Streamlining Sheet Metal Fabrication: Key Practices to Prevent Rework from Design to Delivery
- VIA INDIGOS
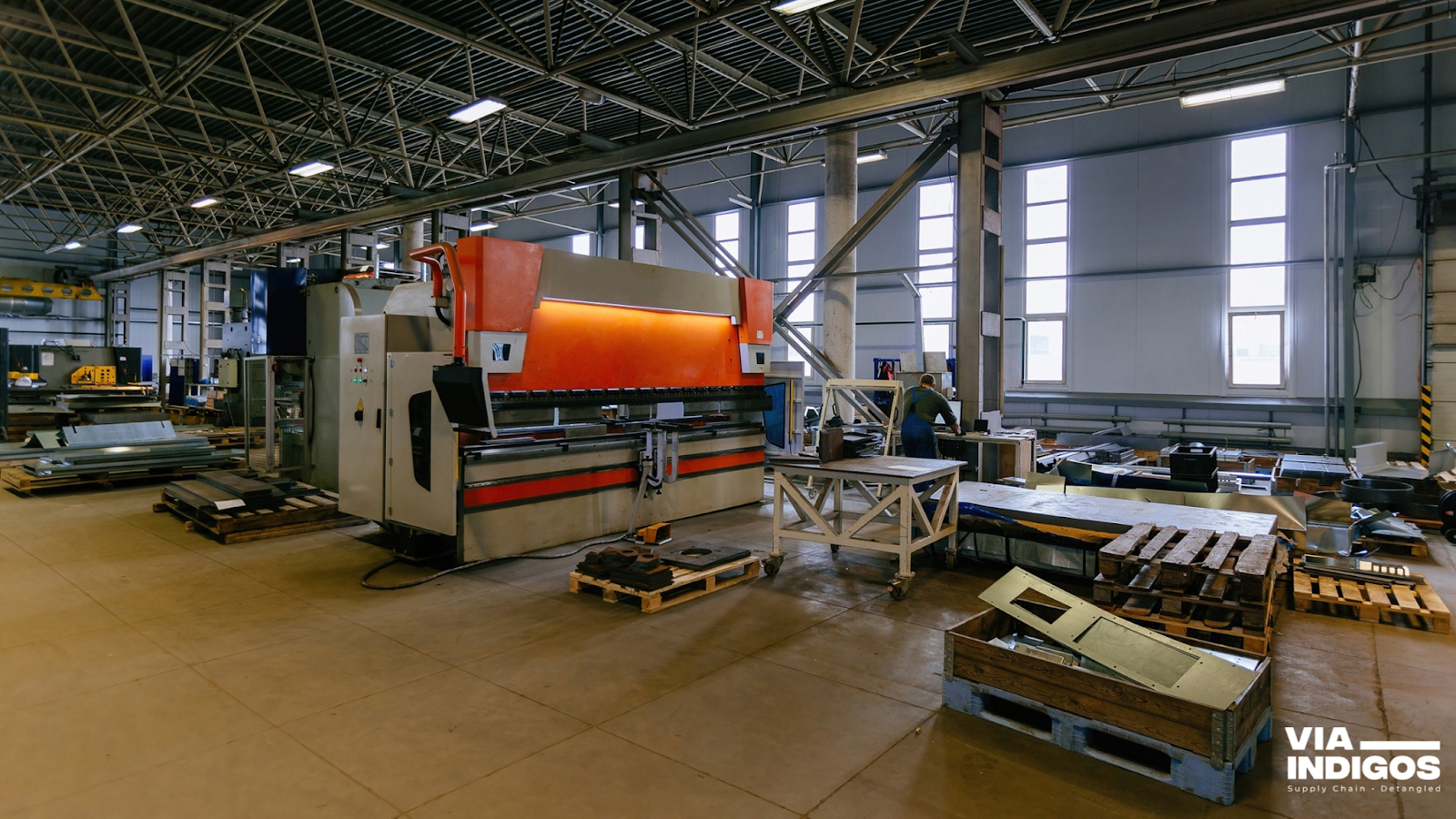
Rework, correcting or modifying a product after its initial production, is a costly and time-consuming challenge in sheet metal fabrication. Beyond its immediate financial implications, rework can disrupt project timelines, diminish customer satisfaction, and lead to inefficiencies across the production process. Preventing rework isn’t just a cost-saving measure; it’s a critical aspect of maintaining quality, meeting deadlines, and ensuring a seamless production pipeline.
We believe that a systematic, end-to-end approach to fabrication can significantly reduce the likelihood of errors. Here’s an in-depth guide to streamlining sheet metal fabrication and minimizing rework, from the design phase to final delivery.
Design with Precision and Intent
The foundation of efficient sheet metal fabrication lies in the design phase, where every detail must be scrutinized and optimized to ensure a seamless production process. A well-planned design serves as the blueprint for success, acting as a guide that shapes the subsequent stages of fabrication. It anticipates challenges, eliminates inefficiencies, and enhances the alignment between design specifications and manufacturing capabilities. By addressing potential bottlenecks and inaccuracies early, this phase lays the groundwork for consistent quality, faster turnaround times, and cost savings throughout the project lifecycle. Investing time and effort into thoughtful design not only facilitates smooth production but also preempts potential challenges, transforming complexities into streamlined solutions.
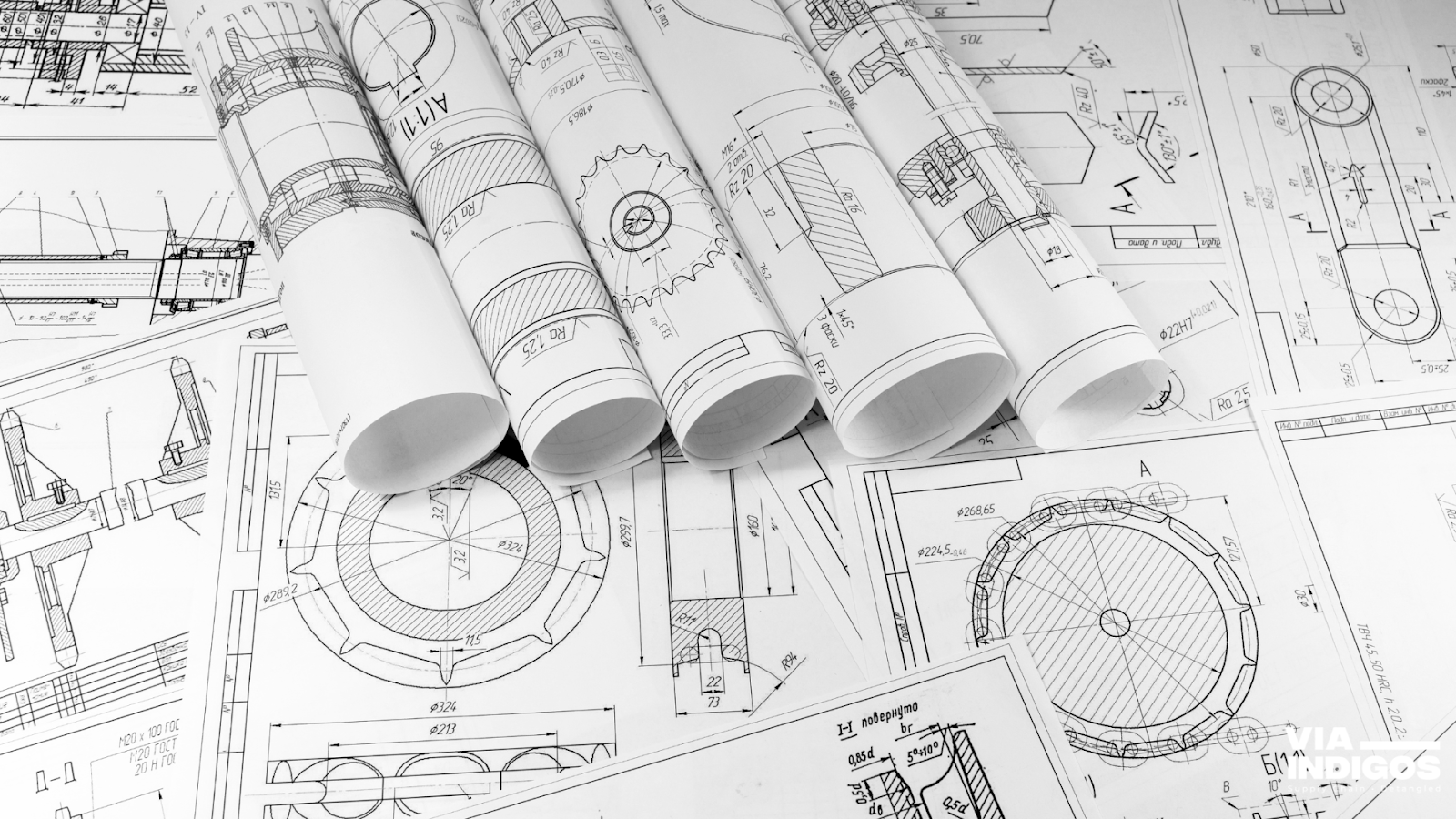
Optimized designs for seamless sheet metal fabrication.
Incorporate Design for Manufacturability (DFM)
Incorporating Design for Manufacturability (DFM) is a crucial step in ensuring efficient and error-free sheet metal fabrication. DFM principles focus on designing parts that align seamlessly with manufacturing processes, minimizing the risk of production issues and reducing overall costs. For example, studies have shown that addressing manufacturability in the design phase can lower production costs by up to 30% and decrease lead times by 20%.
Key DFM Practices:
• Evaluate Bend Radii: Ensure that bend radii conform to the material’s natural properties and tooling capabilities. A standard bend radius equal to or greater than the material thickness prevents cracking and ensures consistent quality.
• Assess Material Thickness: Design with uniform material thickness to avoid unnecessary adjustments during fabrication. Non-standard thicknesses may require special tools, increasing production time and costs.
