Top Applications of Drop Hammer Forging in Automotive Manufacturing
- VIA INDIGOS
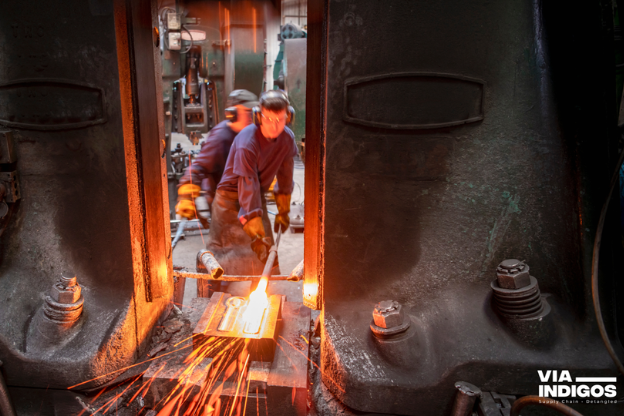
The automotive industry is one of the most demanding sectors when it comes to the durability, strength, and precision of its components. Every part, whether it’s a small nut or a major structural element, plays a critical role in the overall performance and safety of the vehicle. As such, the manufacturing processes used to create these components must be able to meet stringent requirements for both quality and performance.
One of the most reliable and efficient manufacturing methods for producing high-strength components in automotive manufacturing is drop hammer forging. In this long-form post, we will take an in-depth look at what drop hammer forging is, why it’s used in automotive manufacturing, and the specific automotive components that benefit most from this process.
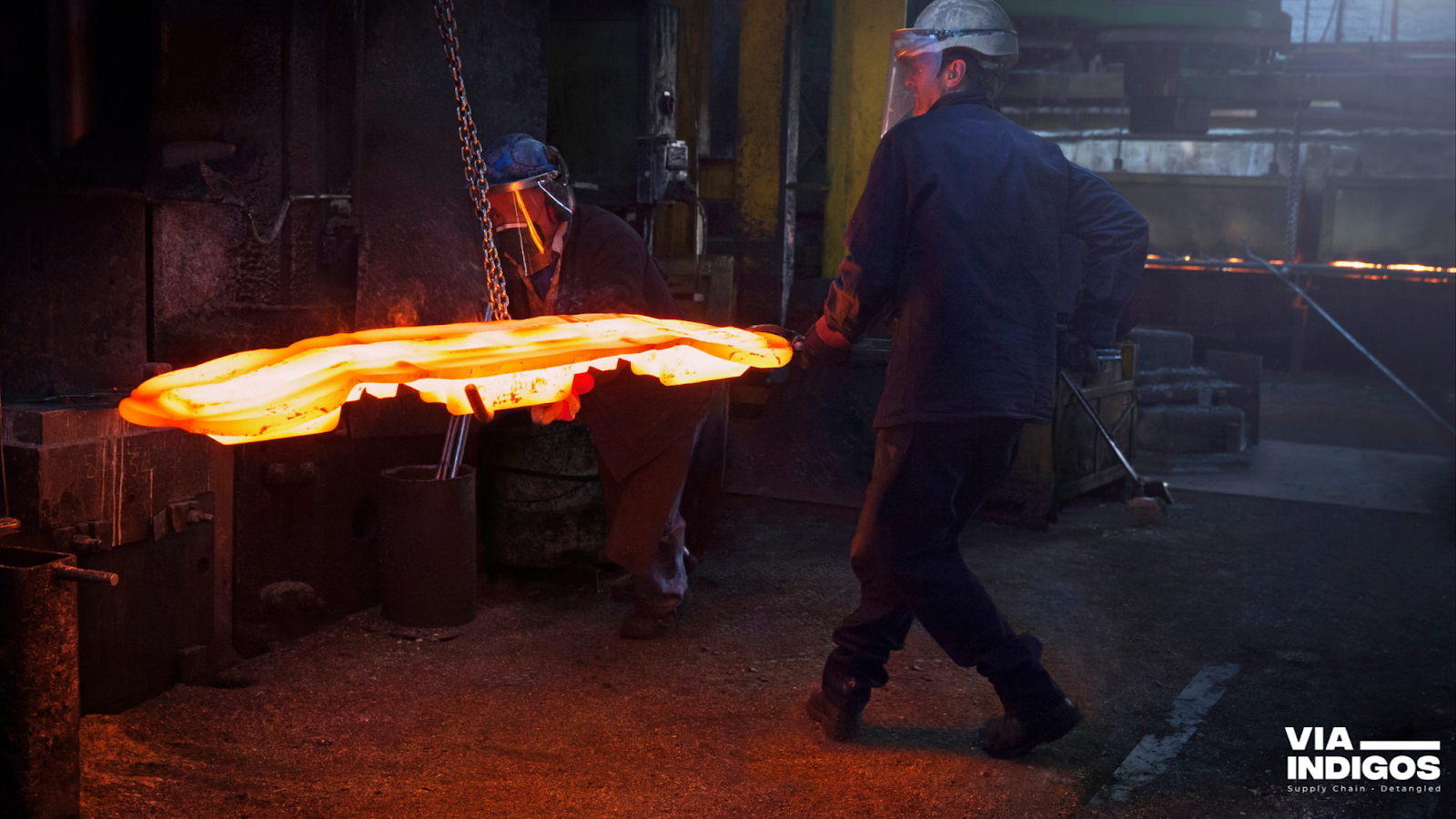
Hot Metal Forging- Intense Heat and Craftsmanship at its best.
What is Drop Hammer Forging?
Drop hammer forging is a metalworking process that uses the force of a rapidly falling hammer to shape heated metal into specific forms. This technique has been a cornerstone in the manufacturing of many high-performance parts for decades due to its ability to enhance the strength, precision, and durability of the parts it creates.
The process involves heating a metal billet (a solid piece of metal that’s typically square or round) to a malleable temperature and then placing it into a die. A hammer, which can weigh several tons, is then dropped onto the billet to shape it into the desired form. The hammer is repeatedly dropped in quick succession to refine the part, and this intense pressure has the effect of aligning the grain structure of the metal, making the final product significantly stronger than it would be with other manufacturing methods.
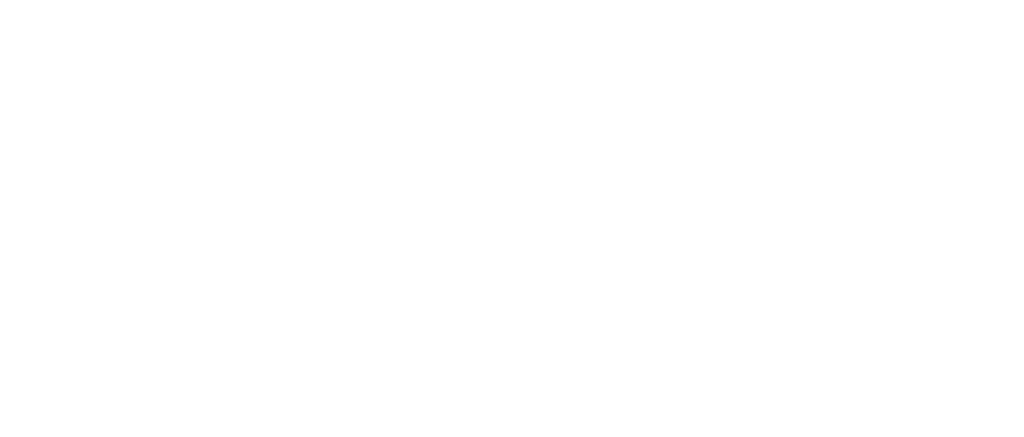
The key benefits of drop hammer forging are
1. Improved Material Strength
The drop hammer forging process significantly enhances the material’s strength through a combination of heat, pressure, and rapid deformation. When a heated metal billet is struck by the hammer, the impact compresses the material, forcing the metal’s grain structure to align in a way that improves its overall mechanical properties. This grain alignment increases the metal’s density, making it stronger and more resistant to deformation.
