Making Precision Plastic Components with Custom Blow Molding
- VIA INDIGOS
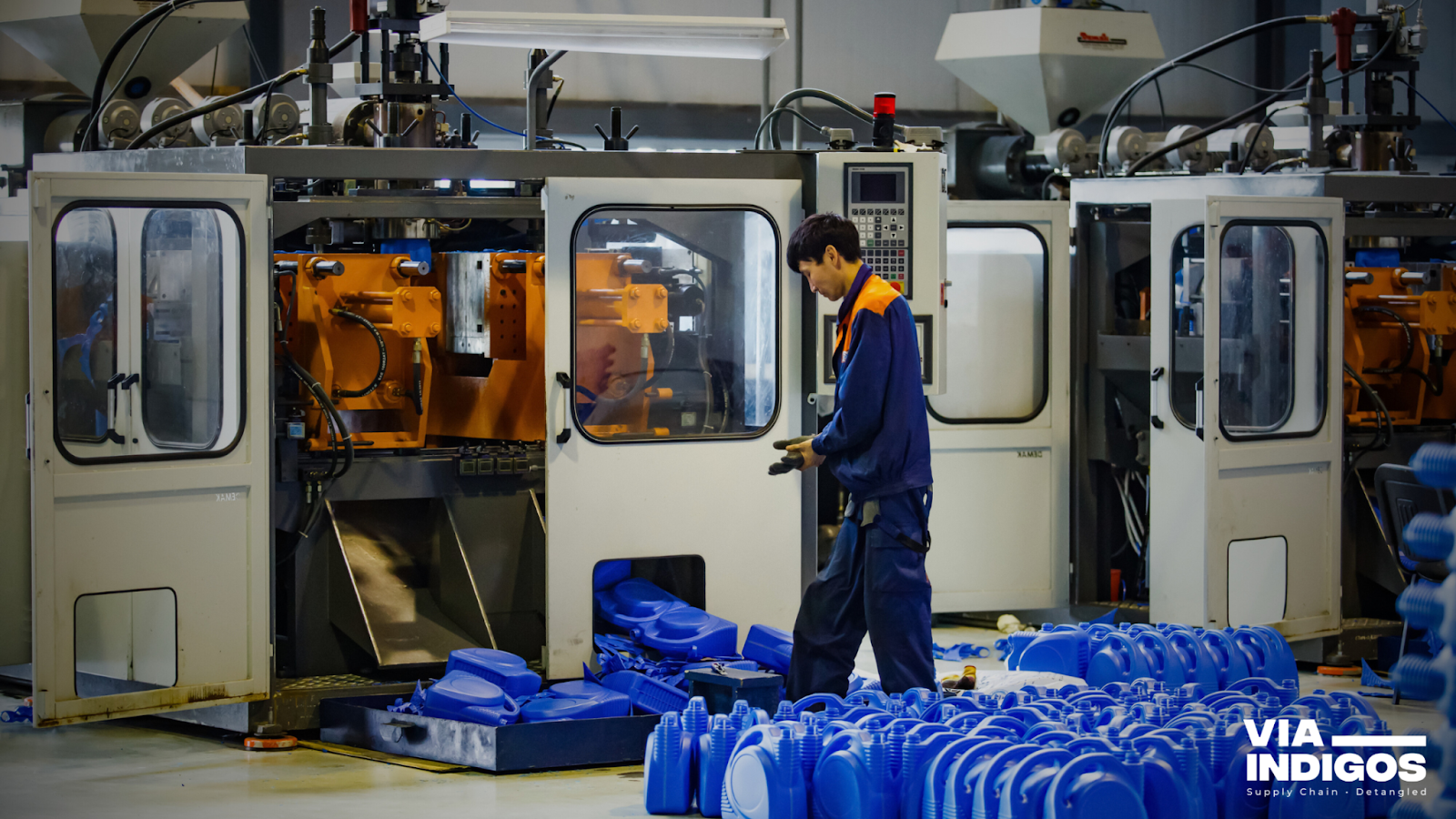
When it comes to creating high-quality, precision plastic components, custom blow molding is a game-changer. This versatile manufacturing process enables the production of complex shapes with consistent quality, making it indispensable for industries ranging from automotive to medical devices. But what exactly is custom blow molding, and how does it deliver the precision and customization businesses demand? Let’s break it down.
What is Custom Blow Molding?
Custom blow molding is a manufacturing process used to produce hollow plastic parts. It involves inflating heated plastic into a mold cavity using air pressure. The process can be highly tailored to create components with specific dimensions, shapes, and material properties.
There are three primary types of blow molding:
• Extrusion Blow Molding (EBM): Used for making items like bottles and large containers. Plastic is extruded into a parison, which is then inflated into the mold.
• Injection Blow Molding (IBM): Ideal for precision parts, where the parison is injection-molded before being blown into the final shape.
• Stretch Blow Molding: Commonly used for creating lightweight, strong bottles (e.g., PET beverage bottles).
