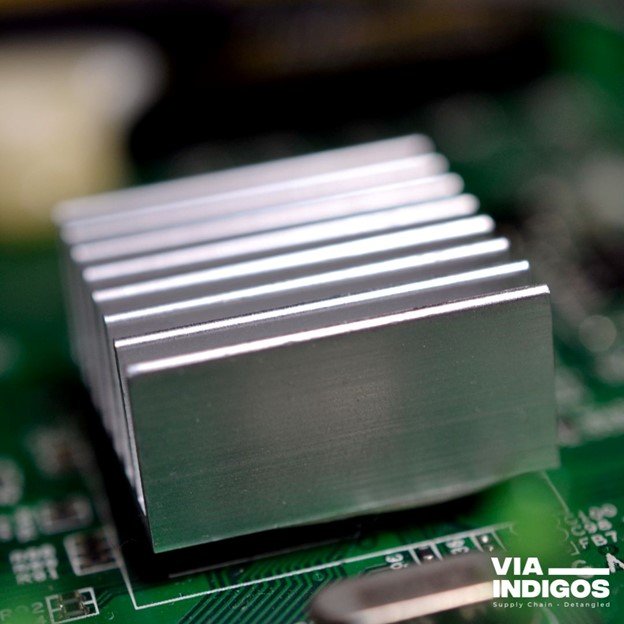
Close-up of an aluminium circuit board in detail
6. Easily Machined and Fabricated
Aluminum alloys are known for their machinability, meaning they can be easily shaped, formed, or joined using various techniques. Whether you’re rolling it into thin sheets, extruding it into complex profiles, or welding it into robust structures, aluminum alloys simplify the manufacturing process.
- Applications: Construction, transportation, and consumer goods manufacturing.
- Why It Matters: Ease of fabrication reduces production costs and timelines, making aluminum alloys a practical choice for large-scale projects and custom designs alike.
7. Exceptional Durability
Despite being lightweight, aluminum alloys are incredibly durable and resistant to wear and tear. Many alloys are designed to handle extreme conditions, such as high pressure, impact, and temperature changes.
- Applications: Aerospace components, automotive frames, and industrial equipment all rely on this durability to perform reliably under stress.
- Why It Matters: Durability ensures that products last longer, reducing the need for frequent replacements and saving both time and money in the long run.
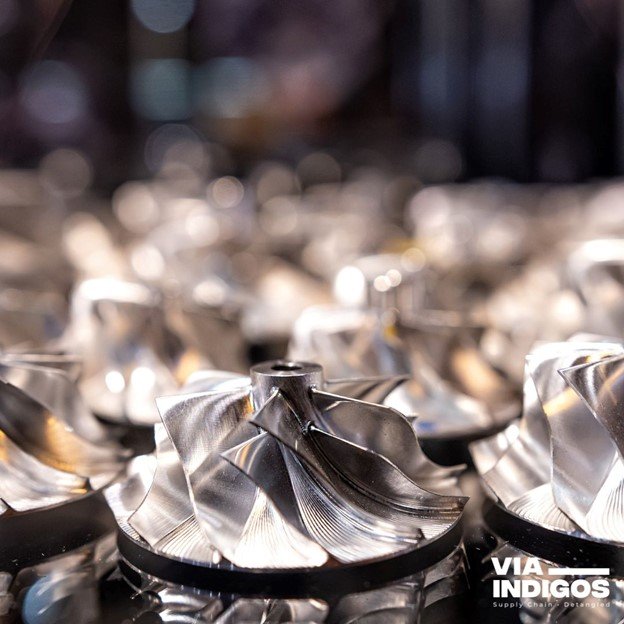
Close-up of high-quality aluminum components, engineered for durability and strength in various applications.
Aluminum alloys offer a rare combination of performance, versatility, and sustainability, making them an invaluable resource for manufacturers and designers. Whether you’re creating lightweight components for transportation, corrosion-resistant materials for marine environments, or energy-efficient systems for electronics, aluminum alloys deliver unmatched benefits.
By understanding these advantages, businesses can leverage aluminum alloys to innovate, reduce costs, and meet the evolving demands of their industries.