The forging process also eliminates any air pockets, internal defects, or impurities that might be present in the metal. These impurities, which could lead to weakness or failure in a part, are compressed and eliminated under the high pressure of the hammer strikes. The result is a part with superior tensile strength, able to withstand higher forces without cracking or breaking. This is particularly important in automotive manufacturing, where components like engine parts, suspension components, and drive train elements experience continuous mechanical stress during operation.
Moreover, the increased material density resulting from the forging process ensures that the part has a more uniform structure, which further improves its performance under stress. Parts that undergo drop hammer forging are less likely to experience issues such as cracking, bending, or warping, even under extreme loads and pressures.
2. Greater Durability
Durability is a critical factor for automotive components, as these parts must endure extreme conditions, including high temperatures, high-speed movements, and constant mechanical stress. Drop hammer forging provides parts with superior resistance to fatigue, wear, and cracking, ensuring they perform reliably over time.
The pressure applied during the forging process refines the material at the microscopic level, making it less prone to fatigue. Metal fatigue occurs when materials undergo repetitive stress, eventually leading to cracks. However, the grain structure achieved during drop hammer forging strengthens the material, significantly reducing the likelihood of fatigue-induced failure.
In addition to fatigue resistance, drop hammer-forged parts also exhibit superior wear resistance. Automotive components like gears, axles, and brake parts are constantly exposed to friction, which can lead to wear over time. By compressing the metal and improving its internal structure, drop hammer forging results in parts that are better equipped to resist wear and maintain their functionality for a longer period, even under high-friction conditions.
The final part also benefits from a reduced risk of cracking. Cracks are often the result of stress concentrations or weaknesses within the material. However, the forging process helps eliminate voids and strengthens the grain, making the final product more resistant to cracking under pressure. This is essential in automotive components like crankshafts and connecting rods, where the parts are exposed to extreme loads and stresses during engine operation.
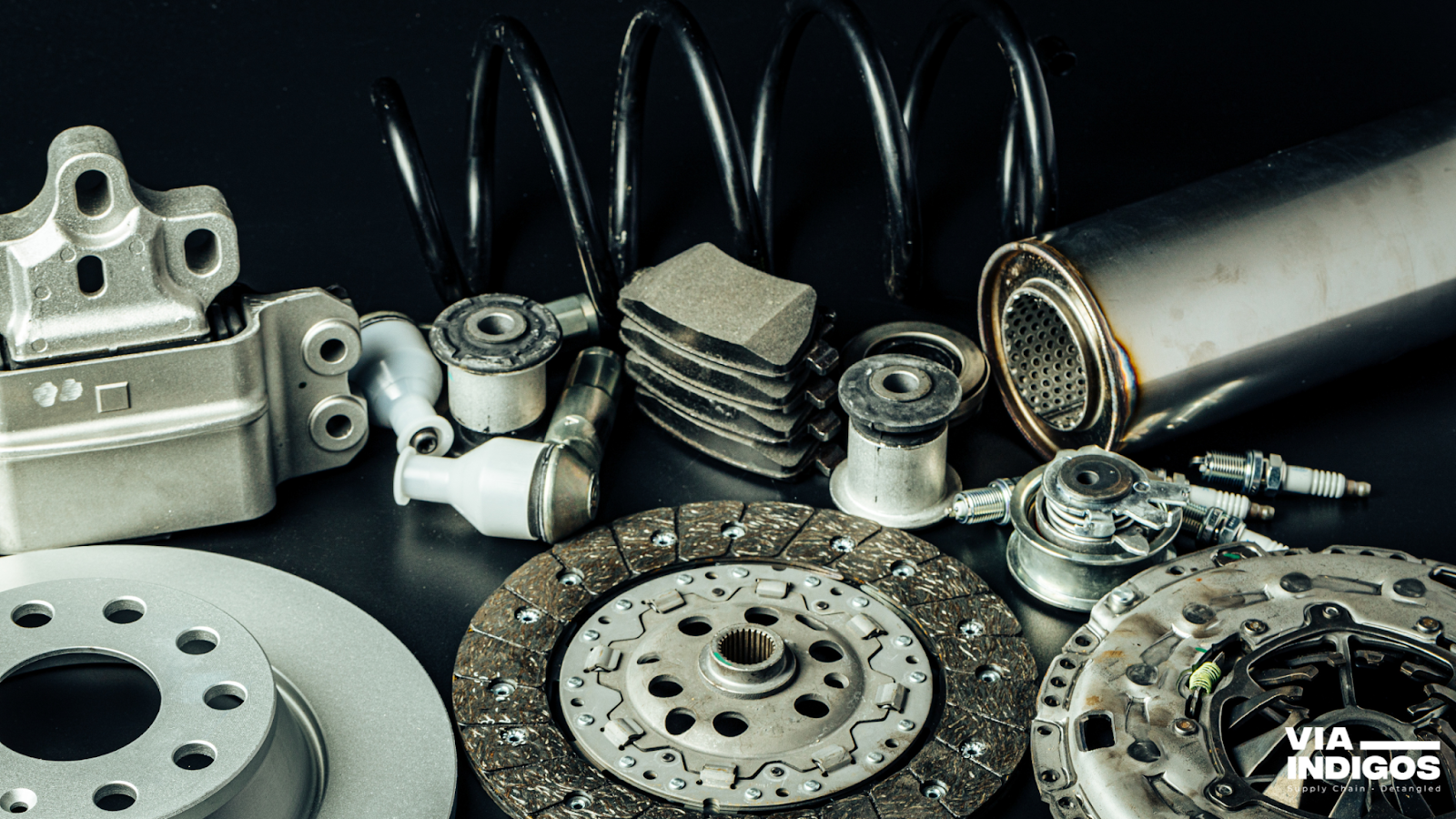
Automotive Parts highlighting precision engineering.
3. Precision
One of the key advantages of drop hammer forging is its ability to produce parts with high precision. The dies used in the forging process are designed with great attention to detail and are capable of producing highly accurate parts with exact tolerances. This level of precision is crucial in automotive manufacturing, where even small deviations from the required specifications can affect the performance, safety, and fit of the parts.
The dies used in drop hammer forging can be designed with intricate features and complex shapes, allowing for the production of parts that meet the exact specifications required for specific automotive applications. The pressure from the hammer, along with the precise design of the die, ensures that every part is shaped to the desired dimensions, without the need for additional machining or finishing. This reduces the likelihood of errors and ensures that each component fits seamlessly into the vehicle’s overall design.
Additionally, the consistency of the process ensures that each part produced in a batch will meet the same standards of precision. This is particularly important in automotive applications where consistency and repeatability are essential. For example, in engine manufacturing, parts such as pistons, crankshafts, and connecting rods must all have extremely tight tolerances to ensure that the engine runs smoothly and efficiently.