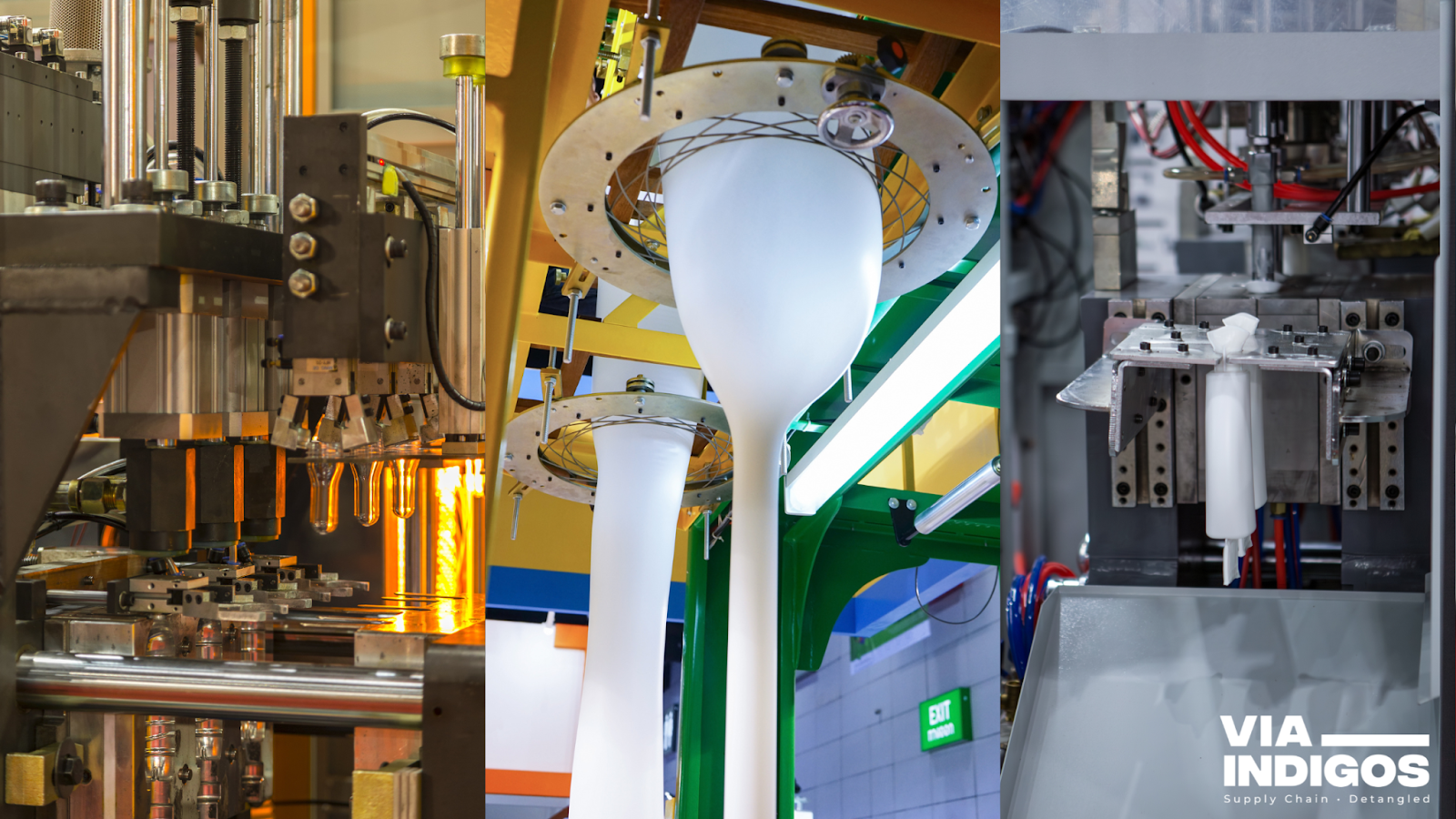
Extrusion Blow Molding: Blow Molded Containers Built for Durability and Efficiency. Perfect for industrial storage, logistics, and more.
Custom blow molding takes these processes a step further by tailoring mold designs, material formulations, and production parameters to meet specific application requirements.
Why Choose Custom Blow Molding for Precision Components?
The precision and flexibility of custom blow molding make it a great choice for manufacturing components that require exacting standards. Here’s why it stands out:
1. Versatility in Design
Custom blow molding allows for the creation of complex geometries that would be difficult or impossible to achieve with other methods. From intricate internal contours to seamless hollow designs, this process enables manufacturers to meet unique design specifications.
2. Material Optimization
With custom blow molding, manufacturers can choose from a wide range of thermoplastics, including:
- • Polyethylene (PE): Durable and cost-effective for general applications.
- • Polypropylene (PP): Known for its chemical resistance and flexibility.
- • Polycarbonate (PC): Ideal for components that require transparency and impact resistance.
Materials can be customized further with additives to enhance properties such as UV resistance, flame retardancy, or strength.
3. Cost Efficiency
For high-volume production, custom blow molding is incredibly cost-effective. Once the mold is created, the per-unit cost decreases significantly, making it an attractive option for industries that require large production runs.
4. Consistency and Precision
Modern blow molding machines equipped with advanced controls ensure tight tolerances and consistent quality across batches. This precision is critical for industries like automotive, where components must fit together seamlessly.
5. Energy Efficiency
Modern blow molding machines consume 30%-40% less energy due to advancements in electric and hybrid technologies, supporting energy efficiency trends.
Applications of Custom Blow Molding
Custom blow molding is used in a variety of industries, each with unique requirements. Here are some examples of precision components created using this technique: Custom blow molding is used in a variety of industries, each with unique requirements:
1. Automotive
Precision components include:
• Air ducts: Used in climate control systems, these require tight dimensional tolerances for proper airflow.
• Fluid reservoirs: Such as windshield washer fluid tanks, designed to fit specific vehicle models.
• Fuel tanks: Lightweight yet robust to meet safety and efficiency standards. Precision components like air ducts, fluid reservoirs, and fuel tanks are often produced using custom blow molding. These parts need to meet stringent safety and performance standards.
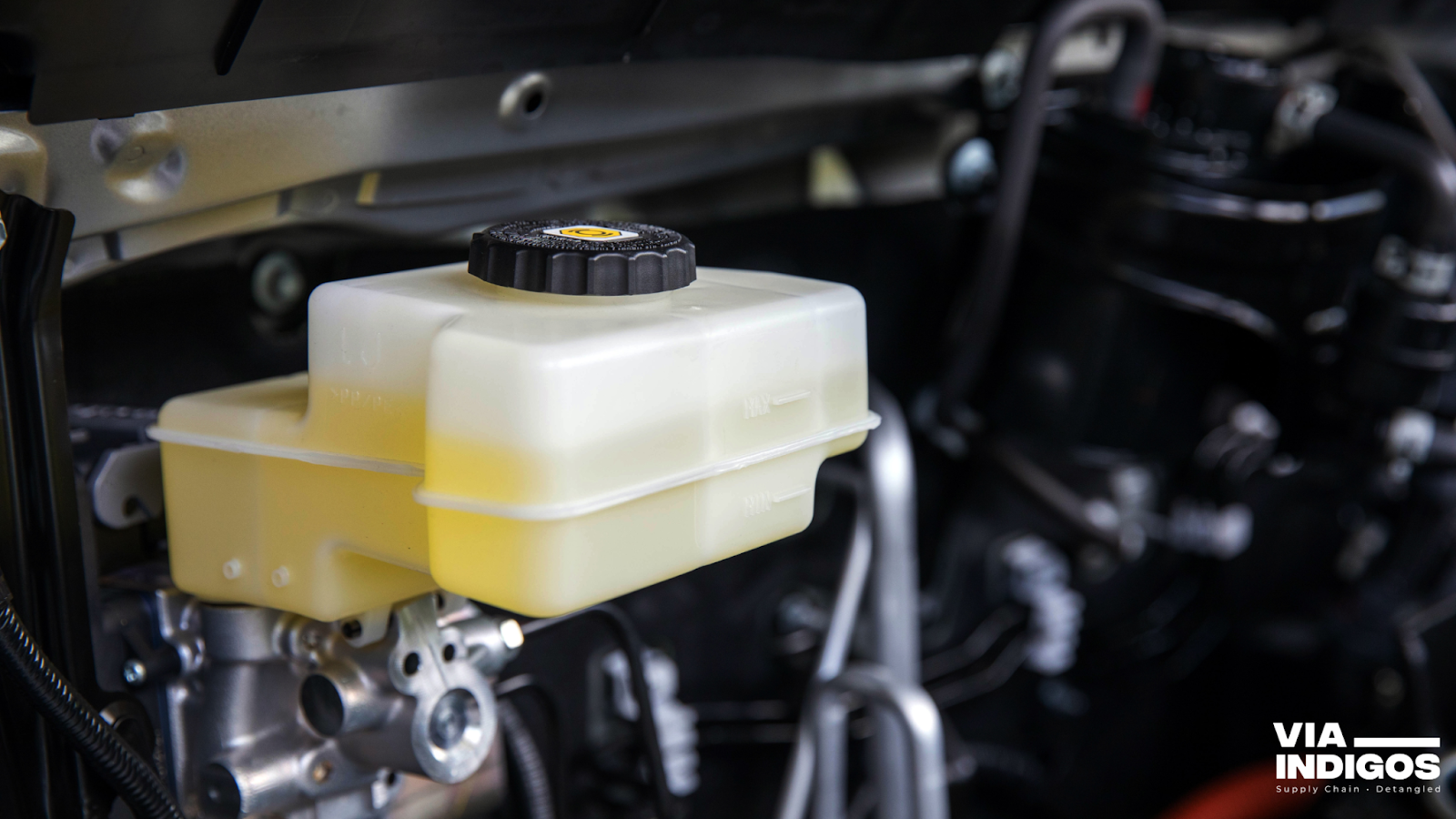
Custom Blow Molding for Precision Automotive Components: From fluid reservoirs to lightweight fuel tanks.