How Aluminum Alloys Fit Into Your Supply Chain
If you’re looking to improve your supply chain, aluminum alloys can play a critical role. Their durability and versatility mean fewer replacements and repairs, while their recyclability helps you reduce waste and meet sustainability goals.
At VIA INDIGOS, we understand that every project is unique. That’s why we don’t just supply aluminum alloys; we help you optimize their use. From selecting the right alloy to streamlining production, we ensure your project runs smoothly from start to finish.
Common Applications of Aluminum Alloys
Aluminum alloys are the unsung heroes behind some of the most innovative and high-performing products across industries. Thanks to their unmatched combination of strength, lightweight properties, corrosion resistance, and versatility, aluminum alloys have revolutionized the way we design and manufacture. Here’s an in-depth look at how they’re shaping various sectors:
1. Aerospace: Reaching New Heights
In aerospace, every gram counts. Aluminum alloys, particularly the high-strength Series 2XXX and 7XXX, are indispensable for reducing weight while maintaining structural integrity.
- Applications:
- Aircraft fuselages and frames: Lightweight yet durable for efficient flight.
- Wings and control surfaces: Ensure stability and maneuverability.
- Spacecraft components: High-performance alloys that can withstand extreme conditions.
- Why They’re Used: The exceptional strength-to-weight ratio and resistance to fatigue make aluminum alloys ideal for both commercial and military aviation.
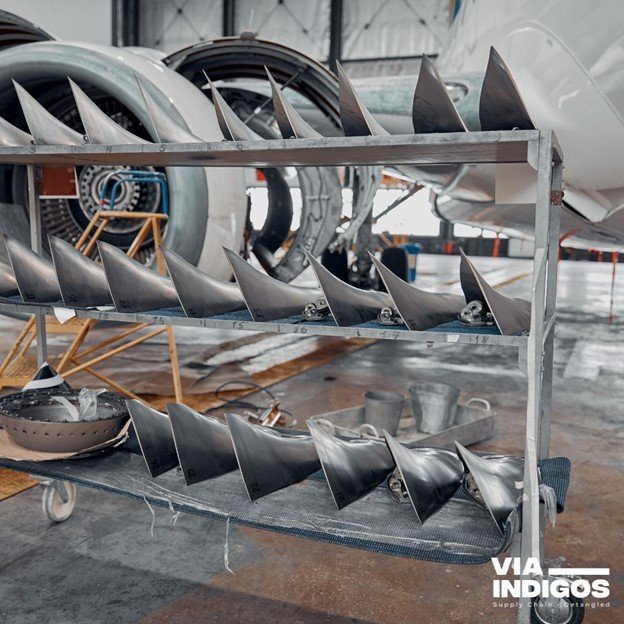
Aluminum Alloys: Powering the Future of Aerospace
2. Automotive: Driving Efficiency and Sustainability
Aluminum alloys are playing a key role in the shift toward fuel-efficient and electric vehicles. By replacing heavier steel components with lightweight aluminum, manufacturers are achieving better mileage and performance.
- Applications:
- Engine blocks and pistons: Series 4XXX alloys for heat resistance and durability.
- Body panels: Series 6XXX alloys for strength and corrosion resistance.
- Wheels and suspension parts: Lightweight solutions for improved handling and performance.
- Why They’re Used: Aluminum alloys reduce vehicle weight without compromising safety or performance, supporting the automotive industry’s push for sustainability and efficiency.
3. Construction: Building a Better Future
From skyscrapers to residential homes, aluminum alloys have become a staple in modern construction. Their resistance to corrosion, aesthetic versatility, and ease of fabrication make them a natural choice for architects and builders.
- Applications:
- Window frames and doors: Durable and weather-resistant Series 6XXX alloys.
- Roofing and siding: Series 3XXX for cost-effective, corrosion-resistant solutions.
- Structural components: Lightweight materials for bridges and large-scale infrastructure.
- Why They’re Used: Aluminum alloys deliver long-term performance while maintaining a sleek, modern appearance, making them a favorite in urban design and construction.