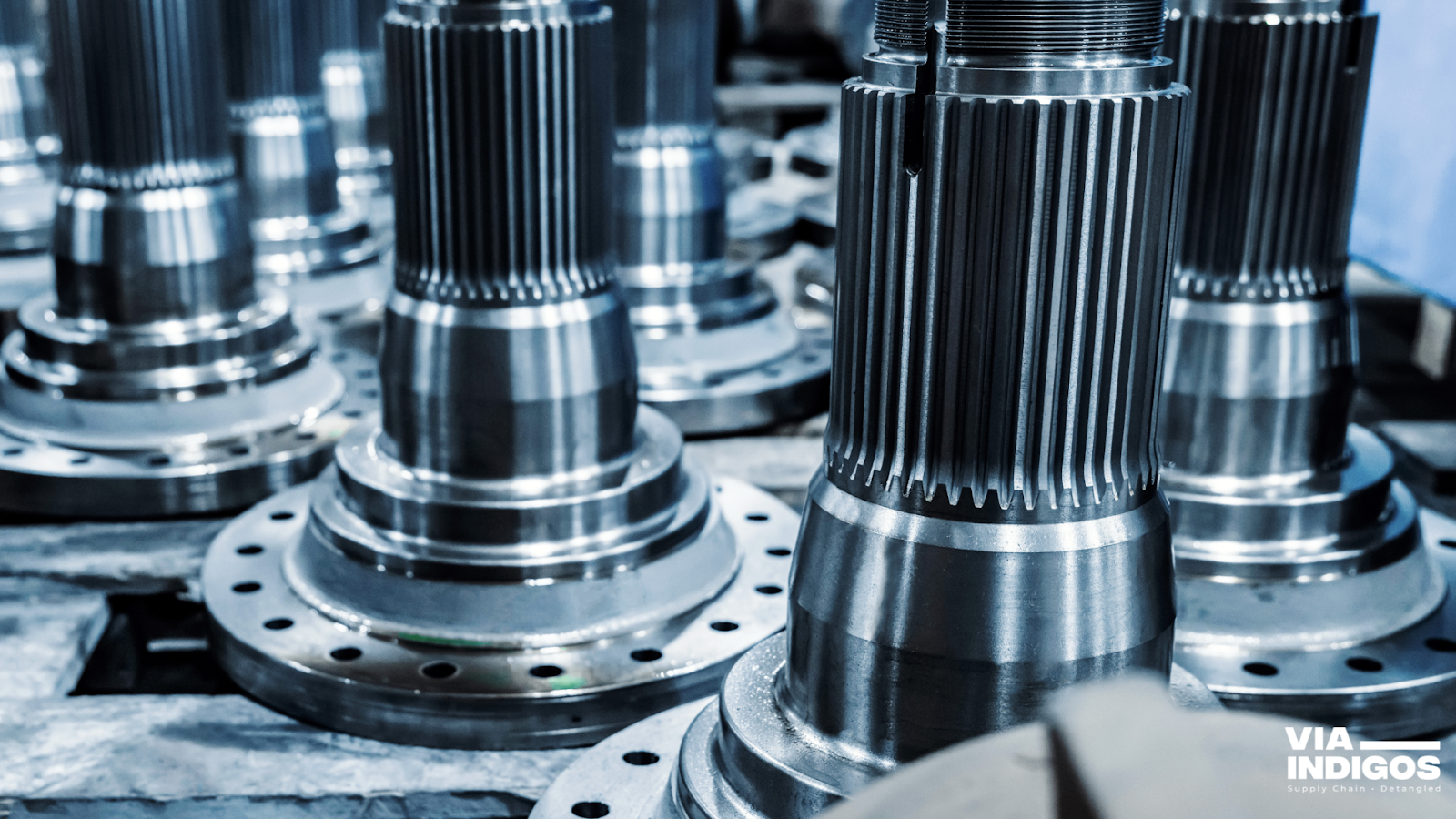
Precisioned forged-machined automotive parts.
4. Cost-Effectiveness
While drop hammer forging is considered a high-energy process due to the intense pressure and repeated hammer blows used to shape the metal, it is highly cost-effective in the long term for several reasons.
First, drop hammer forging minimizes material waste compared to other manufacturing methods like casting or machining. In casting, excess material may need to be trimmed away, leading to wasted resources, and in machining, material is often removed through cutting, leading to further material loss. In contrast, drop hammer forging uses a billet of metal and shapes it into the desired form without removing large amounts of material. The precise shaping reduces the need for additional finishing or machining steps, saving time and resources.
Second, drop hammer forging produces parts with exceptional strength and durability, which means the parts have a longer lifespan. For automotive manufacturers, this translates to fewer replacements and repairs, reducing overall maintenance costs. Stronger, more durable components also lead to better vehicle performance and fewer warranty claims, saving money on repairs and increasing customer satisfaction.
Additionally, the efficiency of drop hammer forging is another cost-saving factor. Although the process requires high energy to drive the hammer strikes, it can produce large quantities of parts quickly and with minimal need for rework. This makes it suitable for mass production, especially for components that are needed in large volumes, such as axles, gears, and crankshafts. The ability to mass-produce high-quality parts at a relatively low cost contributes to the overall cost-effectiveness of the method, especially in the automotive industry, where large-scale production is essential.
Finally, drop hammer forging often results in parts that require fewer additional processes. Many forged parts are finished directly after forging without needing extensive machining or further operations. This reduces the time and labor costs involved in manufacturing, making it more cost-effective compared to methods that require multiple stages of production or finishing.
In automotive manufacturing, this process is used to produce a wide range of components that require high mechanical properties, such as strength, toughness, and wear resistance. By compressing and shaping the metal under intense pressure, drop hammer forging creates parts that are stronger, more resistant to wear and fatigue, and able to meet the exacting standards required in the automotive industry. This process is cost-effective because it reduces material waste, minimizes the need for additional machining, and produces durable parts that require less maintenance over time. With these advantages, drop hammer forging remains an essential technique for creating high-performance, reliable automotive components.
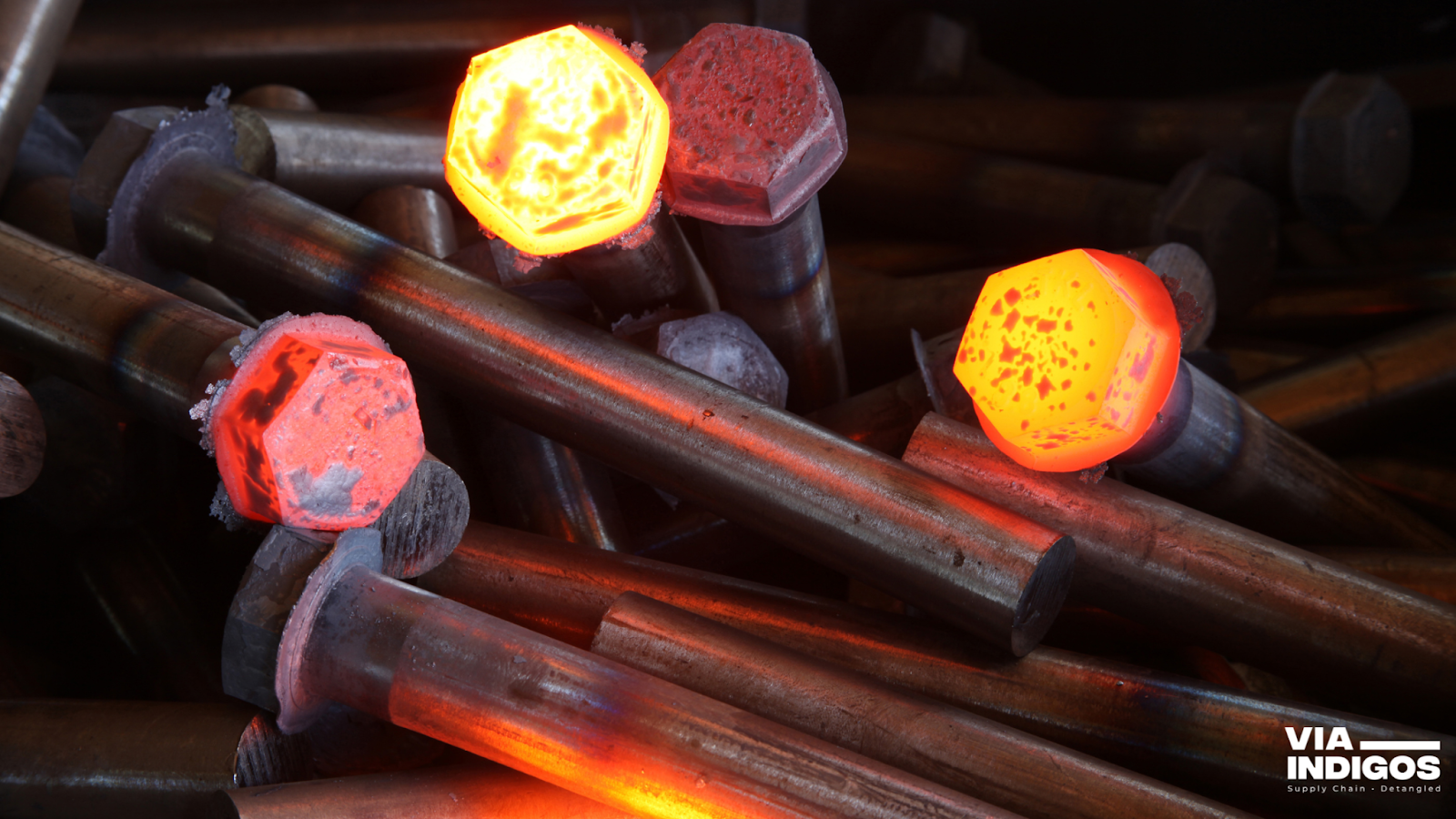
Hot forged fasteners under the forging process.