2. Medical Devices
Precision components include:
• IV bags: Designed for durability and sterility, with custom shapes for specific applications.
• Catheter tubing: Requires exact internal diameters for safe and effective use.
• Oxygen masks: Lightweight and designed to fit comfortably while delivering precise airflow. In the medical field, blow molding is used to create sterile, lightweight components such as IV bags, containers, and tubing. The ability to customize shapes and materials is invaluable in this sector.
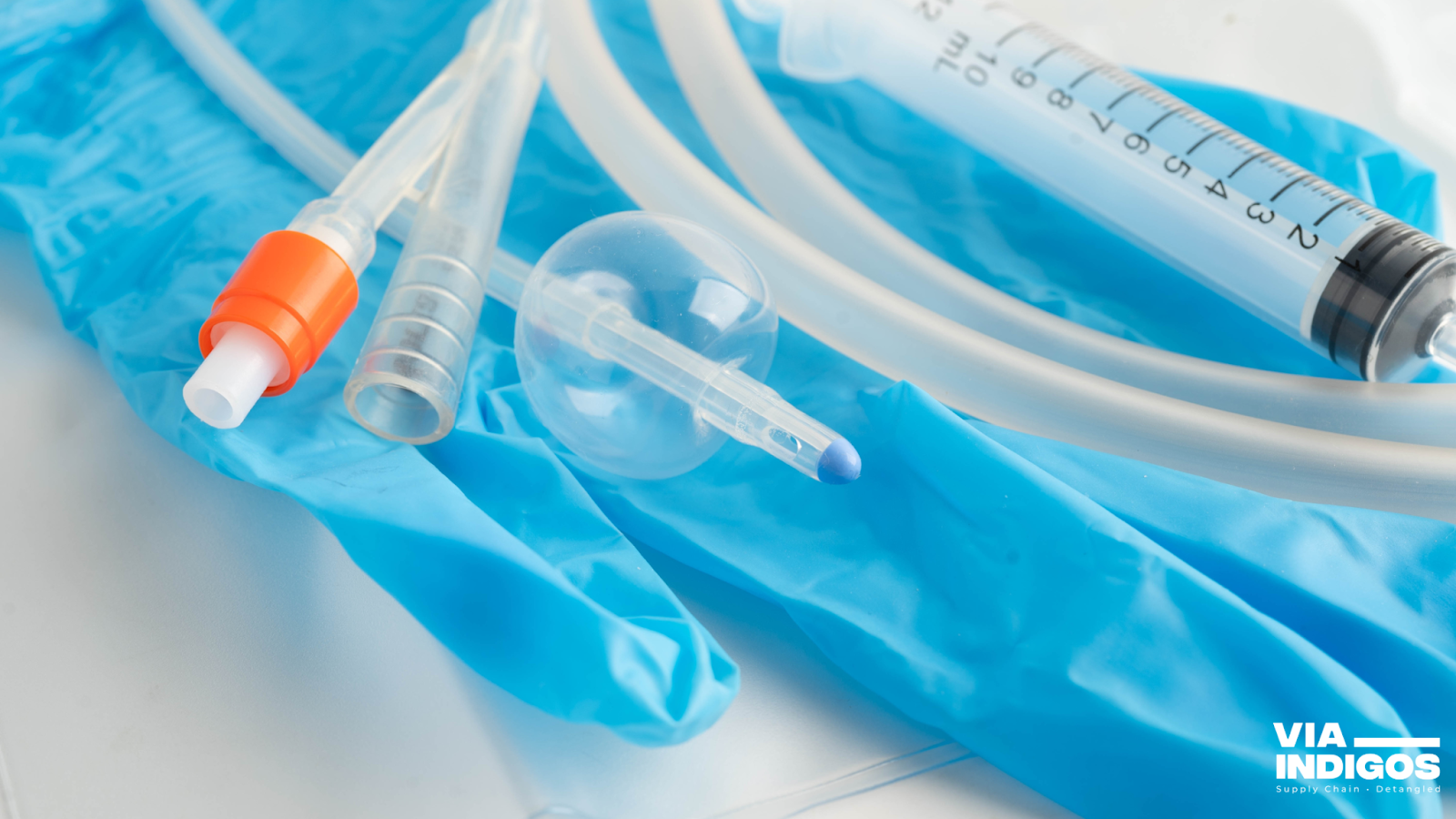
Precision in Healthcare: Blow-Molded Catheter Tubing Engineered for Exact Internal Diameters.
3. Consumer Goods
Precision components include:
• Reusable water bottles: Designed for durability, ergonomic handling, and leak-proof seals.
• Storage containers: Custom shapes and sizes for specific household or commercial uses.