• Tooling Constraints: Account for the capabilities and limitations of available machinery. This includes punch sizes, die clearances, and cutting methods, which can significantly affect production feasibility.
By adopting these practices early in the design process, you can avoid costly redesigns and streamline manufacturing.
DFM principles ensure that your designs align with manufacturing capabilities. By evaluating factors like bend radii, material thickness, and tooling constraints early on, you can eliminate potential production issues. Avoid overcomplicated features that could increase fabrication difficulty or lead to inaccuracies.
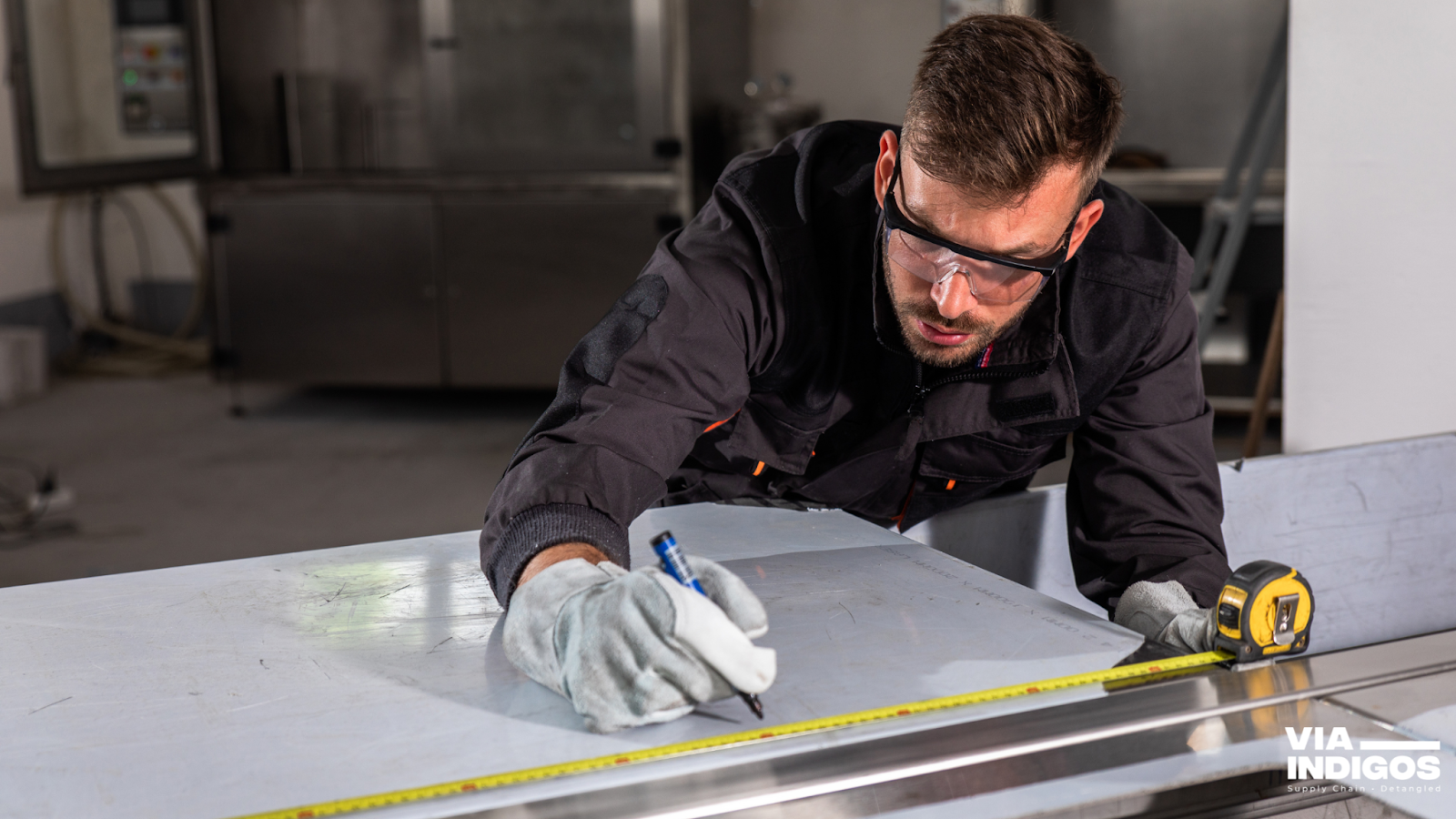
Precision planning for efficient sheet metal fabrication.
Optimize for Simplicity
Simplifying designs is not only about reducing visual complexity but also about enhancing manufacturability and reliability. Complex designs often introduce unnecessary challenges, leading to higher rates of error and rework. Simplified designs reduce production time, material waste, and costs, creating a win-win for manufacturers and clients alike.
Practical Guidelines for Simplicity:
• Minimize Intricate Shapes: Eliminate overly detailed features that may require specialized tools or additional steps during fabrication. For instance, avoid tight internal corners and instead use fillets or rounded edges for ease of cutting and bending.
• Keep Bend Consistency: Use consistent bend angles and radii across the design. Inconsistent bends can lead to misalignments during assembly and increase rejection rates.
• Avoid Excessive Features: Features like unnecessary slots, holes, or embossments complicate manufacturing and increase the chance of errors. Stick to essential elements to maintain functional integrity.
By adhering to these principles, manufacturers can cut fabrication times by up to 15% and achieve better overall quality.
Simpler designs are easier and faster to fabricate. Minimize intricate shapes and keep bends consistent. For instance, using a standard bend radius equal to or greater than the sheet’s thickness reduces strain on the material and ensures consistent quality.
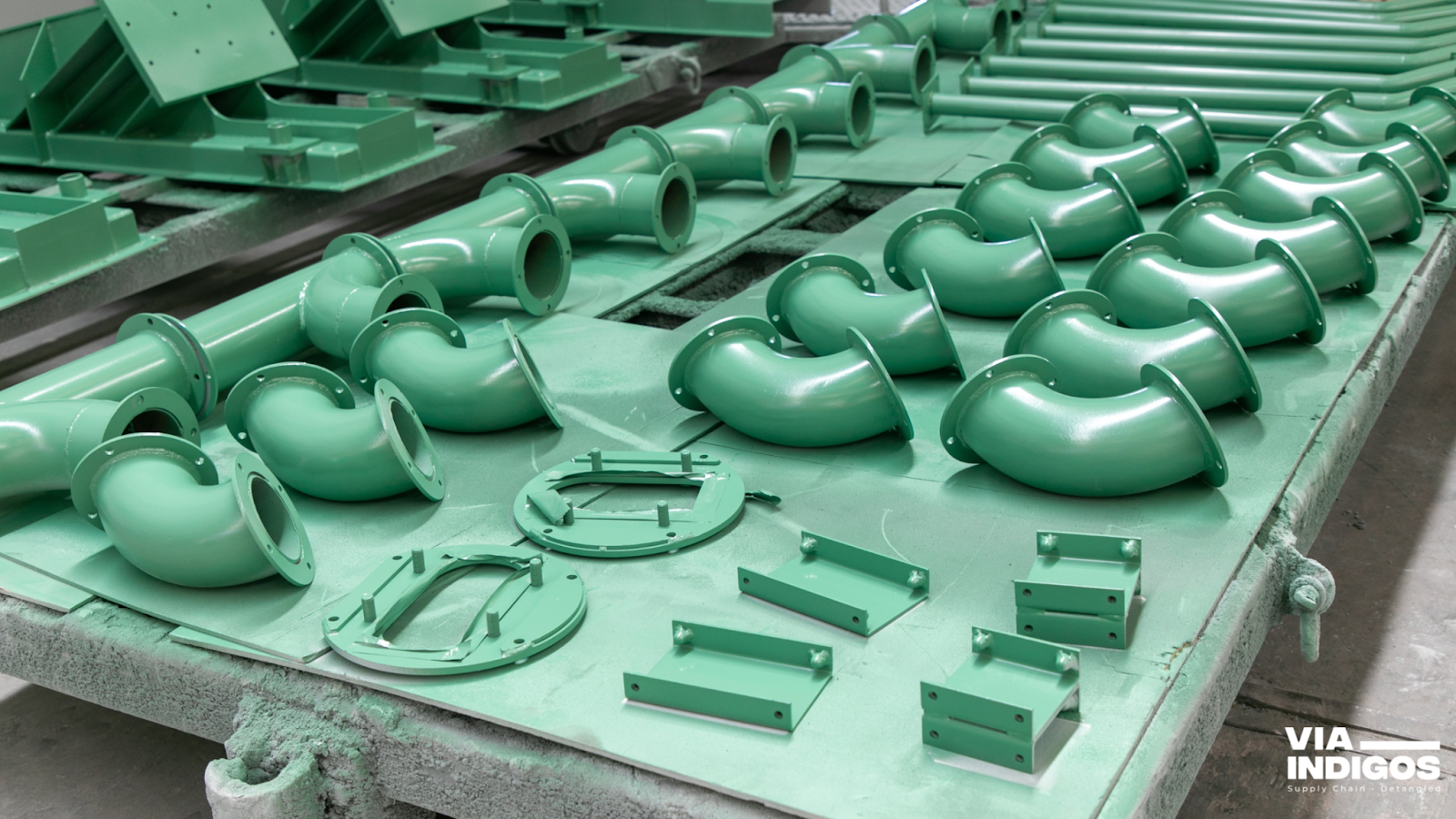
Streamlining shapes and bends for faster fabrication and reduced errors.
Account for Tolerances
Setting accurate and achievable tolerances is a cornerstone of successful sheet metal fabrication. Overly tight tolerances can lead to production inefficiencies, increased rework, and higher costs, while loose tolerances may compromise the functionality and fit of the final product.
Best Practices for Tolerance Management:
• Define Critical Tolerances Clearly: Prioritize tolerances for critical features such as mating surfaces, hole alignments, and edge distances. Non-critical dimensions can allow for greater flexibility.