Top Applications of Drop Hammer Forging in Automotive Manufacturing
1. Crankshafts
• Why Crankshafts are Critical: The crankshaft is one of the most vital components of an internal combustion engine. It converts the linear motion of the pistons into rotational motion, which then drives the vehicle’s wheels. Crankshafts must endure extremely high levels of stress, torque, and vibration, making their strength and durability essential for the engine’s performance.
• Why Drop Hammer Forging Works: Crankshafts require exceptional strength, toughness, and fatigue resistance. Drop hammer forging helps create a fine grain structure in the metal, enhancing its strength and durability. The forging process ensures that the metal used in crankshafts has the optimal characteristics to handle the stresses of high-speed operation.
• How the Process Works: The crankshaft billet is first heated and then placed into a die. A series of hammer blows shapes the billet into the rough form of the crankshaft. Additional hammer strikes are used to refine the shape and enhance the metal’s grain structure, resulting in a part that can handle the extreme forces involved in engine operation without cracking or failing.

An engine crankshaft, showcasing precision engineering and durability.
2. Connecting Rods
• Why Connecting Rods are Critical: Connecting rods link the pistons to the crankshaft and must be able to withstand the forces generated by combustion. These components are under constant stress during engine operation and must remain strong, lightweight, and resistant to fatigue.
• Why Drop Hammer Forging Works: The drop hammer forging process enhances the grain structure of the metal, creating a stronger and more durable connecting rod. The ability to produce complex shapes ensures that connecting rods are both lightweight and capable of withstanding the immense forces they experience in the engine.
• How the Process Works: The heated billet is placed in a die, where it is shaped by the drop hammer. The repeated impact ensures the material is compacted, increasing its strength and fatigue resistance. By using high-quality alloys and optimizing the forging process, manufacturers can produce connecting rods that meet the high-performance demands of modern engines.
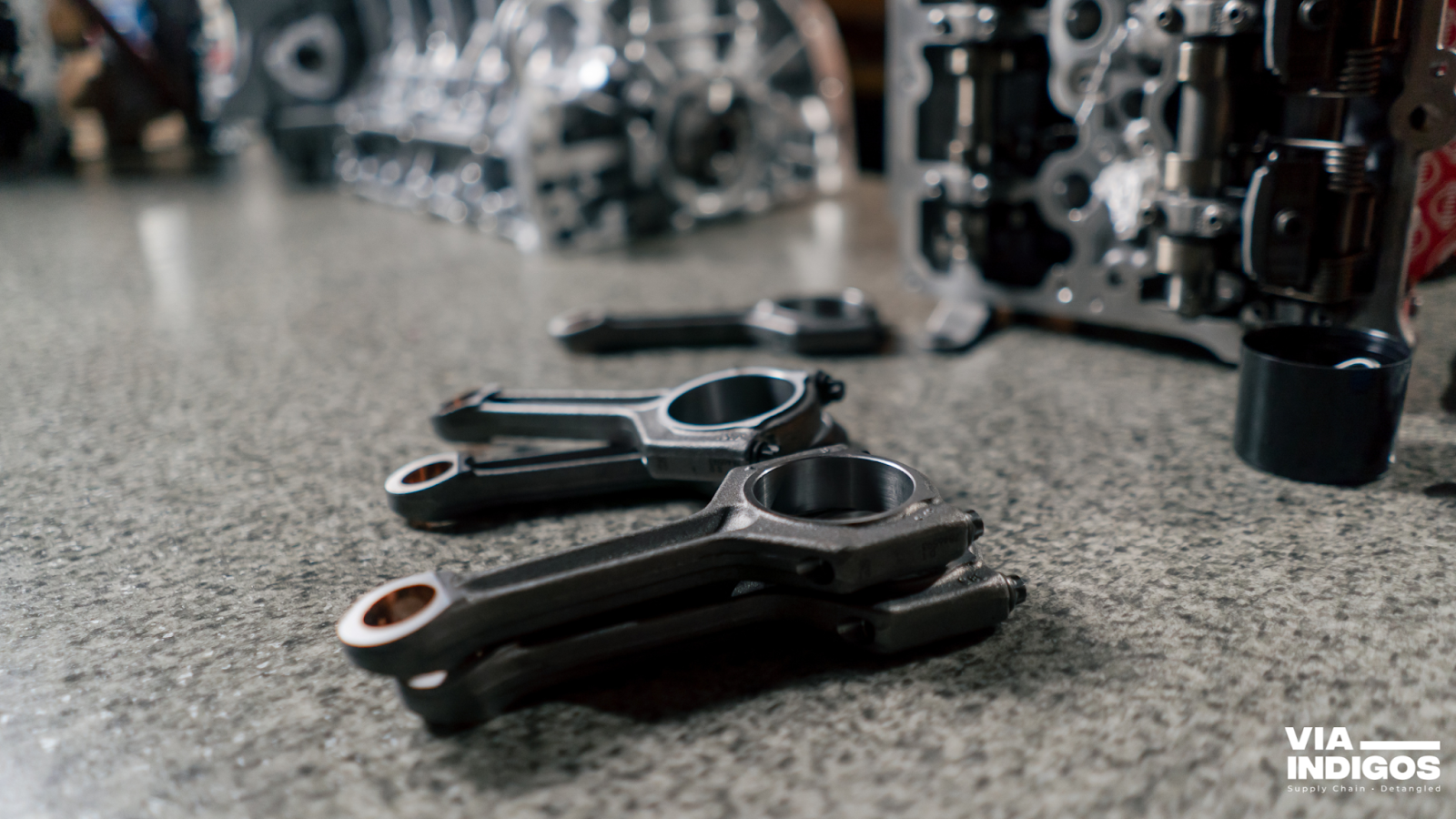
A Connecting Rod all set to get installed.
3. Wheel Hubs
• Why Wheel Hubs are Critical: The wheel hub is a key part of the vehicle’s suspension system. It serves as the central connection point for the wheel and axle and bears much of the weight of the vehicle. The hub must be strong enough to withstand the forces from road impacts, turning, and braking.
• Why Drop Hammer Forging Works: Drop hammer forging is ideal for producing wheel hubs due to its ability to create high-strength, durable components. The forging process enhances the toughness and resistance to wear, ensuring that the wheel hub can endure the high loads and stresses that come with regular driving.