• Child safety seats: Hollow parts molded to strict safety standards for impact resistance. From water bottles to household containers, custom blow molding enables the production of durable, aesthetically pleasing products at scale.

Extrusion Blow Molding: Blow Molded Containers Built for Durability and Efficiency. Perfect for industrial storage, logistics, and more.
4. Industrial Applications
Precision components include:
• Chemical storage tanks: Designed to resist corrosion and handle specific chemical properties.
• Tool housings: Protect delicate instruments and withstand rugged use.
• HVAC ducting: Precision-molded parts ensure efficient air distribution in industrial systems. Blow-molded parts are also found in industrial settings, where they are used for storage tanks, tool housings, and other robust components.
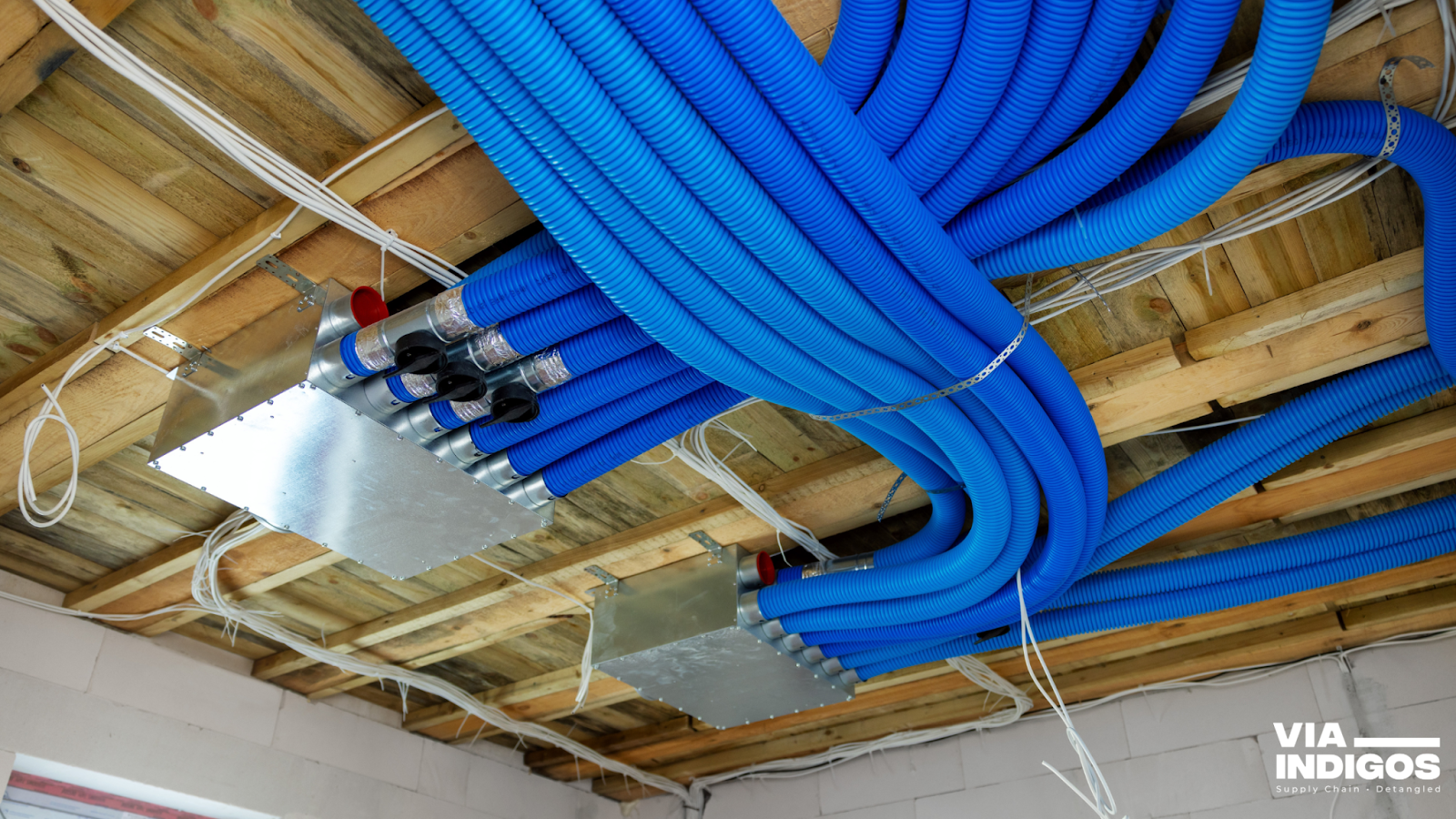
Streamlined Airflow: Precision Blow-Molded HVAC Ducting for Optimal Industrial Air Distribution.
The Custom Blow Molding Process
The custom blow molding process involves several key steps, each tailored to achieve the desired precision and quality:
Step 1: Design and Prototyping
Manufacturers work closely with clients to develop detailed CAD designs and prototypes. Advanced simulations may be used to predict how the plastic will behave during molding.