• Balance Precision and Practicality: Aim for tolerances that manufacturing equipment can reliably achieve. For example, a laser cutter can typically achieve tolerances within ±0.005 inches, whereas manual processes may vary more significantly.
• Communicate with Fabricators: Collaborate with your manufacturing team to understand their equipment’s capabilities. Aligning design tolerances with their machinery’s performance ensures smoother production.
Statistics reveal that mismatched tolerances contribute to over 50% of rework cases in sheet metal projects. By carefully managing tolerances, you can reduce the risk of errors and maintain optimal performance during assembly.
Precise tolerances are crucial in sheet metal fabrication. Establish clear, achievable tolerances to avoid misfits or assembly issues. Overly tight tolerances can lead to unnecessary rework during the assembly process.
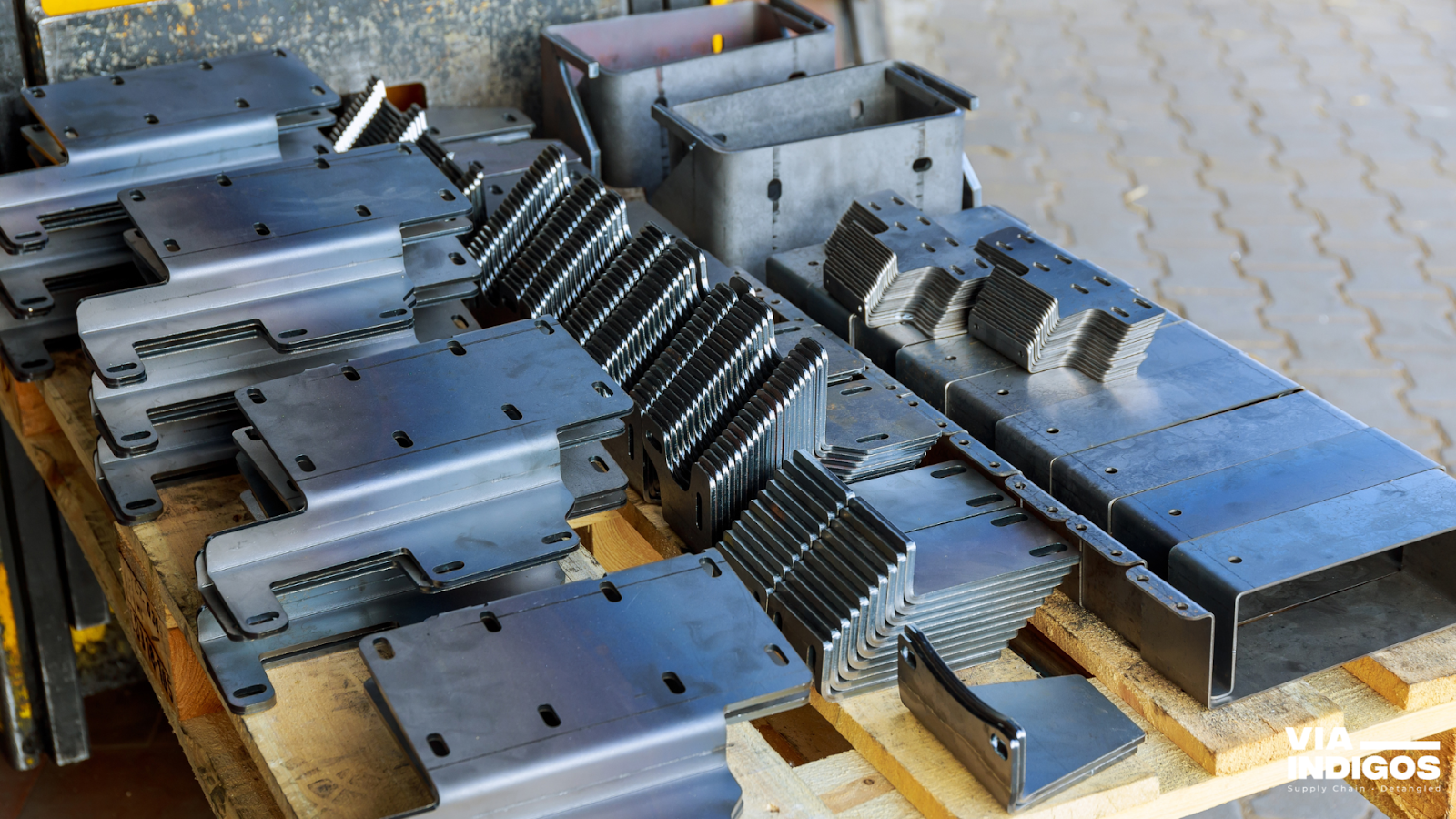
Precision-built sheet metal parts: Accurate tolerances for flawless assembly.
Select the Right Materials and Gauges
Material selection is one of the most significant factors influencing the success of sheet metal fabrication. The right choice ensures cost-effectiveness, manufacturability, and optimal performance of the final product. A poor selection, on the other hand, can lead to production bottlenecks, unnecessary rework, and increased expenses.
Standardize Material Choices
Standardizing materials and gauges simplifies procurement and manufacturing processes. Using widely available materials reduces lead times, ensures consistent quality, and minimizes compatibility issues during production. For example, selecting a common gauge like 16-gauge steel for structural applications can help streamline operations.
Benefits of Standardization:
• Reduced Lead Times: Widely used materials are more readily available, cutting down on sourcing delays.
• Minimized Errors: Standard materials are well-documented and familiar to fabricators, reducing variability and production errors.
• Cost Efficiency: Bulk purchasing of standard materials can lead to significant savings over time.
Balance Strength and Workability
While strong materials like stainless steel or titanium offer durability, they can be more challenging to work with due to their resistance to bending and cutting. Conversely, softer metals like aluminum are easier to handle but may not provide the necessary strength for certain applications.
Key Considerations:
• Application Needs: Determine whether the design prioritizes strength, corrosion resistance, or lightweight properties.
• Machinability: Softer materials like aluminum 5052 are easier to bend and cut, reducing fabrication time.
• Production Efficiency: Striking the right balance between strength and workability can reduce machining time and improve overall productivity.
Supporting Data
Studies indicate that material-related errors account for nearly 25% of production inefficiencies in sheet metal fabrication. By carefully selecting materials and standardizing gauges, manufacturers can lower these inefficiencies by up to 15%, leading to smoother production cycles and reduced waste.
Example: In automotive applications, high-strength low-alloy (HSLA) steel is commonly used for its balance of strength and formability. Its properties allow for precise forming without excessive tool wear, which helps reduce rework and increases part longevity.
By choosing materials that meet both performance and manufacturability criteria, manufacturers can achieve superior results while minimizing the risk of errors and production delays.
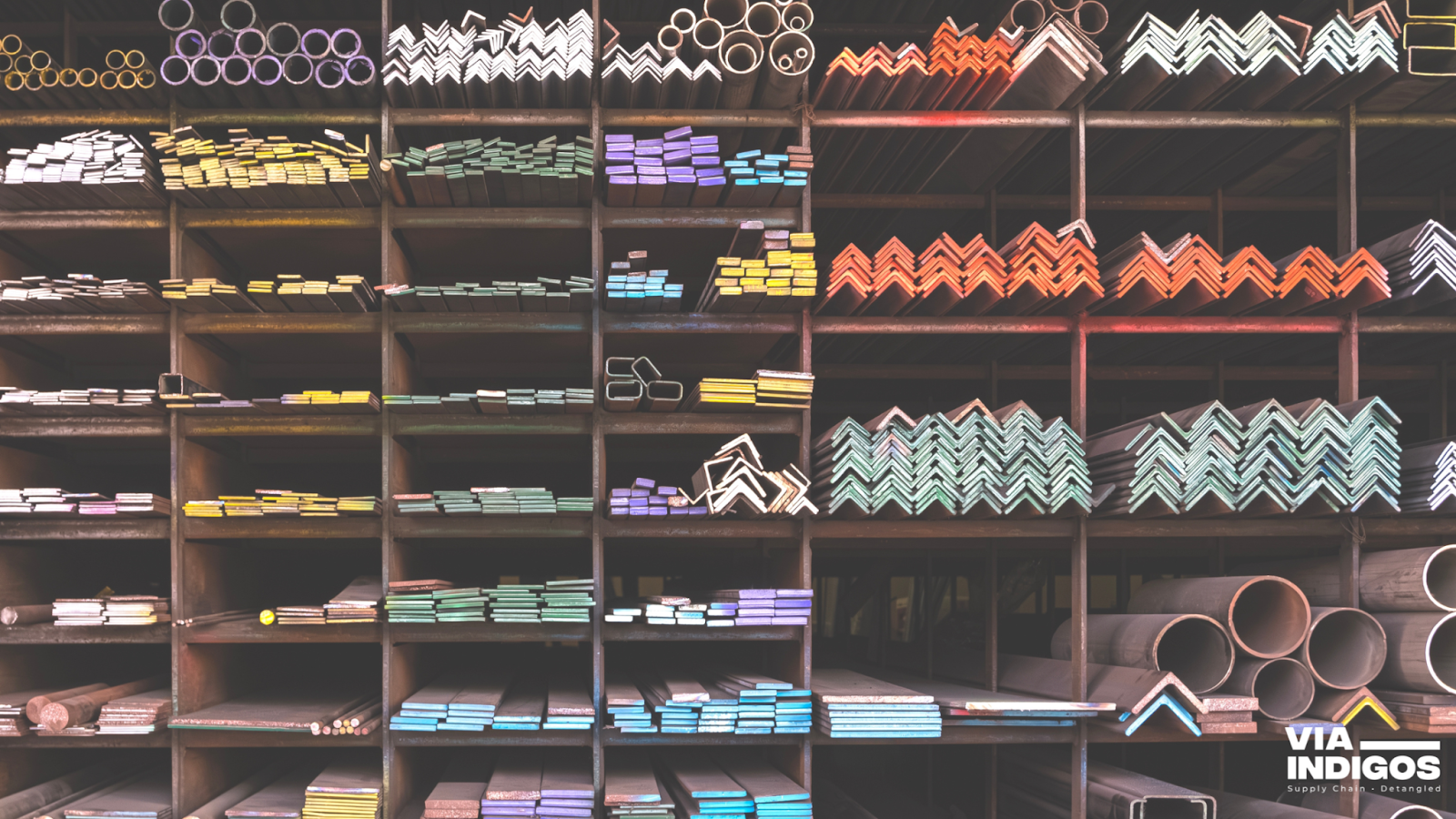
Streamline fabrication with the right materials and gauges
Invest in Prototyping and Simulation
Prototyping and simulation are indispensable tools in modern sheet metal fabrication. They provide a risk-free environment to test designs, identify potential flaws, and ensure manufacturability before committing to full-scale production. This proactive approach saves time and reduces costs associated with rework and material waste.