• How the Process Works: Billets for wheel hubs are heated to the appropriate temperature and placed into a die. The drop hammer repeatedly strikes the billet to shape it, compacting the metal and improving its mechanical properties. The result is a robust wheel hub that is less likely to fail under the demands of daily driving and harsh road conditions.
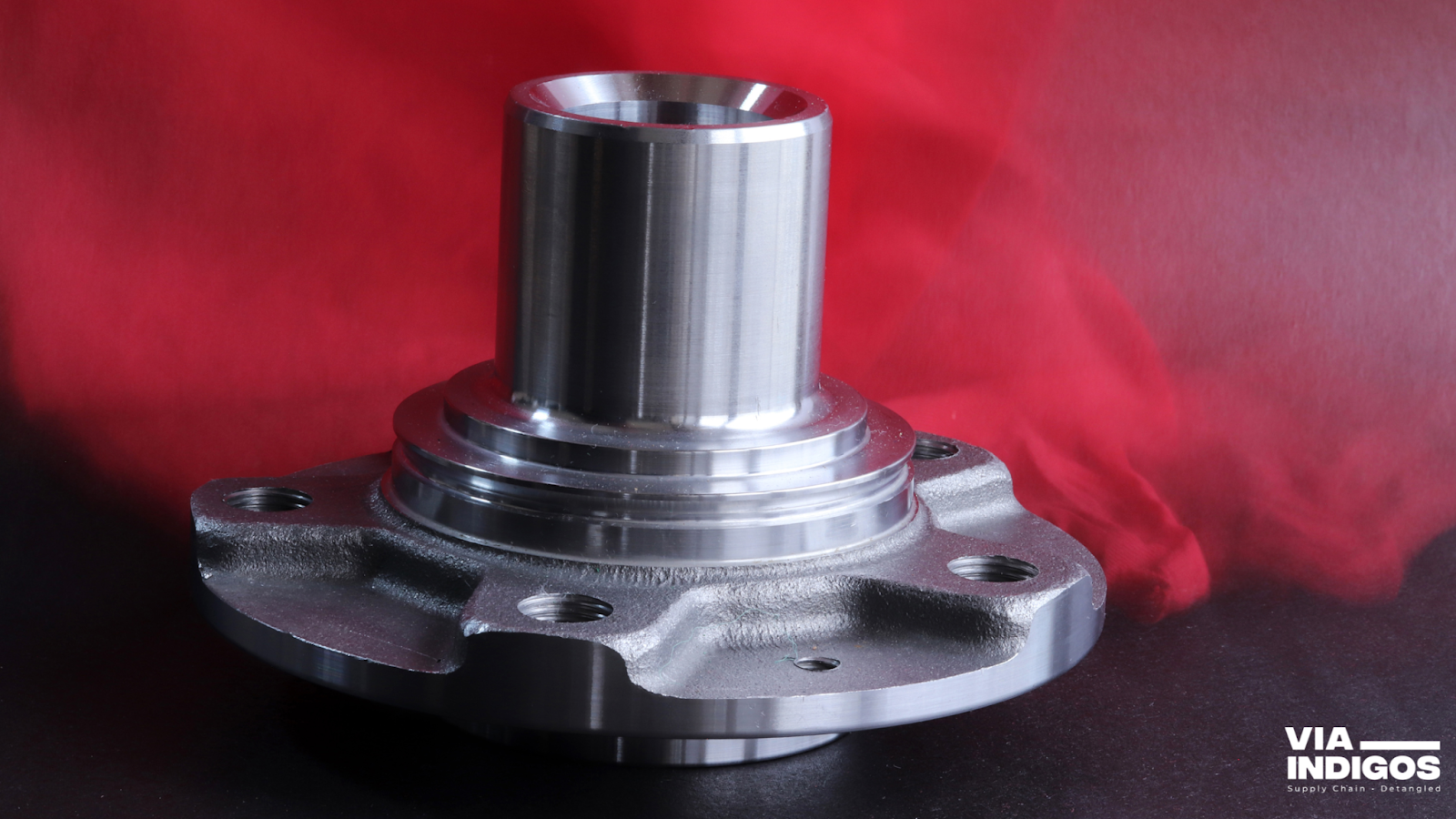
Forged Wheel Hubs machined to precision.
4. Gear Components
• Why Gear Components are Critical: Gears are integral parts of a vehicle’s transmission, helping to transmit power from the engine to the wheels. They must be precisely manufactured to ensure smooth operation and durability. Gears are subjected to constant friction and pressure, making their strength and wear resistance essential.
• Why Drop Hammer Forging Works: Drop hammer forging provides a highly effective way to create gears that are both precise and strong. The process improves the density of the metal, enhancing the gear’s resistance to wear and fatigue. It also allows for the production of complex, finely detailed gear teeth that are essential for efficient transmission operation.
• How the Process Works: Gear blanks are heated to the correct temperature, and the drop hammer is used to shape the metal into the required gear form. The repeated impact ensures that the teeth are properly formed, while also aligning the grain structure of the material to improve the overall strength and wear resistance of the gear.
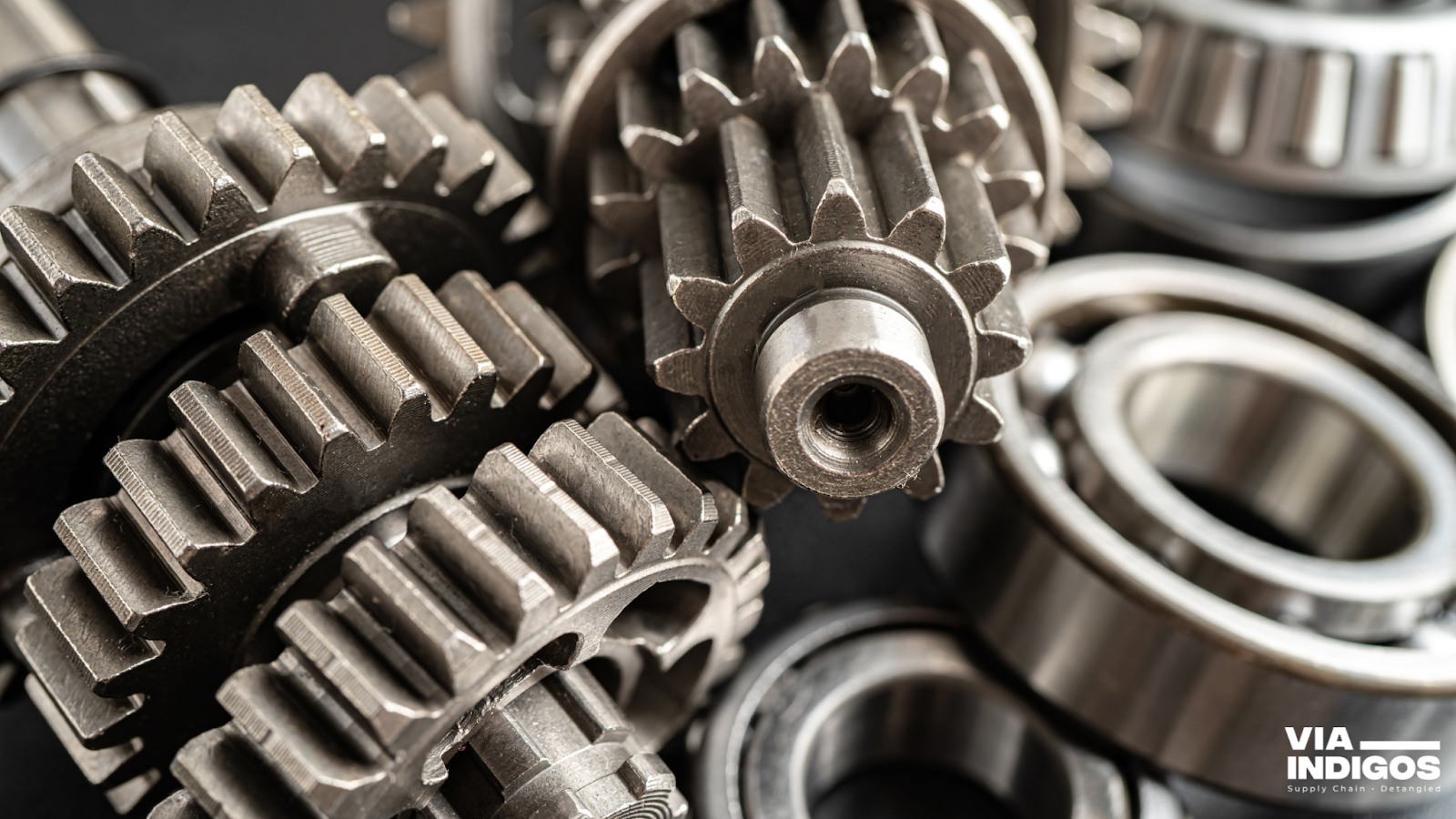
Brass gears and cogs interlock, showcasing precise clockwork engineering.