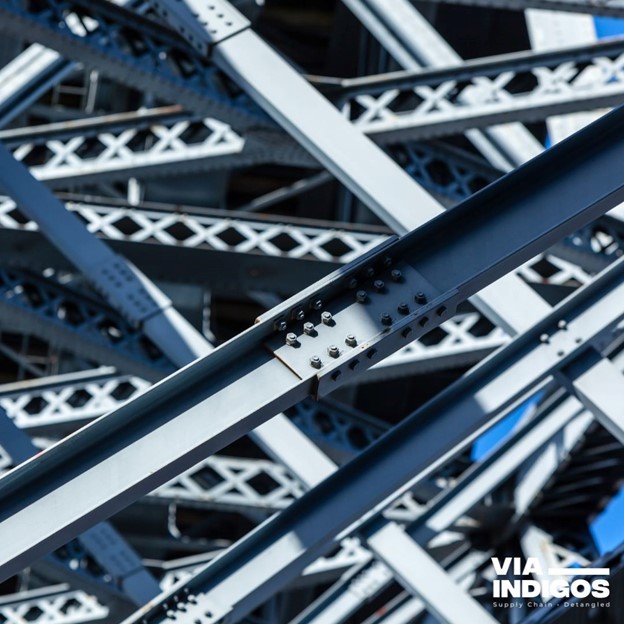
Steel beams: the backbone of durable and reliable construction
4. Marine: Tackling the Toughest Environments
The marine industry demands materials that can endure harsh, saltwater environments. Aluminum-magnesium alloys (Series 5XXX) are perfectly suited for this challenge, offering superior corrosion resistance and strength.
- Applications:
- Ship hulls: Lightweight yet robust materials for durability and efficiency.
- Offshore equipment: Resistant to saltwater corrosion for oil rigs and wind farms.
- Marine hardware: Long-lasting components like ladders and rails.
- Why They’re Used: The ability to resist saltwater corrosion without heavy maintenance makes aluminum alloys a cost-effective solution for marine applications.
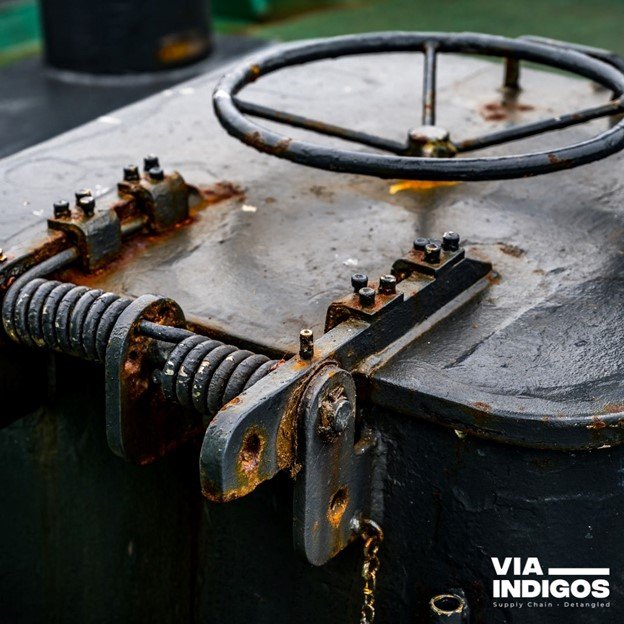
Built to withstand the harshest waters—aluminum alloys keeping marine engineering afloat.
5. Electronics and Electrical: Powering Modern Life
Aluminum’s excellent conductivity and lightweight properties make it a standout material in electronics and electrical engineering.
- Applications:
- Power transmission lines: Series 1XXX for its high conductivity.
- Heat sinks and casings: Dissipate heat effectively in electronic devices.
- Consumer electronics: Lightweight enclosures for laptops, phones, and tablets.
- Why They’re Used: Aluminum alloys ensure efficient thermal and electrical performance, while their lightweight nature supports portability in consumer electronics.