Leverage Virtual Testing
Advanced simulation software allows manufacturers to predict and resolve issues at the design stage. These tools can analyze factors like stress distribution, deformation, and thermal effects, ensuring the design’s integrity under real-world conditions.
Benefits of Virtual Testing:
• Cost Reduction: Detecting and addressing issues in the virtual phase can cut prototyping expenses by up to 50%.
• Accelerated Timelines: Virtual testing reduces the need for multiple physical prototypes, speeding up the development process.
• Improved Accuracy: High-precision simulations provide detailed insights, enabling fine-tuning of designs for optimal performance.

Prototyping precision: Streamline fabrication with risk-free testing and simulations.
Create Physical Prototypes
Despite the advancements in virtual testing, physical prototypes remain critical for validating functionality, fit, and finish. Hands-on testing provides insights that simulations may not fully capture, such as assembly challenges or user interaction.
Steps for Effective Prototyping:
• Start with Low-Fidelity Models: Use inexpensive materials for initial prototypes to quickly test basic concepts.
• Iterate Based on Feedback: Incorporate learnings from physical testing into subsequent design iterations.
• Finalize with Production-Grade Materials: Ensure the final prototype matches the intended materials and processes for accurate validation.
Investing in both virtual and physical prototyping ensures a well-rounded approach to design validation, significantly reducing the likelihood of costly errors during full-scale production.
Before committing to full-scale production, validate your designs through prototyping and simulation tools.
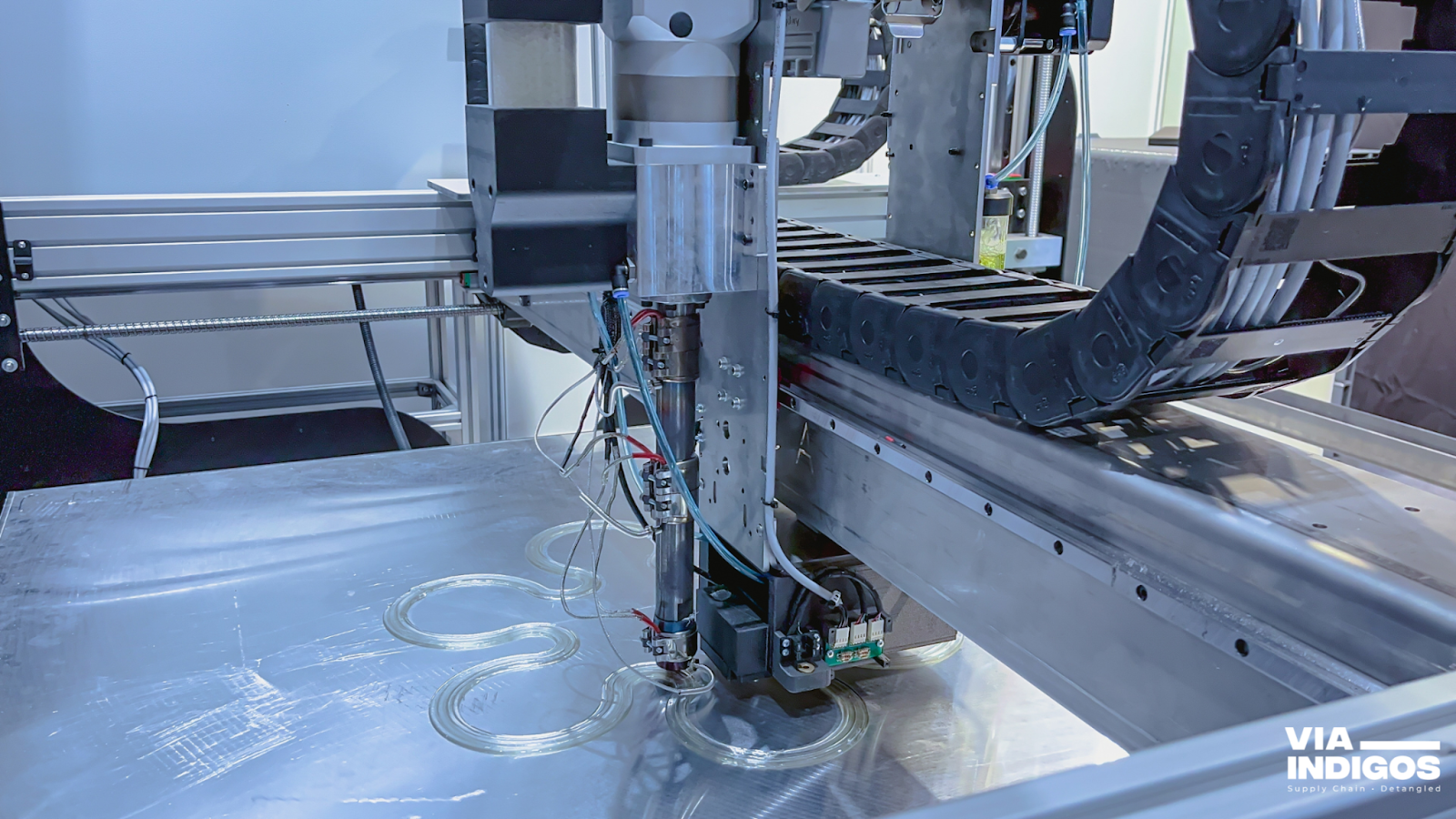
Physical prototypes ensure precision and functionality.
Strengthen Collaboration Across Teams
Effective collaboration is the backbone of any successful sheet metal fabrication project. Miscommunication or lack of alignment between teams can lead to errors, delays, and rework. Building a culture of teamwork and utilizing the right tools can streamline the entire fabrication process.
Centralized Communication Platforms
Centralized platforms ensure that all stakeholders, from designers to fabricators, have access to the latest project information. Tools like project management software, shared cloud storage, and instant messaging systems help maintain clarity and reduce misunderstandings.
Advantages:
• Real-Time Updates: Teams can access the latest versions of designs and specifications instantly, minimizing errors caused by outdated information.
• Improved Accountability: Assigning tasks and tracking progress ensures that everyone stays on schedule.
• Enhanced Feedback: Centralized systems make it easy to share and review feedback in one place.
Encourage Feedback Loops
Creating an open environment for feedback ensures that potential issues are identified and resolved early. Regular meetings and design reviews involving cross-functional teams can catch inconsistencies and improve overall efficiency.
Best Practices:
• Schedule Regular Check-Ins: Weekly or bi-weekly meetings keep everyone aligned.
• Document Lessons Learned: Maintain a record of past challenges and solutions to avoid repeating mistakes.
• Promote Cross-Department Collaboration: Encourage input from production, quality control, and logistics teams during the design phase.
By fostering strong collaboration, manufacturers can significantly reduce errors, improve quality, and ensure timely delivery.
Effective communication between design, engineering, and production teams is crucial for seamless fabrication.
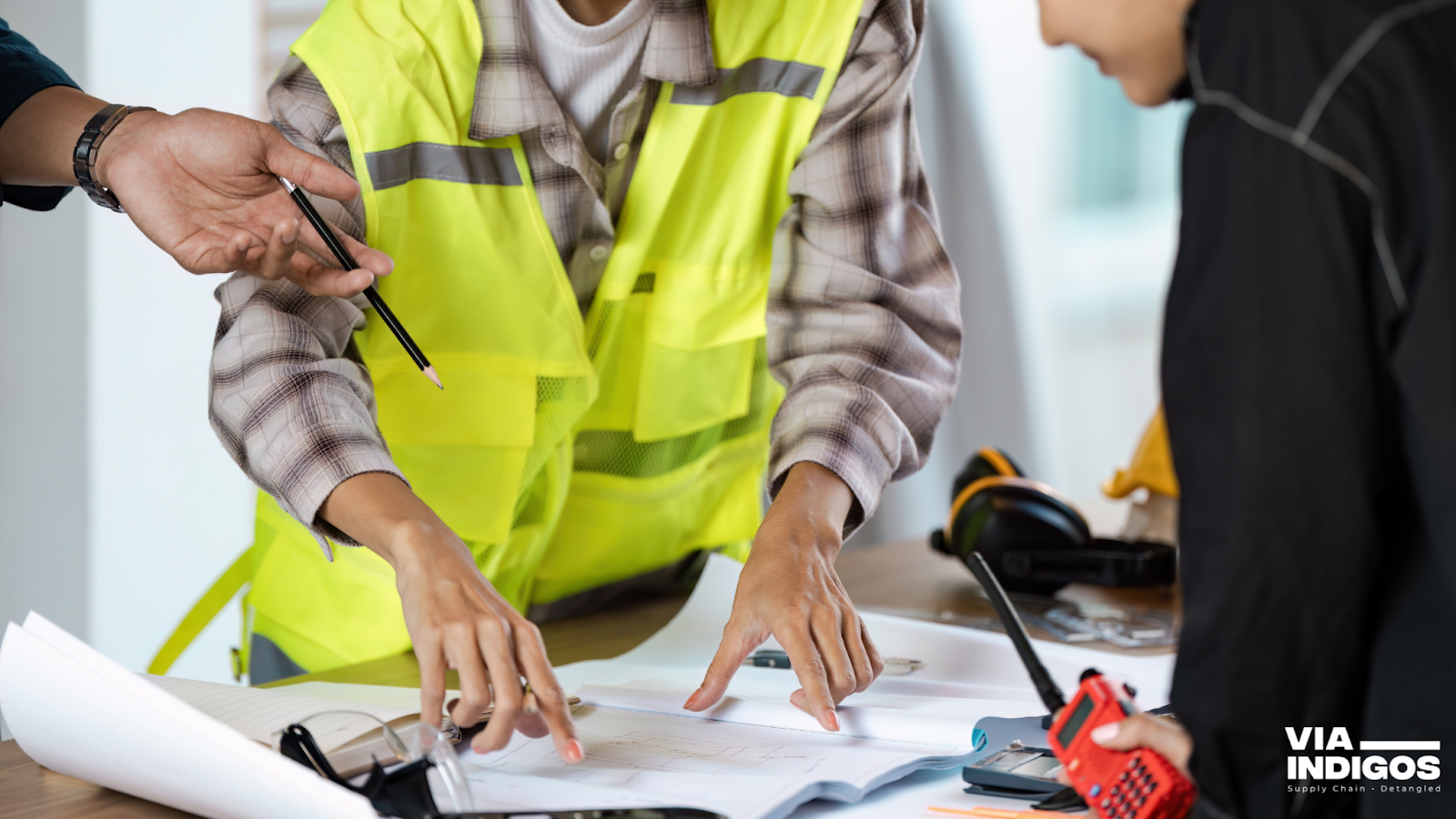
Teamwork drives precision: Collaboration ensures seamless fabrication.