5. Suspension Components
• Why Suspension Components are Critical: Suspension components, such as control arms, struts, and shock mounts, are essential for absorbing shocks and providing a smooth ride. These parts must be strong enough to withstand dynamic loads, impacts, and the wear and tear of rough roads and varied driving conditions.
• Why Drop Hammer Forging Works: Suspension components must be able to handle significant forces without deforming or breaking. Drop hammer forging enhances the mechanical properties of the metal, making it tougher and more resistant to stress. The ability to produce parts with complex shapes and detailed geometries further improves performance.
• How the Process Works: Steel billets are heated and placed into a die, where they are shaped by the repeated impact of the drop hammer. The forging process ensures that the material is dense and free from defects, resulting in high-strength suspension components that will perform reliably over time.
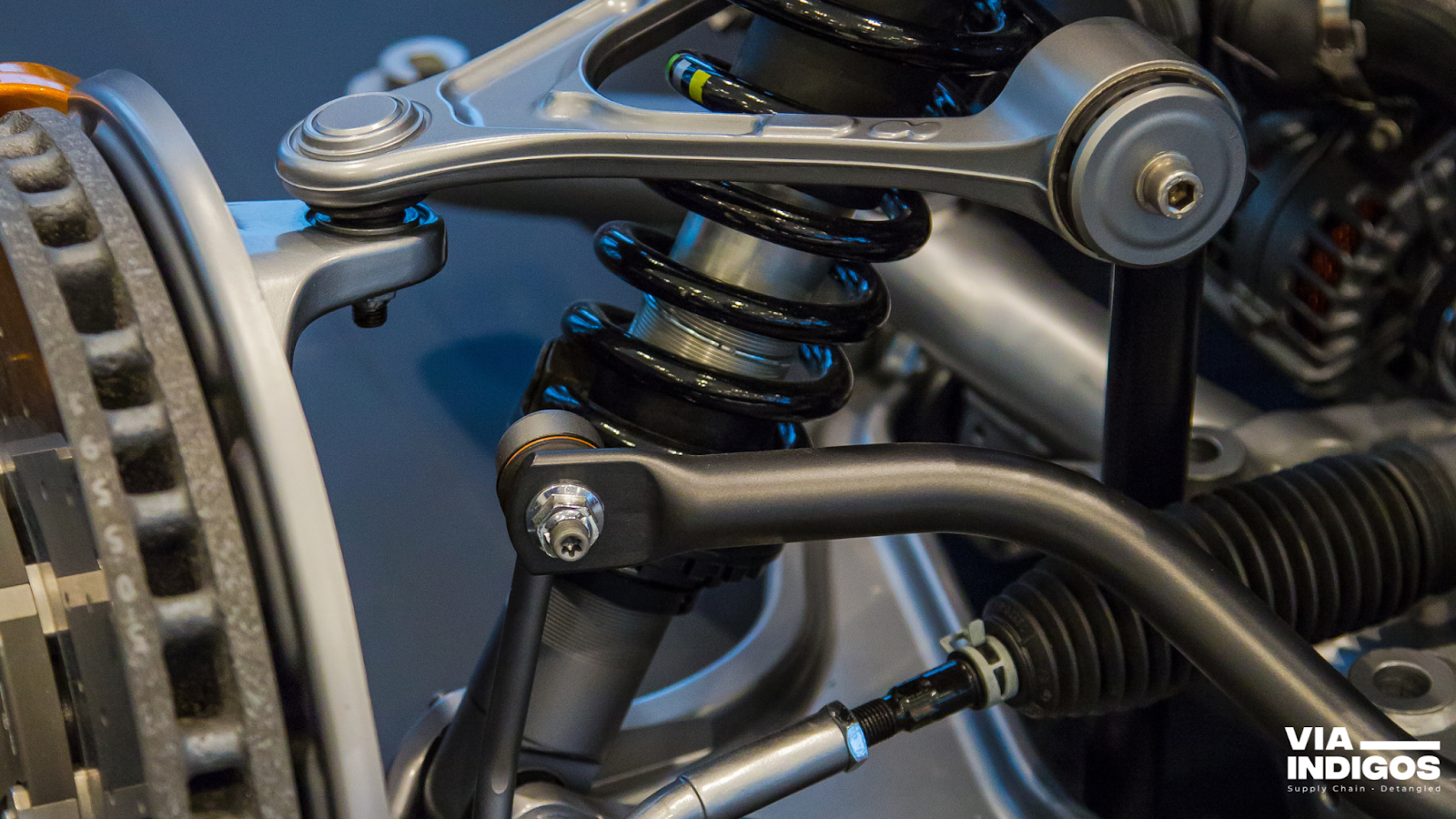
Vehicle suspension and axle system
6. Axles
• Why Axles are Critical: Axles are essential for connecting the wheels to the drivetrain, and they bear the weight of the vehicle while transmitting torque to the wheels. They are subjected to heavy loads and rotational forces during operation.
• Why Drop Hammer Forging Works: Axles require exceptional strength and fatigue resistance. Drop hammer forging increases the density and strength of the metal, ensuring that the axle can handle the stress from acceleration, braking, and turning. The process also creates a more uniform material structure, minimizing the risk of cracks or failures.
• How the Process Works: After the axle billet is heated, it is placed into a die where it is shaped by the repeated force of the drop hammer. The forging process improves the material properties, resulting in a strong, durable axle that can support the vehicle’s weight and performance requirements.