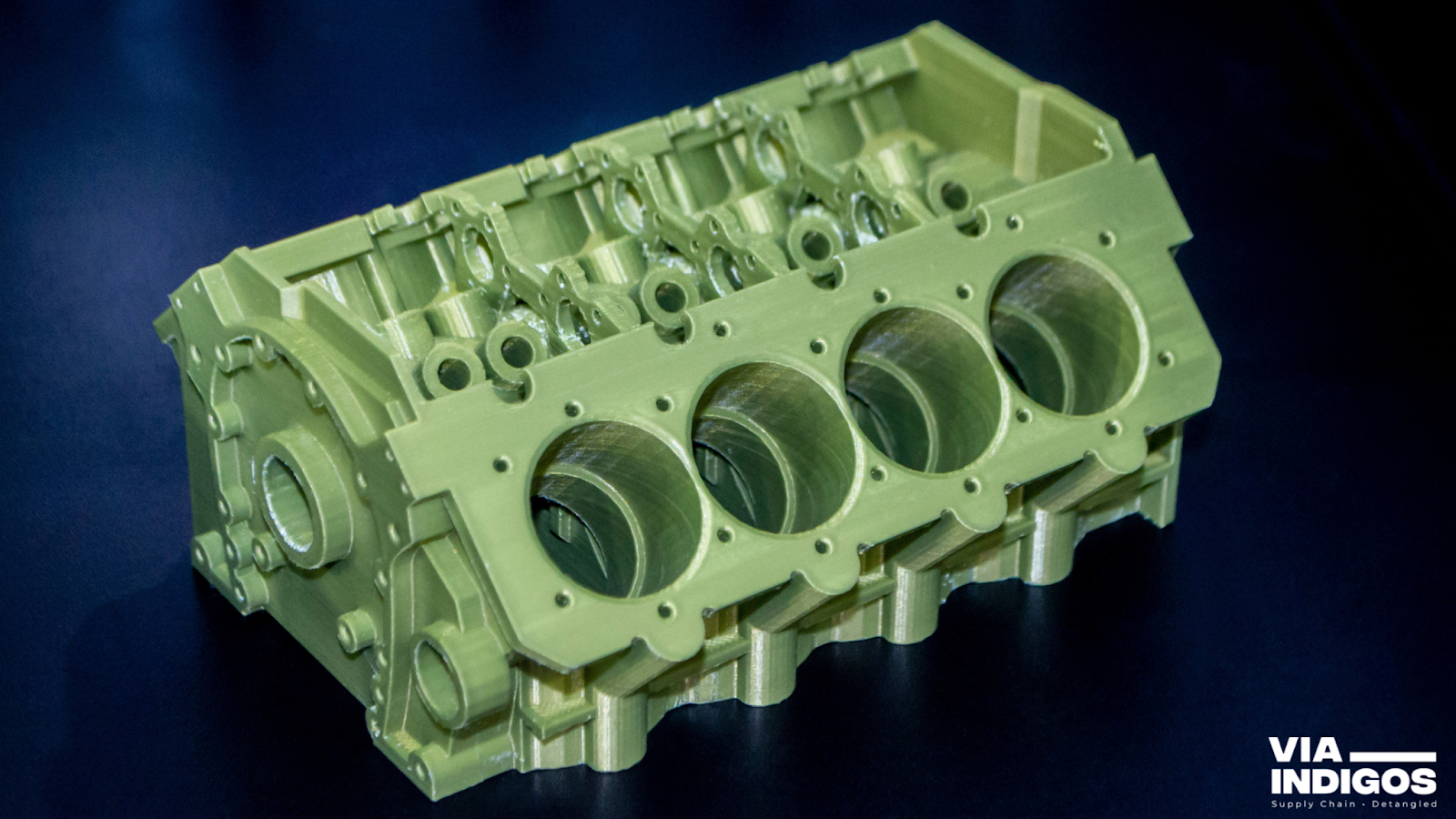
Precision Design and Prototyping – From detailed CAD designs to advanced simulations, our blow molding process begins.
Step 2: Mold Fabrication
Molds are machined to exact specifications, often using materials like aluminum or steel. Precision is paramount, as the mold determines the final product’s quality.
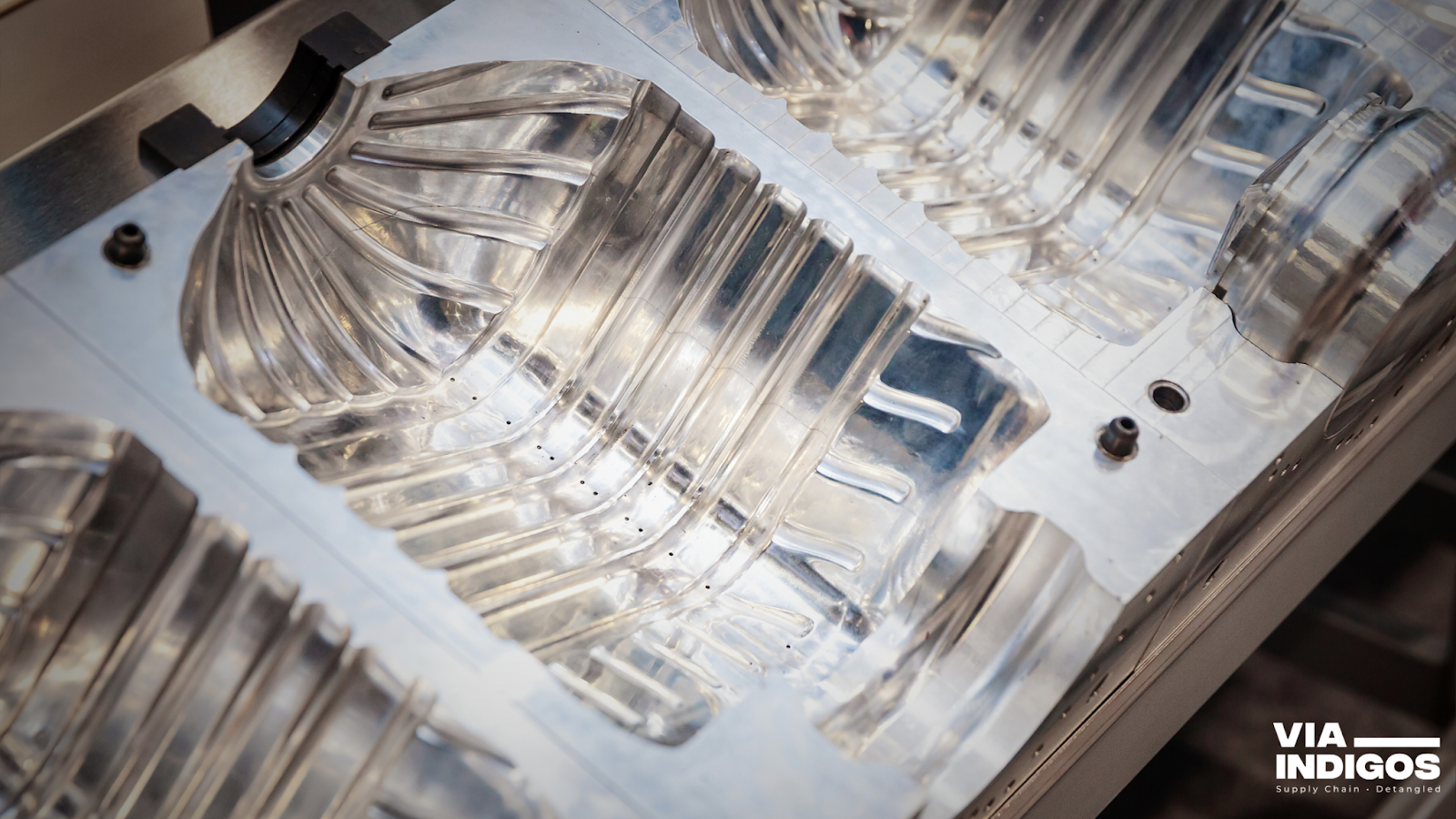
Crafting Precision: High-Quality Aluminum and Steel Molds Engineered to Perfection.