Centralized Communication Platforms
Use collaborative tools to maintain clear communication across departments. Shared access to designs, timelines, and feedback reduces the risk of miscommunication.
Encourage Feedback Loops
Foster an environment where feedback is welcomed and acted upon. Regularly review designs and production plans with all stakeholders to identify potential issues early.
Implement Robust Quality Control Measures
Quality control is essential in preventing defects and ensuring that products meet required standards. A robust quality assurance system reduces rework, boosts customer satisfaction, and enhances overall efficiency.
Perform Regular Inspections
Regular inspections at various stages of fabrication help catch defects early and prevent them from progressing through the production line. Inspections can be manual, visual, or automated, depending on the complexity of the parts.
Key Inspection Points:
• Material Verification: Ensure the correct material and thickness are used before production begins.
• Dimensional Accuracy: Check critical dimensions after cutting, bending, and assembly to ensure they meet specifications.
• Surface Finish: Inspect for scratches, dents, or other imperfections that may compromise quality.
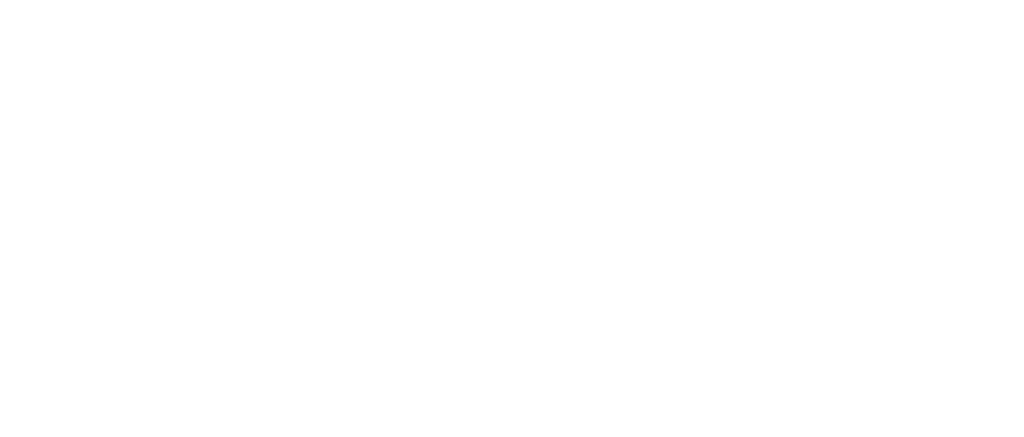
Partnering with the right team ensures streamlined production from start to finish.
Invest in Advanced Tools
Modern quality control tools provide higher precision and reduce the likelihood of human error. Technologies like coordinate measuring machines (CMMs), laser scanners, and automated inspection systems are invaluable in ensuring consistent quality.
Benefits:
• Increased Accuracy: Advanced tools can detect deviations as small as microns, ensuring tight tolerances.
• Faster Turnaround: Automated systems speed up inspections, reducing downtime.
• Comprehensive Reporting: Digital tools generate detailed reports for better traceability and process improvement.
A commitment to stringent quality control measures not only reduces rework but also strengthens customer trust in your manufacturing capabilities.
Preventing rework requires a strong commitment to quality at every stage of fabrication.
Perform Regular Inspections
Schedule quality checks at key stages of production, from material procurement to final assembly. Catching defects early reduces downstream errors.
Invest in Advanced Tools
Modern quality assurance tools, such as coordinate measuring machines (CMMs) and laser scanning, ensure precise measurements and defect detection.
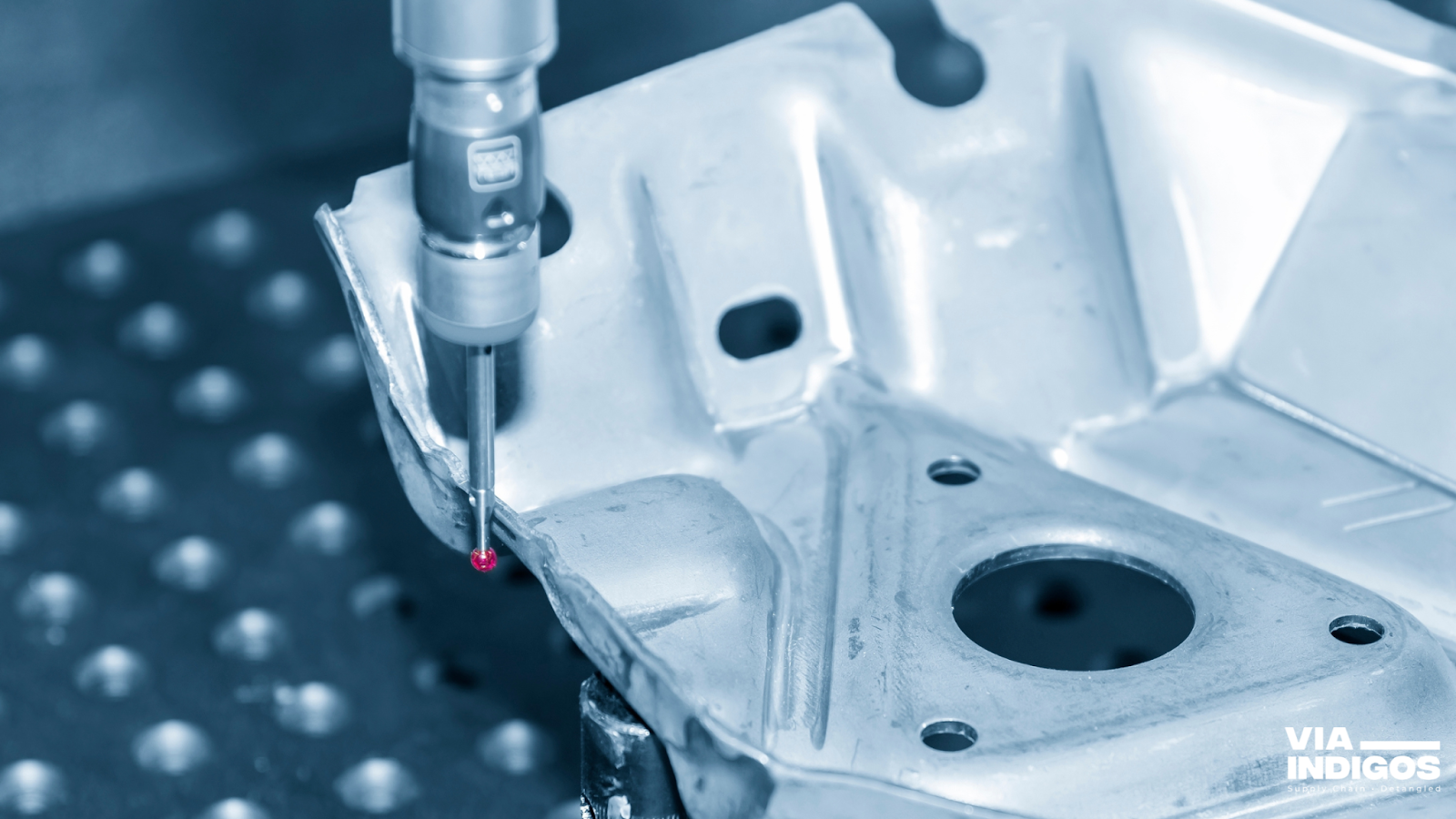
Precision Redefined: CMM ensures tight tolerances and defect-free fabrication.
Standardize Processes with SOPs
Standard Operating Procedures (SOPs) are essential for maintaining consistency and reducing variability in sheet metal fabrication. They provide clear, step-by-step guidelines for each process, ensuring that every team member understands their role and responsibilities.
Document Workflows
Comprehensive documentation ensures that all processes are repeatable and scalable. Well-documented workflows serve as a reference for new employees and help experienced workers troubleshoot issues more effectively.
Tips for Effective Documentation:
• Be Detailed: Include every step, tool, and material required for each process.
• Use Visual Aids: Diagrams, flowcharts, and photos enhance clarity and understanding.
• Update Regularly: Revise SOPs to reflect changes in tools, materials, or techniques.
Train Employees Regularly
Regular training ensures that employees stay updated with the latest industry practices and technologies. A well-trained workforce is more capable of executing complex tasks accurately, reducing errors and rework.
Training Best Practices:
• Conduct Hands-On Workshops: Practical training sessions help employees better understand procedures.