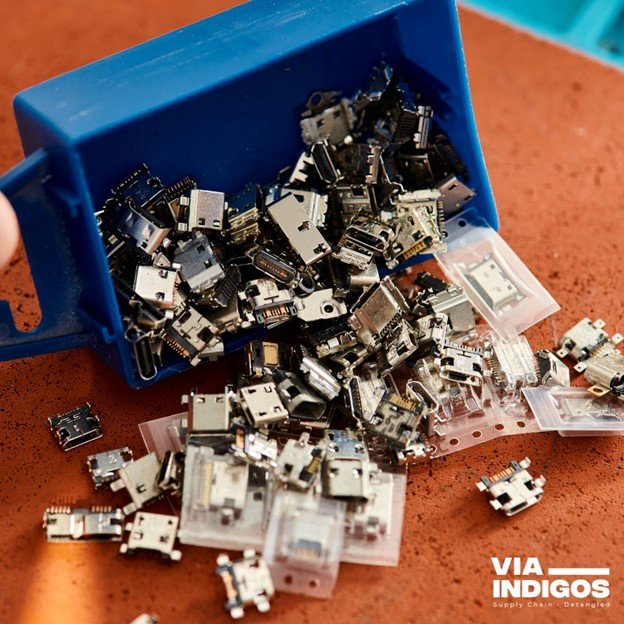
Precision-engineered aluminum components for the electronics industry
6. Consumer Goods: Everyday Innovation
Aluminum alloys are everywhere, from your kitchen to your favorite recreational activities. They combine functionality with style, making them a key material for consumer products.
- Applications:
- Beverage cans: Series 3XXX for corrosion resistance and ease of recycling.
- Sporting equipment: Series 7XXX for lightweight, high-performance bicycles and gear.
- Cookware: Non-reactive and heat-conductive materials for pots and pans.
- Why They’re Used: The combination of aesthetic appeal, durability, and sustainability makes aluminum alloys a no-brainer for consumer goods manufacturers.
7. Renewable Energy: Supporting a Sustainable Future
As industries move toward greener solutions, aluminum alloys are making an impact in renewable energy sectors.
- Applications:
- Solar panel frames: Lightweight and corrosion-resistant.
- Wind turbine components: Durable materials for offshore and onshore turbines.
- Battery casings: Safe, lightweight housing for energy storage systems.
- Why They’re Used: Aluminum alloys support the renewable energy industry with their durability, resistance to environmental factors, and ability to withstand extreme weather conditions.
Tailoring Aluminum Alloys to Your Industry
No matter your industry, aluminum alloys offer a level of versatility that’s hard to match. These alloys can be tailored to meet highly specific requirements, making them the go-to material for countless applications. Whether you’re designing components that need to withstand extreme heat, resist corrosion in harsh environments, or provide exceptional strength without adding unnecessary weight, there’s an aluminum alloy that fits the bill.
The beauty of aluminum alloys lies in their adaptability. For instance, in industries like aerospace and automotive, where every ounce counts, lightweight yet strong alloys play a crucial role in improving fuel efficiency and overall performance. In the marine and construction sectors, corrosion resistance becomes a top priority, ensuring longevity and reducing maintenance costs. Meanwhile, consumer goods manufacturers appreciate the machinability and recyclability of aluminum, which make it both cost-effective and sustainable.
By understanding the properties of different alloys, businesses can align material choices with their specific goals, whether that means optimizing for durability, appearance, or environmental impact. The right alloy doesn’t just enhance a product’s performance; it can also streamline production processes and contribute to long-term cost savings.
No matter the challenge, be it extreme temperatures, high-pressure environments, or complex designs, aluminum alloys provide a solution that’s as versatile as the industries they serve. Leveraging their unique characteristics ensures a product that not only performs well but stands the test of time.
Why Work with Via Indigos?
When it comes to contract manufacturing and supply chain management, the choice of partner can significantly impact your project’s success. It’s not just about selecting the right material, it’s about finding a team that understands your vision, delivers excellence, and drives innovation every step of the way. At Via Indigos, we’ve built a reputation as a trusted partner for businesses seeking reliability, precision, and long-term value in their manufacturing processes.
Here’s what sets us apart:
1. Material Expertise
Navigating the intense world of materials, especially aluminum alloys, requires deep knowledge and a keen understanding of your project’s needs. Our team doesn’t just provide materials, we guide you in selecting the perfect alloy tailored to your application. Whether you need strength, heat resistance, corrosion resistance, or a balance of properties, we ensure your material choice aligns seamlessly with your product’s requirements and goals.