Step 3: Material Selection
The choice of thermoplastic is critical. Manufacturers consider factors like strength, flexibility, chemical resistance, and cost when selecting materials.
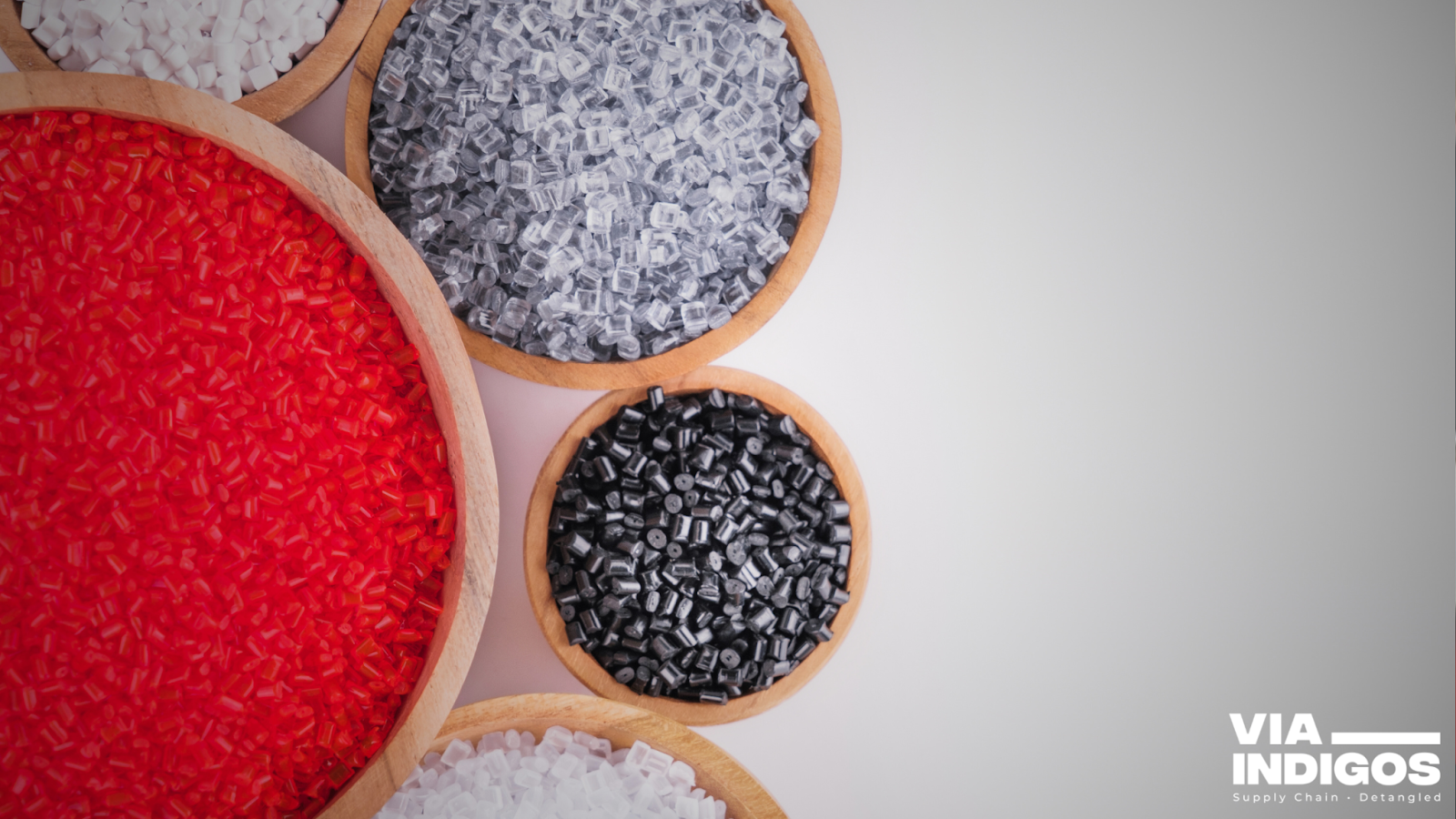
Choosing the Right Thermoplastic for Blow Molding. Strength, flexibility, and chemical resistance are carefully evaluated to deliver superior results.
Step 4: Molding and Production
Plastic is heated to its melting point, then formed into a parison (a hollow tube). Air pressure inflates the parison into the mold, where it cools and solidifies.
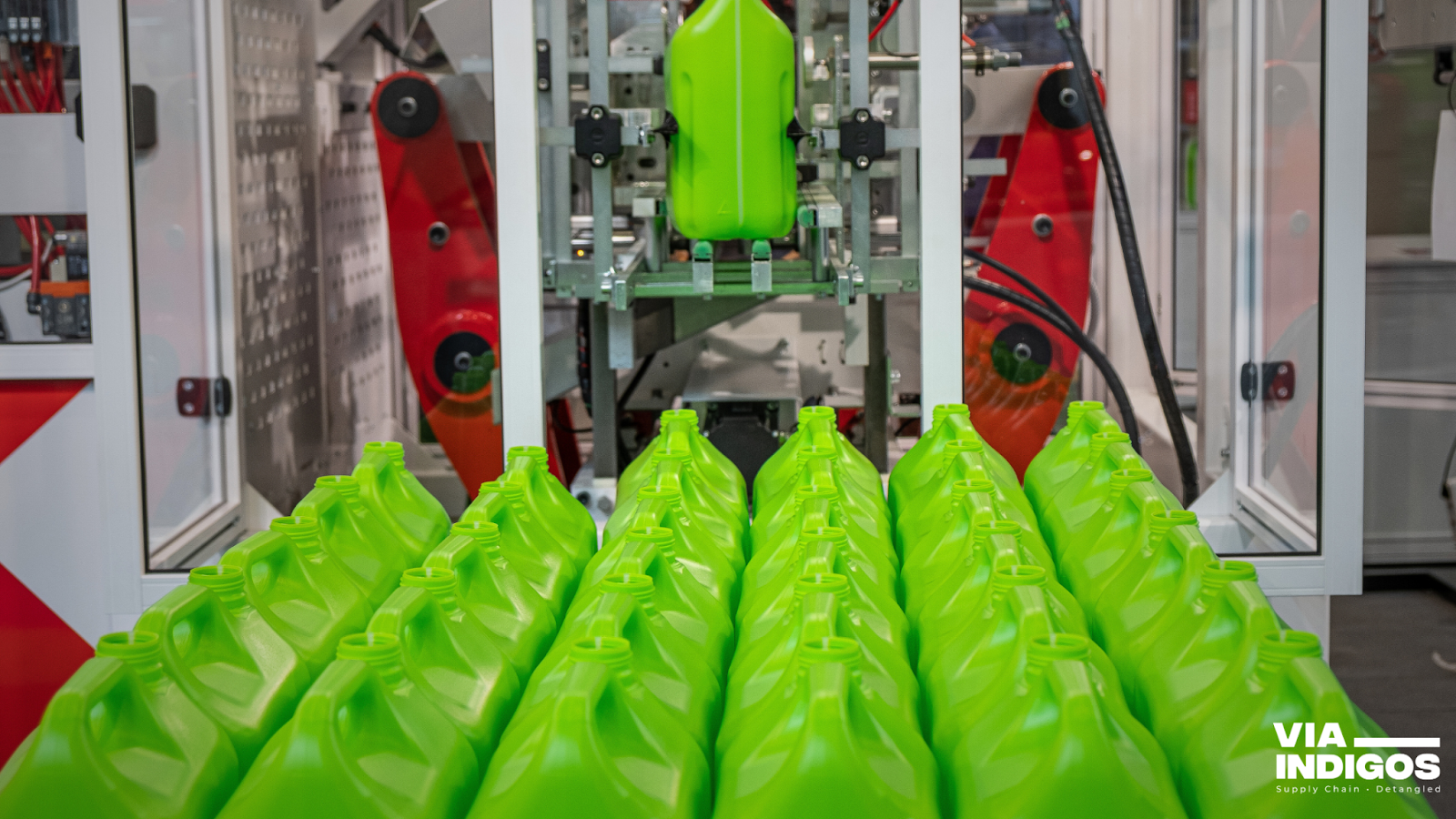
Jerry Cans Production in Motion: Blow Molding Excellence at Scale.