• Offer Refreshers: Periodic refresher courses reinforce key concepts and skills.
• Encourage Skill Development: Promote cross-training to ensure flexibility and adaptability within teams.
Standardized processes supported by regular training create a robust framework for consistent quality and efficiency in fabrication.
Clear and consistent procedures minimize errors and variability in production.
Document Workflows
Maintain detailed Standard Operating Procedures (SOPs) for each step of the fabrication process. These documents serve as a reference point for training and troubleshooting.
Train Employees Regularly
Provide ongoing training to keep your team up-to-date with the latest techniques and tools. A well-trained workforce is better equipped to execute designs accurately, reducing the need for rework.
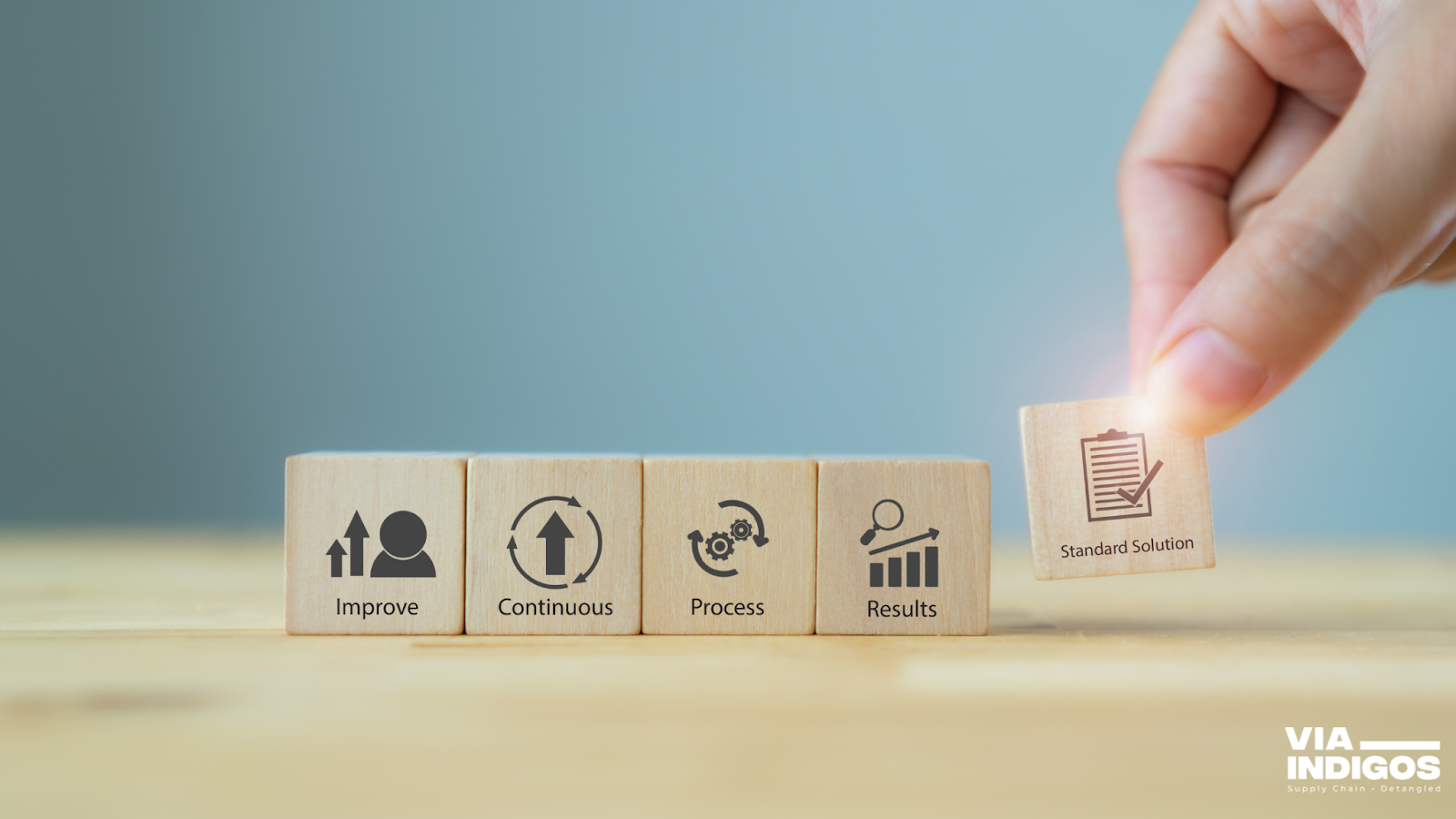
Consistency through SOPs: Standardized processes for efficient fabrication.
Optimize Material Utilization
Efficient material usage is a cornerstone of cost-effective and sustainable sheet metal fabrication. Optimizing material utilization not only minimizes waste but also reduces production costs and environmental impact.
Utilize Nesting Software
Nesting software is a powerful tool for maximizing material usage during the cutting process. By arranging parts strategically on a sheet, nesting minimizes scrap and ensures optimal use of raw materials.
Benefits of Nesting Software:
• Reduced Waste: Studies show that effective nesting can reduce material waste by up to 20%.
• Faster Cutting: Optimized layouts streamline the cutting process, improving overall efficiency.
• Cost Savings: Less waste translates to lower material costs and a more sustainable operation.
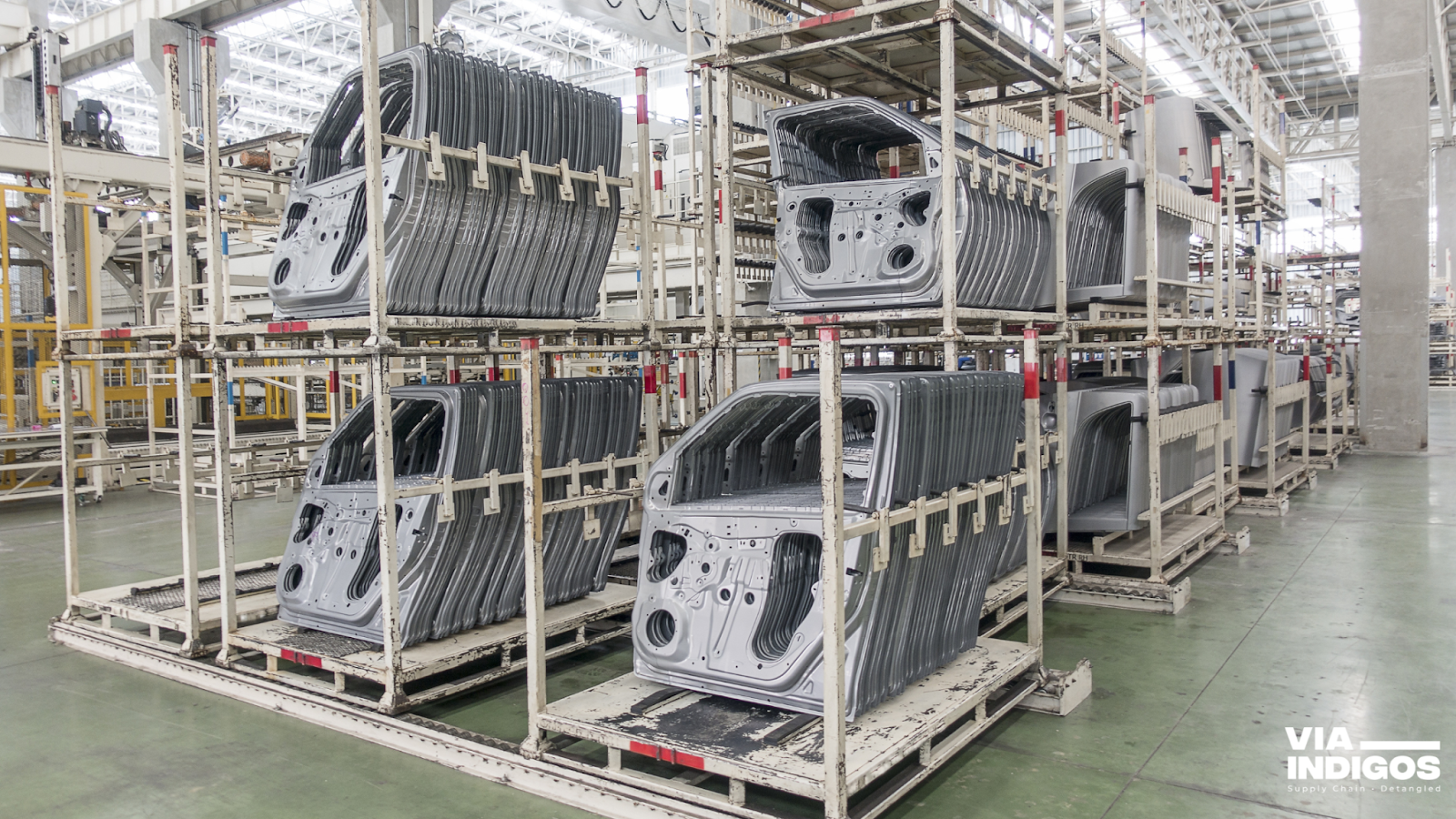
Maximized efficiency: Optimize material usage for cost-effective fabrication.
Monitor Inventory in Real-Time
Real-time inventory tracking helps manufacturers avoid material shortages or overstocking, both of which can lead to inefficiencies and higher costs.
Key Strategies:
• Implement IoT Solutions: Smart sensors and software provide real-time updates on material levels.
• Analyze Usage Patterns: Regularly review consumption data to predict future needs accurately.
• Streamline Reordering: Automated alerts ensure timely replenishment of materials, preventing production delays.
By focusing on material optimization, manufacturers can reduce waste, lower costs, and demonstrate environmental responsibility to their clients.
Efficient use of materials not only reduces waste but also helps prevent errors.
Utilize Nesting Software
Nesting software optimizes cutting patterns to maximize material usage. This reduces waste and ensures precision during the cutting process.