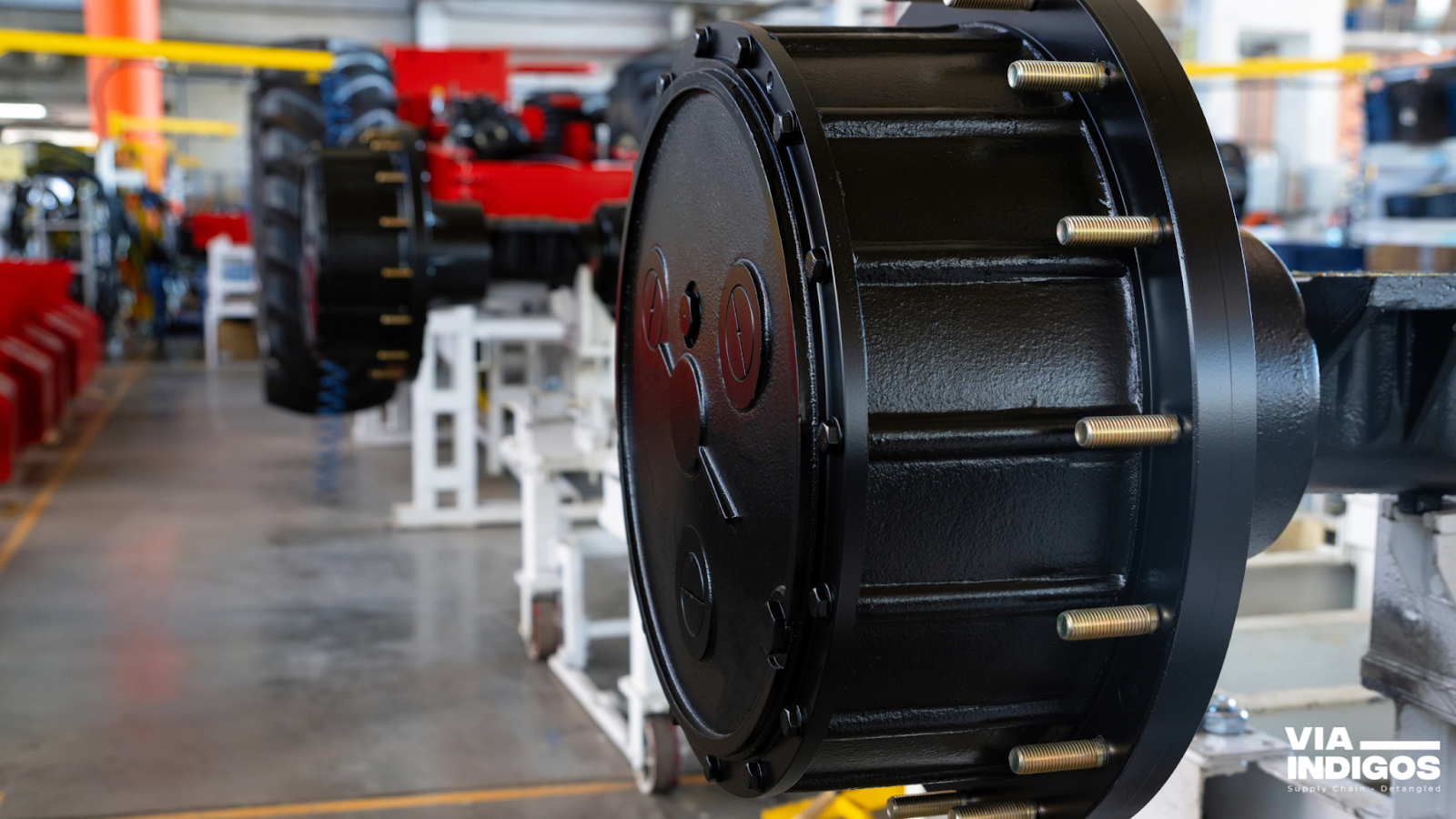
A disassembled tractor axle, showcasing robust mechanical precision.
7. Steering Knuckles
• Why Steering Knuckles are Critical: Steering knuckles are integral parts of a vehicle’s steering system, allowing the wheels to pivot in response to steering inputs. The knuckles must be able to withstand the dynamic forces involved in steering and handling.
• Why Drop Hammer Forging Works: Drop hammer forging produces steering knuckles that are strong and precisely shaped, allowing for smooth, reliable steering performance. The process ensures that the knuckle’s material has a fine grain structure, which enhances its strength and resistance to wear.
• How the Process Works: The billet for the steering knuckle is heated and placed into the die. The repeated hammer strikes shape the knuckle and compress the material, resulting in a precise, durable part that can endure the stresses from turning and road impacts.
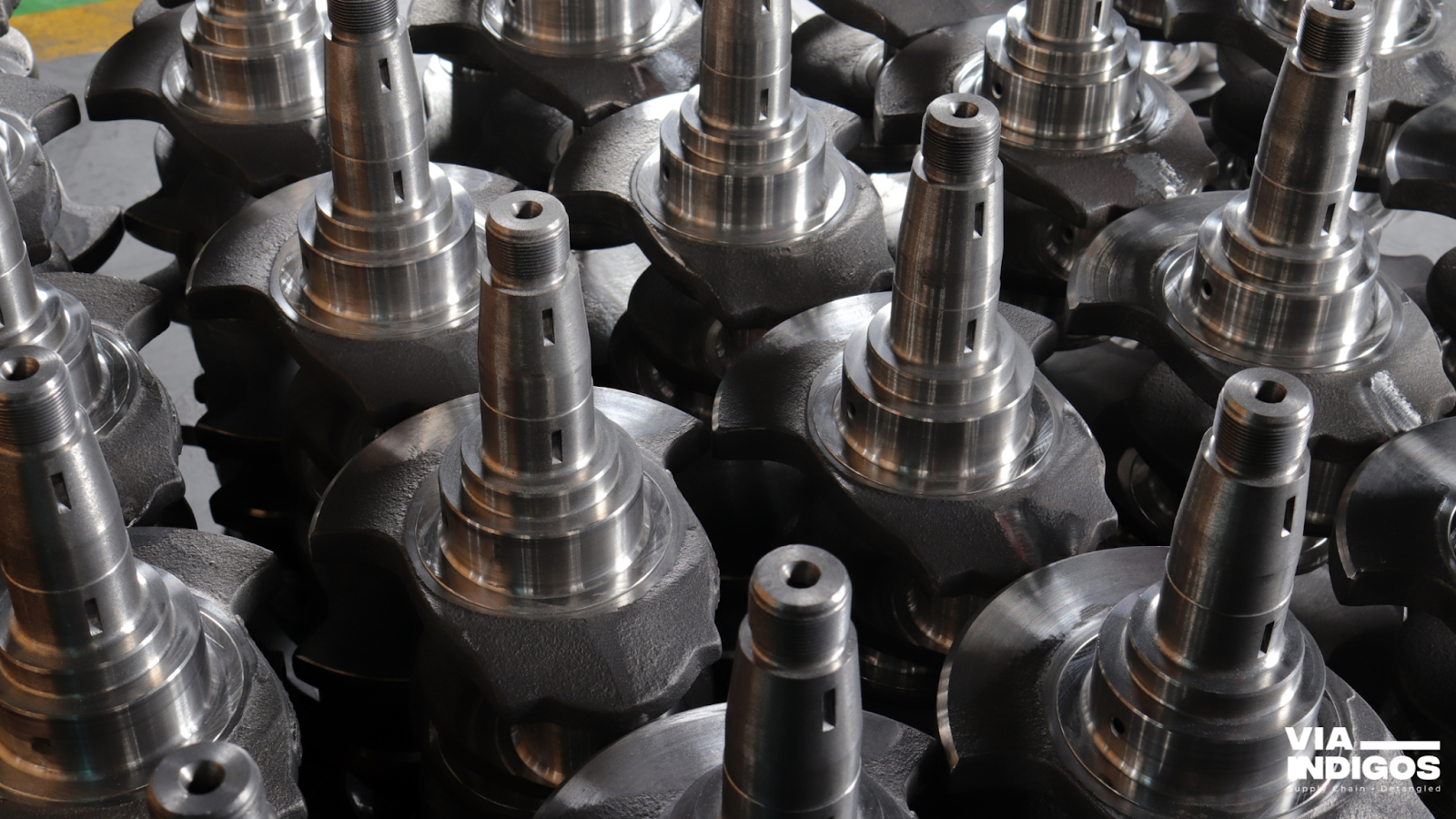
Steering Knuckles forged to precision
Why Drop Hammer Forging is Ideal for Automotive Manufacturing
1. Strength and Durability
Drop hammer forging produces parts that are significantly stronger than cast or machined components due to the grain structure and material densification that occurs during the process. Automotive components that are forged using this method can withstand high mechanical stresses, temperature variations, and exposure to harsh environments, making them ideal for critical parts such as crankshafts, axles, and connecting rods.