Step 5: Finishing and Quality Control
Once molded, the component undergoes finishing processes such as trimming, drilling, or surface treatments. Rigorous quality checks ensure that each piece meets the required specifications.
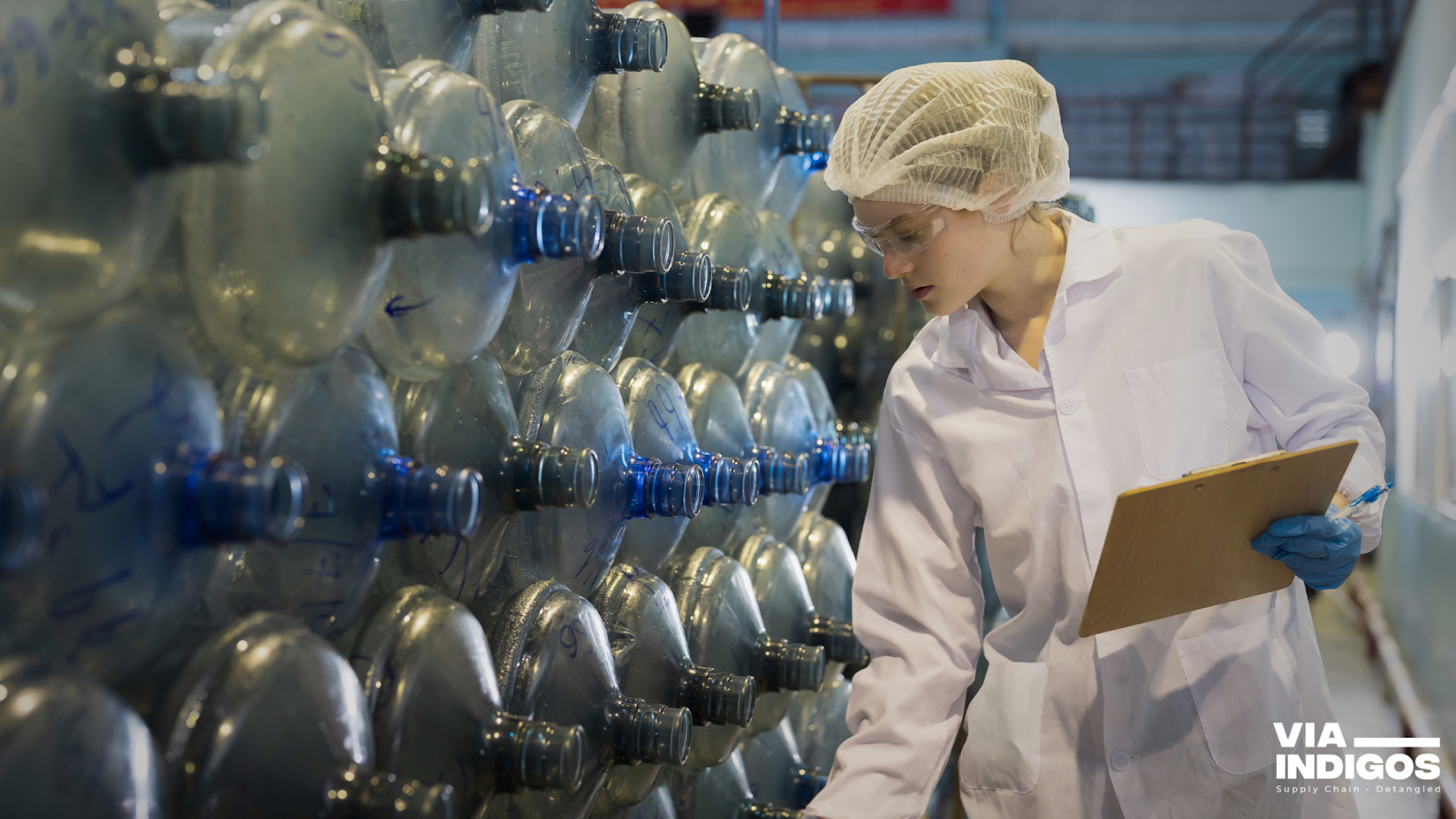
From Precision Molding to Perfection: followed by rigorous quality checks to meet exact specifications.
Challenges and Innovations in Custom Blow Molding
Despite its many advantages, custom blow molding comes with challenges, such as:
• Mold Costs: High initial mold fabrication costs can be a barrier for small production runs. Custom molds can cost anywhere from $5,000 to $100,000, depending on complexity and material. For small-scale production, this cost can account for up to 40% of the initial budget.
• Material Wastage: Scrap material from trimming or defective parts can add to costs. Studies show that 5-15% of material used in blow molding is wasted due to trimming and defects. This is being addressed with advanced recycling systems, which can recover up to 80% of scrap material for reuse.
However, innovations in blow molding technology are addressing these issues:
• Recyclable Materials: Many manufacturers now use recyclable plastics to reduce waste.