2. Streamlined Processes
Efficiency and transparency are at the heart of what we do. From the initial design phase to the final production, every step is meticulously planned and executed to minimize lead times and reduce costs. Our collaborative approach ensures that you’re always informed and in control, with clear communication and consistent updates. We work to identify bottlenecks and optimize workflows, ensuring your supply chain operates like a well-oiled machine.
3. Global Reach with Local Insight
With operations in both the USA and India, we combine global scalability with local expertise. This dual presence allows us to offer cost-effective solutions while maintaining the quality and precision demanded by competitive markets. Our cross-border capabilities mean we can cater to a diverse range of industries and adapt to your supply chain needs, whether it’s meeting tight deadlines, managing international logistics, or supporting market-specific requirements.
4. Commitment to Sustainability
In an era where environmental responsibility is non-negotiable, we prioritize sustainable practices throughout our operations. While aluminum is already recognized as a recyclable and eco-friendly material, we go a step further by implementing energy-efficient processes, reducing waste, and promoting circular manufacturing practices. By working with us, you’re not just optimizing your product, you’re contributing to a greener, more sustainable future.
5. Unparalleled Customer Focus
At VIA INDIGOS, every project starts with you. We take the time to understand your unique needs, challenges, and goals, ensuring that our solutions are tailored to deliver real value. Whether you’re developing a groundbreaking product or refining an existing one, our team is committed to being your partner in success. We believe in building long-term relationships through trust, reliability, and results that speak for themselves.
6. Innovation at Every Turn
The manufacturing world is evolving, and staying competitive means embracing new technologies and methodologies. We bring a forward-thinking approach to every project, leveraging advanced tools, data-driven insights, and innovative solutions to help you stay ahead of the curve. Whether it’s introducing cutting-edge materials or optimizing your supply chain with the latest practices, we’re always looking for ways to drive your business forward.
When you work with VIA INDIGOS, you’re not just choosing a supplier, you’re partnering with a team dedicated to elevating your business. From our deep expertise in aluminum alloys to our commitment to efficiency, sustainability, and customer satisfaction, we’re here to ensure your success every step of the way.
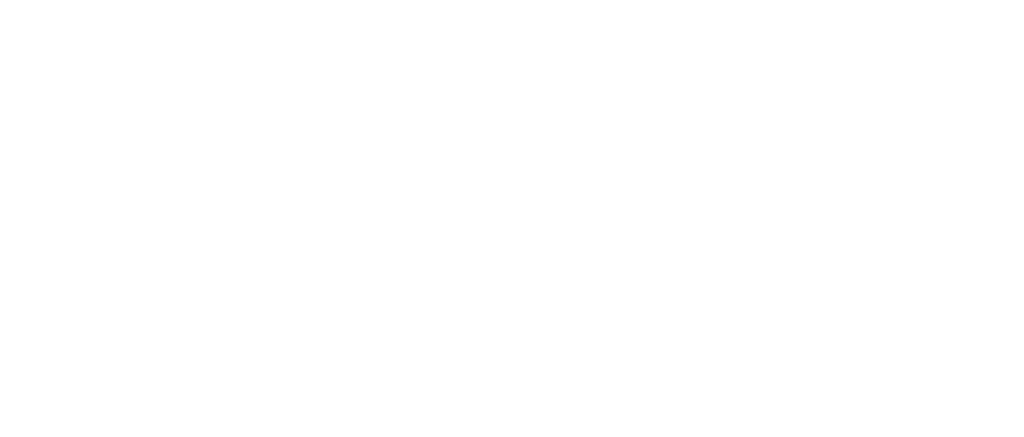
From construction to consumer goods to automotive, we help you unlock aluminum alloys for high-performance applications.
Let’s Collaborate on Your Next Project
At the end of the day, your success is our success. We’re here to help you unlock the full potential of aluminum alloys and achieve your manufacturing goals. Whether you’re looking to improve efficiency, reduce costs, or innovate with new designs, VIA INDIGOS, one of the leading custom aluminum extrusion manufacturers, is your partner in progress.
With aluminum alloys as your foundation and VIA INDIGOS as your trusted partner, the possibilities are endless. Let’s build something amazing!