Monitor Inventory in Real-Time
Track material usage and availability to avoid shortages or substitutions that could lead to errors and rework.
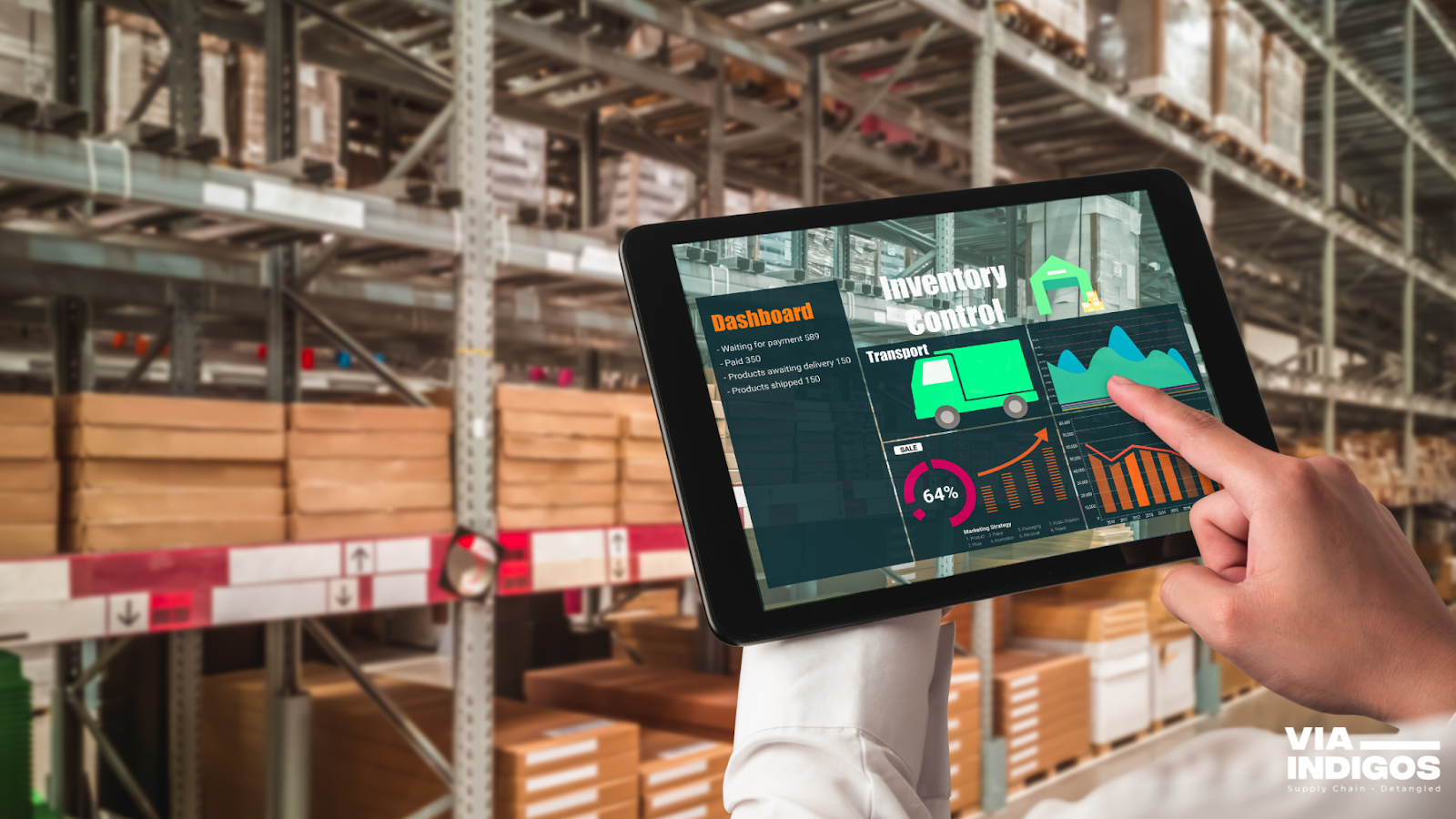
Real-time inventory tracking: Streamline supply and reduce downtime.
Plan for Post-Processing Early
Post-processing, such as finishing and assembly, is a crucial stage that significantly impacts the final product’s quality and appearance. Incorporating post-processing considerations into the design phase ensures smoother transitions and reduces the likelihood of errors or delays.
Simplify Finishing Requirements
Design parts that are easy to finish, avoiding features that complicate processes like powder coating, painting, or anodizing.
Tips for Simplification:
• Avoid Sharp Internal Corners: Rounded corners allow for more even application of finishes.
• Design for Accessibility: Ensure that all surfaces are easy to reach during finishing.
• Minimize Secondary Operations: Reduce the need for additional grinding, sanding, or polishing.
Coordinate with Vendors
Collaborating with finishing vendors early in the design phase helps align expectations and capabilities, ensuring a smoother post-processing phase.
Vendor Coordination Best Practices:
• Provide Clear Specifications: Share detailed design drawings and finishing requirements with vendors.
• Align on Timelines: Coordinate schedules to ensure post-processing does not delay overall production.
• Review Samples: Request sample finishes to confirm quality before full-scale production.
By planning for post-processing during the design phase, manufacturers can avoid common pitfalls, reduce rework, and deliver high-quality products efficiently.
Post-processing steps, such as finishing and assembly, should be considered during the initial design phase.
Simplify Finishing Requirements
Design parts with post-processing in mind. Avoid tight corners or hard-to-reach areas that complicate surface treatments like powder coating or anodizing.
Coordinate with Vendors
Work closely with finishing vendors to ensure your designs align with their capabilities, reducing the risk of errors during this stage.
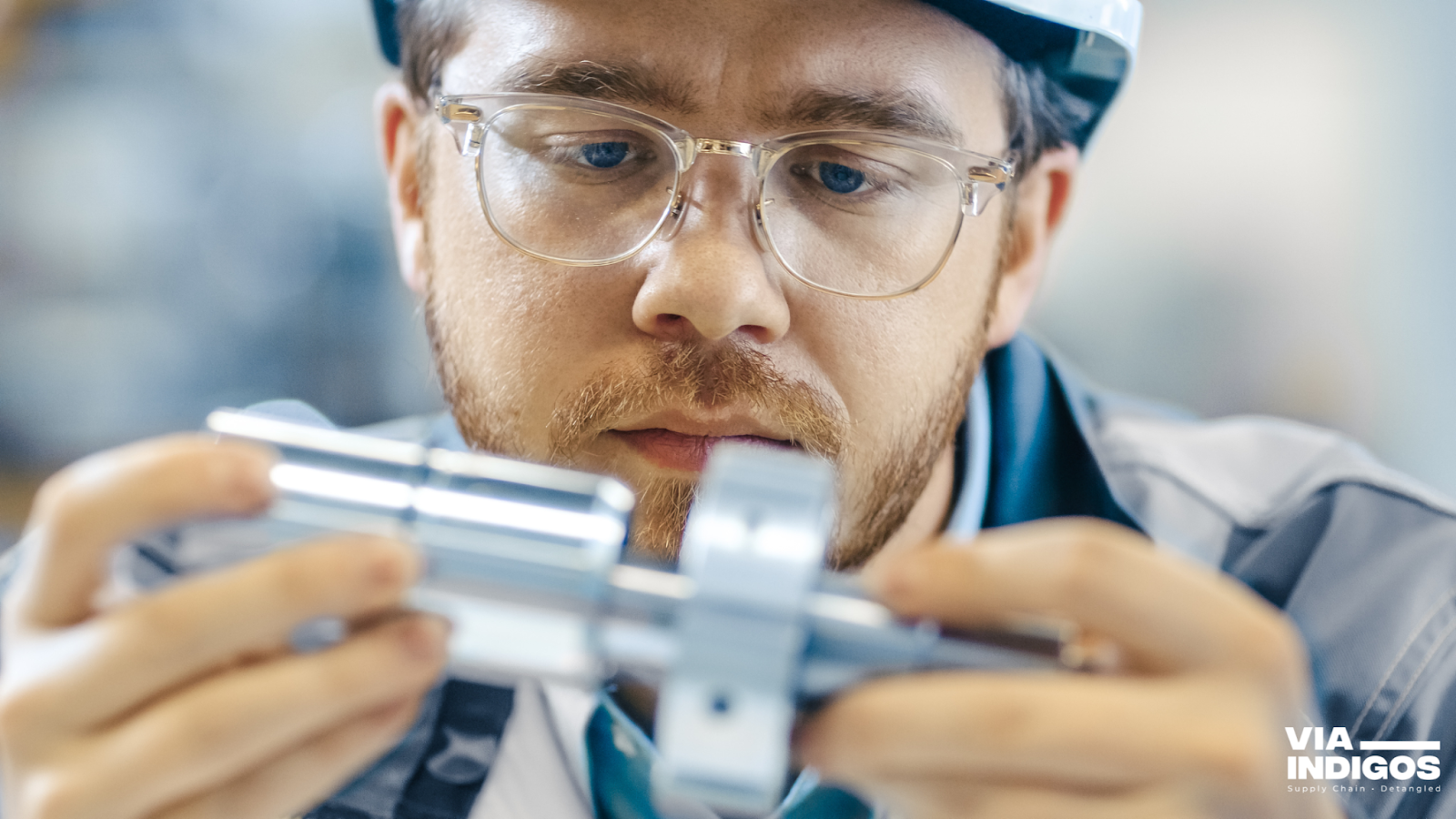
Attention to detail: Post-processing for flawless finishes and assembly.
Embrace Continuous Improvement
Continuous improvement is a fundamental principle for staying competitive in the dynamic field of sheet metal fabrication. By consistently analyzing processes and adopting innovative solutions, manufacturers can reduce inefficiencies and enhance overall performance.
Analyze Rework Trends
Tracking and analyzing instances of rework provides valuable insights into recurring issues and their root causes. This data can guide process improvements and prevent similar errors in the future.