2. Precision and Customization
The drop hammer forging process is highly precise, producing parts with tight tolerances and complex shapes that meet the exact specifications required in automotive manufacturing. This allows for the production of highly detailed components, such as gears and suspension parts, which need to meet specific performance standards for safety and efficiency.
3. Material Efficiency
Since drop hammer forging shapes components from a billet rather than cutting or machining them from larger blocks, it results in less material waste. This is particularly important in the automotive industry, where cost efficiency and sustainability are becoming increasingly important.
4. Enhanced Performance
The forging process improves the mechanical properties of the material, enhancing fatigue resistance, wear resistance, and impact strength. This leads to better performance and a longer service life for automotive components, which is crucial for ensuring vehicle reliability and safety.
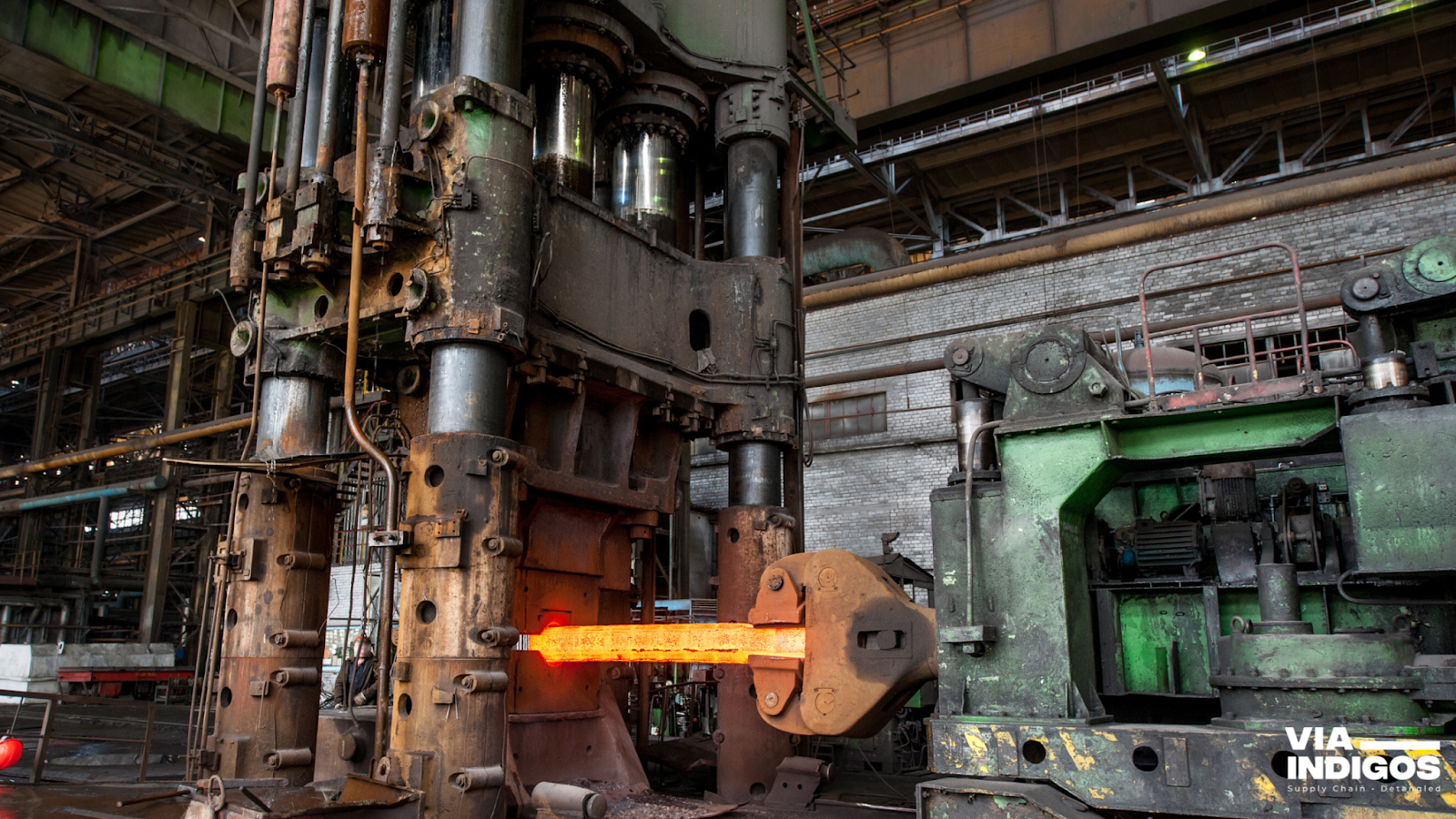
Forging Press Shop, forging under high heat and pressure.
Conclusion
Drop hammer forging is an indispensable manufacturing process in the automotive industry, playing a critical role in the production of high-performance, durable components. From crankshafts to steering knuckles, this method ensures that the parts used in vehicles can withstand the demanding conditions of modern driving while maintaining strength, precision, and reliability. As automotive forging parts manufacturers and suppliers continue to push the boundaries of performance and safety, drop hammer forging will remain a vital technique in producing the high-quality components that consumers and manufacturers alike demand. For businesses looking to ensure the longevity, efficiency, and safety of their automotive products, drop hammer forging is an investment in both performance and quality.
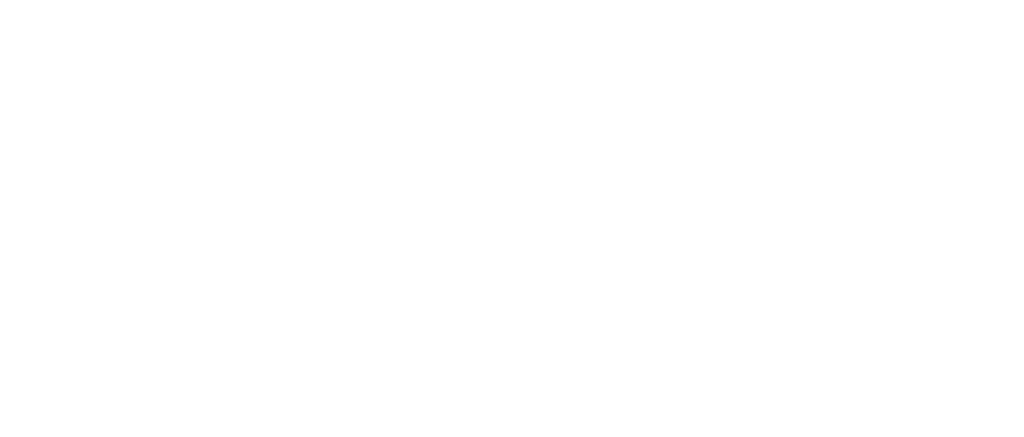
Who We Are
At VIA INDIGOS, we specialize in delivering precision-engineered components through advanced manufacturing techniques, including drop hammer forging. As a trusted partner in global supply chain optimization, we ensure your components meet the highest standards of strength, durability, and precision.
What We Offer:
• End-to-End Manufacturing Solutions tailored for 12+ industries, from initial concept to final door delivery.
• Compliance with Global Standards: All components are certified to meet stringent international standards for safety, reliability, and performance.
• China +1 Strategy: With a strong presence in India and deep manufacturing partnerships, we help businesses diversify their sourcing, cut tariffs, and reduce reliance on single-region supply chains.
• Cost-Effective Forging Techniques: Our network expertise in efficient production methods minimizes waste and reduces costs.
• Precision Forging for Critical Components: Whether it’s crankshafts, axles, or gears, our process ensures every part is built to exacting specifications.
• Reliable Supplier Partnerships: We streamline supply chains by combining global scalability with local expertise, delivering high-quality components with reduced lead times and low tariffs.