• Advanced Controls: IoT-enabled machines allow for real-time monitoring and adjustments, minimizing defects and downtime.
Conclusion
Custom blow molding is a powerful tool for creating precision plastic components that meet the unique needs of diverse industries. Its ability to combine design flexibility, material customization, and cost efficiency makes it a preferred choice for manufacturers worldwide. Whether you’re designing parts for a car, medical device, or consumer product, custom blow molding delivers the precision and reliability you need to succeed.
Ready to explore how custom blow molding can benefit your business? Contact us today to bring your vision to life!
Why VIA INDIGOS for Blow Molding and Precision Plastic Manufacturing?
At VIA INDIGOS, we specialize in connecting global businesses with India’s unmatched capabilities in custom blow molding. From air ducts and fluid reservoirs to reusable water bottles and storage tanks, we deliver precision plastic components tailored to your specifications. Our end-to-end supply chain management streamlines production, reduces costs, and ensures timely delivery, allowing your business to scale efficiently.
We go beyond being a supplier—we act as your on-ground manufacturing partner, ensuring every stage of production meets your exacting standards. Leveraging India’s thriving manufacturing ecosystem and the benefits of China +1 strategies, we help you mitigate risks, reduce tariffs, and gain a competitive edge in today’s dynamic markets.
What Sets VIA INDIGOS Apart?
• Strategic Export Advantage: India is one of the largest exporters of plastics, with exports exceeding $12 billion annually. Partnering with VIA INDIGOS allows you to tap into this thriving market while optimizing your supply chain.
• Certified and Trusted Production: Our network of production partners meets stringent global standards, including ISO 9001, IATF 16949, and FDA certifications for medical-grade components.
• Tailored Solutions for Diverse Needs: Whether you need durable chemical storage tanks or lightweight medical components, our expertise spans industries and applications.
• Advanced Blow Molding Processes: We utilize cutting-edge technology, including extrusion, injection, and stretch blow molding, to achieve complex geometries and unparalleled precision.
• End-to-End Support: From prototyping and mold fabrication to quality control and logistics, we manage every aspect of your production journey.
• On-Ground Presence: Our India-based teams ensure seamless communication, real-time updates, and stringent oversight at every stage of the process.
Why Choose India for Custom Blow Molding?
India’s manufacturing sector is rapidly expanding, with exports of plastic and related products growing by 14% annually. By working with VIA INDIGOS, you gain access to a cost-effective, high-quality production base that supports large-scale manufacturing without compromising on quality or timelines.
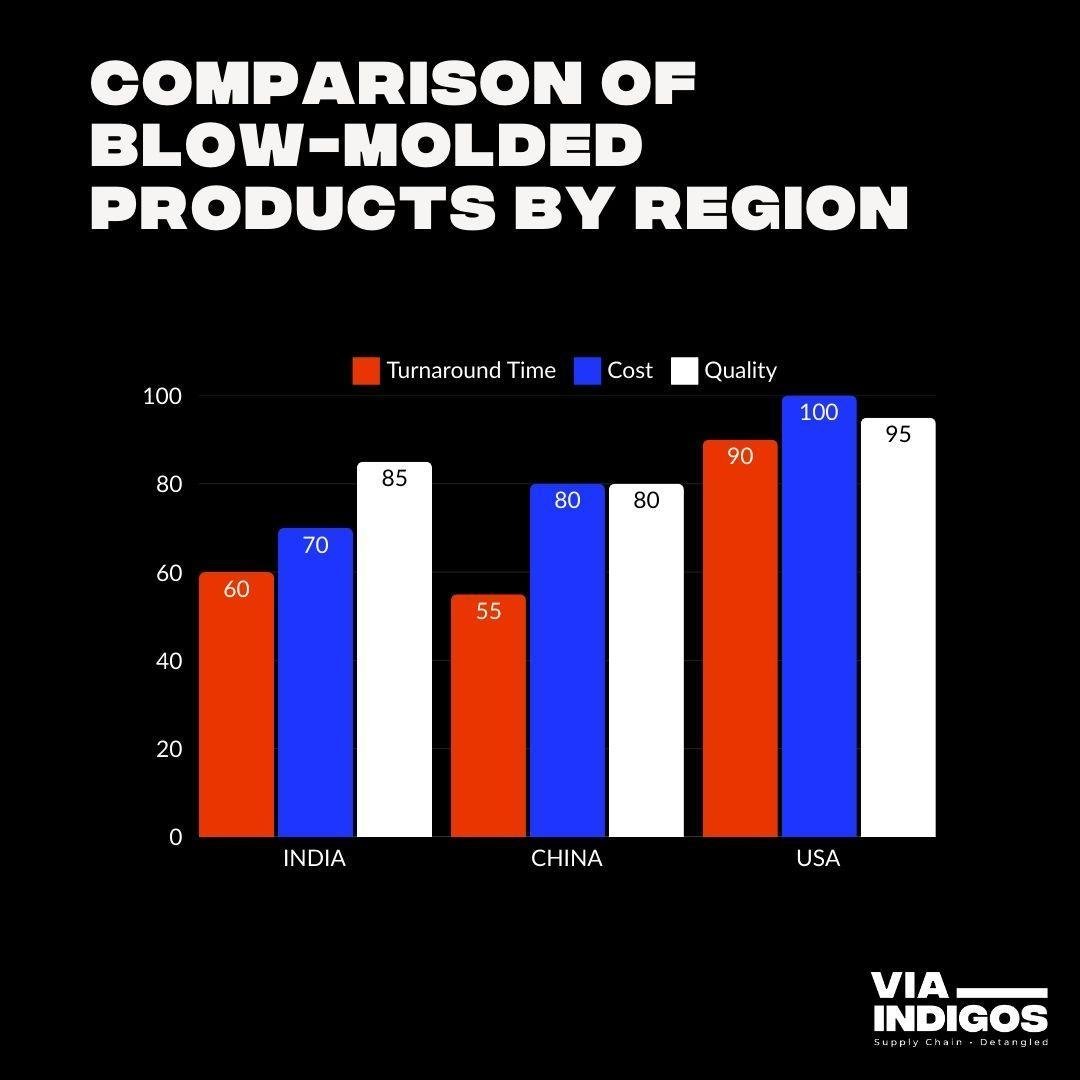
Driving Value for Your Business
Cost Efficiency: With labor and production costs up to 40% lower than in Western markets, we deliver high-quality products at a fraction of the cost.
- Speed to Market: Our streamlined processes and extensive network of suppliers ensure that your products are delivered faster, helping you stay ahead of the competition.