Key Metrics to Track:
• Error Frequency: Monitor how often specific defects occur.
• Cost of Rework: Calculate the financial impact of rework to prioritize improvements.
• Cycle Time Delays: Assess how rework affects production timelines.
Invest in Technology
Emerging technologies, such as automation, IoT, and machine learning, offer significant opportunities for improving fabrication processes.
Benefits of Technological Investments:
• Increased Precision: Automated machines reduce human error and maintain tighter tolerances.
• Enhanced Monitoring: IoT-enabled devices provide real-time data on equipment performance and material usage.
• Predictive Maintenance: AI-driven analytics can predict equipment failures before they occur, minimizing downtime.
Adopting a mindset of continuous improvement ensures long-term success and positions manufacturers as leaders in quality and efficiency.
A culture of continuous improvement drives innovation and reduces inefficiencies over time.
Analyze Rework Trends
Regularly review instances of rework to identify patterns and root causes. Use this data to refine processes and prevent similar issues in the future.
Invest in Technology
Adopting advanced technologies, such as automated machinery and IoT-enabled tracking systems, enhances precision and efficiency.
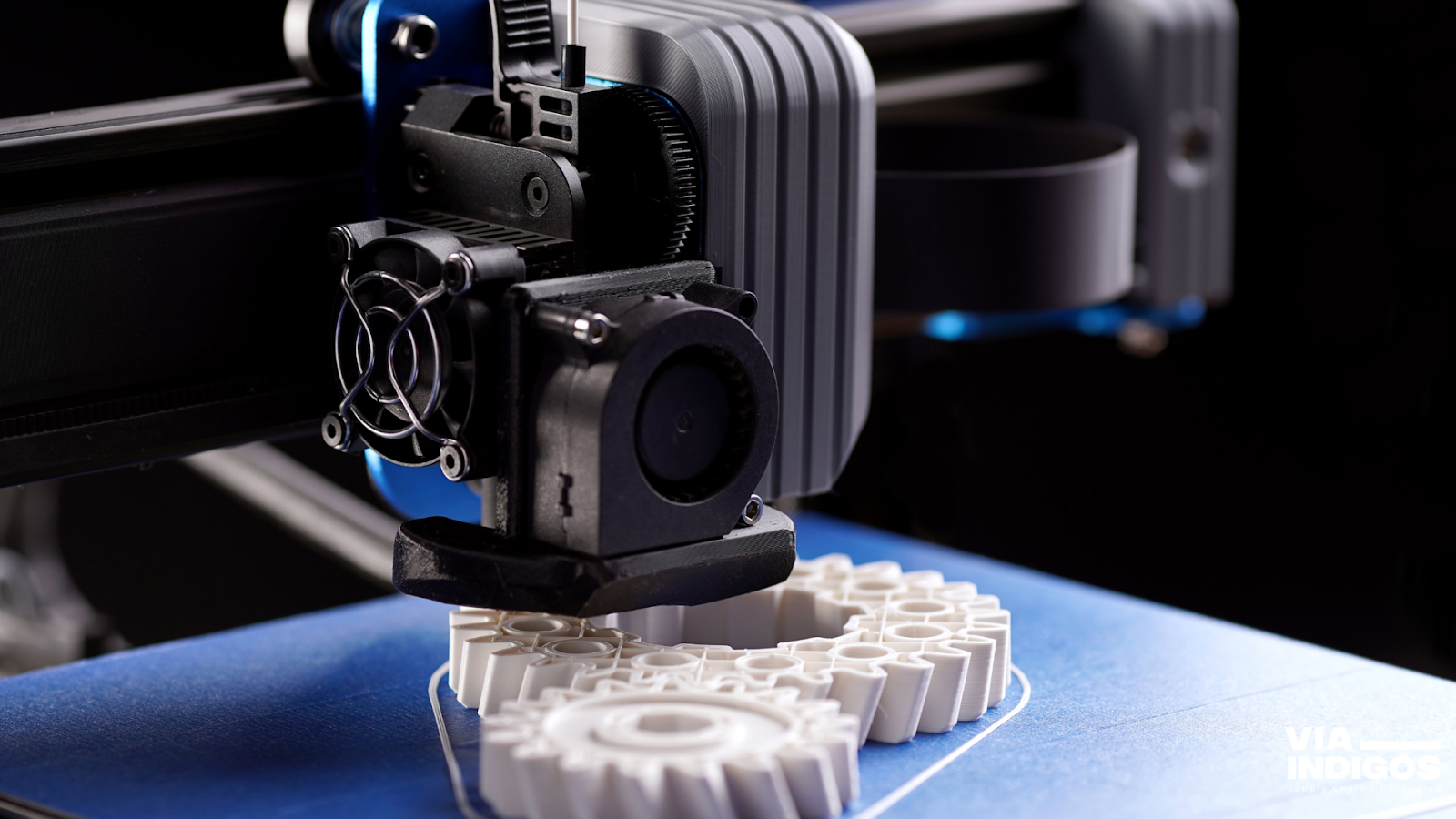
Advanced technology at work: Driving precision, efficiency, and innovation.
Deliver Excellence Through End-to-End Accountability
From initial design to final delivery, every step in the fabrication process plays a role in minimizing rework. By fostering a culture of accountability, empowering teams with the right tools, and maintaining an unwavering commitment to quality, you can ensure consistent success in sheet metal fabrication projects.
Ownership at Every Stage
When each phase—design, prototyping, material selection, fabrication, and assembly—operates in silos, errors slip through the cracks. A seamless handover process between teams ensures that designs are manufacturable, materials meet specifications, and production lines follow precise standards. This interconnected accountability minimizes the risk of costly rework.
For instance, when design engineers collaborate closely with production teams, they can proactively address manufacturability concerns, avoiding unnecessary design revisions later in the process. Similarly, by involving quality control at multiple checkpoints, defects are caught early, preventing cascading issues during final assembly.
Supplier and Vendor Accountability
A robust supply chain is as important as internal processes. At VIA INDIGOS, our boots on the ground approach means our teams physically oversee manufacturing, vet suppliers thoroughly, and ensure compliance with the required standards. By managing vendors directly and monitoring their performance, we eliminate inconsistencies that could lead to production errors.
This hands-on approach minimizes miscommunication, guarantees materials and components meet exact specifications, and strengthens overall supply chain resilience. By implementing our China +1 strategy, we diversify manufacturing sources, reducing dependency and unlocking tariff benefits that drive down costs. This not only safeguards quality but also enables businesses to cut import duties by up to 25%, boosting profitability and ensuring sustainable growth.
Full Visibility Across the Process
End-to-end accountability means visibility across the entire fabrication journey. Real-time tracking systems, IoT-enabled monitoring, and digital project management platforms allow manufacturers to stay informed about production progress, material consumption, and potential bottlenecks. This level of insight enables rapid adjustments and keeps projects aligned with deadlines.
For example, integrating IoT into fabrication equipment helps track machine performance and preempt maintenance needs, reducing downtime and preventing defects that lead to rework. Additionally, centralized platforms for design approvals and project updates keep all stakeholders informed, fostering transparency across departments.
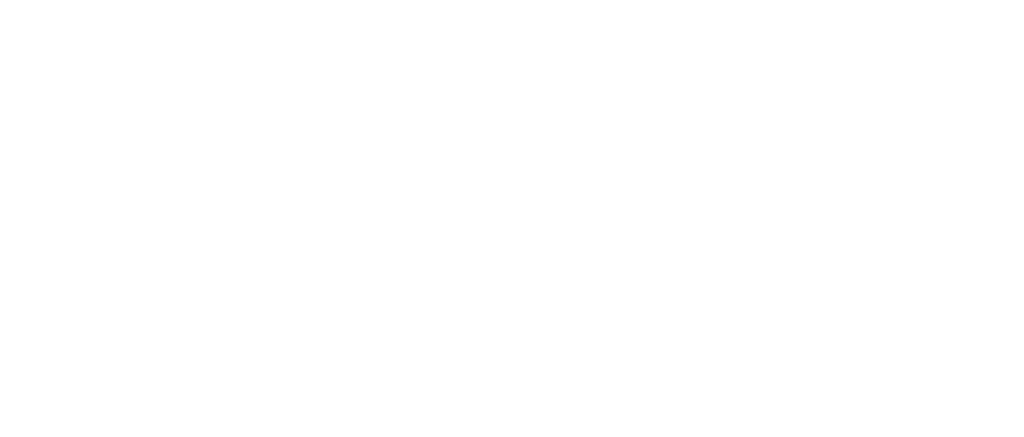
With boots on the ground and a vast network of production partners in INDIA, we help you cut tariffs, reduce lead times and avoid supply chain disruptions.
Why VIA INDIGOS for Fabrication and Manufacturing?
At VIA INDIGOS, we connect businesses to the heart of India’s manufacturing ecosystem, providing end-to-end fabrication and supply chain management that reduces costs and accelerates production. From sheet metal fabrication to casting, forging, and injection molding, we deliver parts that align with your specifications, timelines, and budget.
We’re not just another supplier—we’re your boots on the ground, ensuring quality from design to delivery. By leveraging India’s manufacturing strengths and implementing China +1 strategies, we help you bypass tariffs, avoid bottlenecks, and diversify your supply chain for long-term resilience.
What Sets VIA INDIGOS Apart?
• Strategic Manufacturing Advantage: India-based production for cost savings, tariff reductions, and uninterrupted supply.
• Certified and Compliant: Our production partners meet ISO 9001, IATF 16949, and other global quality standards.
• Material and Process Expertise: From sheet metal and casting to precision machining, we source the right materials for performance and durability.
• End-to-End Oversight: We manage everything—from supplier vetting to production, inspection, and logistics—so you don’t have to.
• On-Ground Teams: Our teams in India oversee every stage, ensuring your parts are manufactured with precision and delivered on time.
At VIA INDIGOS, we’re not just a link in the chain—we manage the entire process, providing seamless fabrication solutions that cut costs without compromising quality.